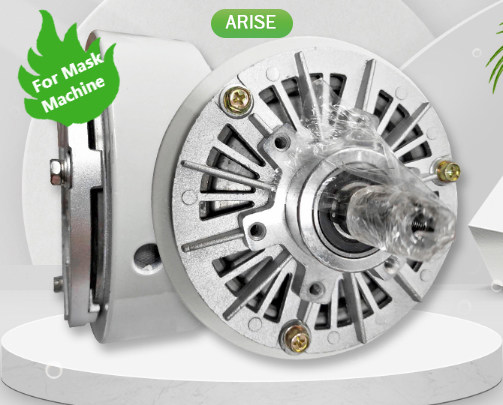
Magnetic Powder Brake
The magnetic powder brake is based on the electromagnetic principle, utilizing the magnetic powder to transfer torque.
It has the advantages of fast response speed, simple structure, no pollution, low noise, no impact vibration, energy saving.
It has been widely used in papermaking, printing, plastic, rubber, textile, printing and dyeing, wire and cable, metallurgy, and other unwinding and winding tension control in the coiled processing industry.
Why Select Magnetic Powder Brake
1. Boasting high-precision and wide torque control capabilities, this system ensures precise control by proportionally adjusting the transmitted torque in accordance with the exciting current.
2. With outstanding durability, the magnetic powder clutch brake offers a long service life and exhibits resistance to heat, abrasion, oxidation, and corrosion.
3. Enjoying high stability, this powder clutch brake maintains fixed torque characteristics and stable binding force between powder particles. Its sliding torque remains consistent, unaffected by relative RPM changes, thus ensuring constant torque.
4. Facilitating continuous sliding operations, this magnetic powder clutch features excellent heat dissipation and adopts a cooling structure that minimizes thermal deformation. Thanks to its high heat resistance, it delivers a reliable connection, braking, and sliding power, ensuring smooth operation without vibration.
5. Offering minimal impact during smooth transitions, this powder brake enables startup and stops without jolts or shocks.
6. Tailored for high-frequency operations, this system boasts fast response speeds and incorporates a specialized heat dissipation structure.
7. Lightweight and maintenance-free, this system utilizes high-temperature-resistant coils and special grease bearings. Additionally, it applies special wear-resistant treatments to armature components prone to wear.
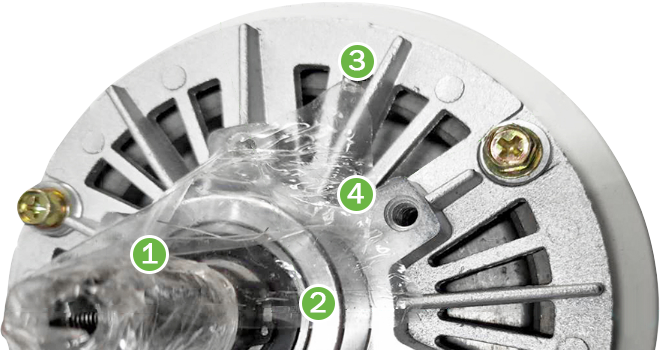
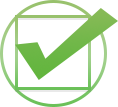
1. Quick Response
Alloy magnetic powder with superior heat resistance. Stable output torque.Work at high frequency.
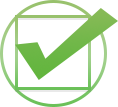
2. Superior Performance
High-temperature resistant material coils and high-quality bearings.Smooth operation. No impact.Low noise.
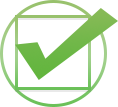
3. Overload Protection
Automatic slip in case of torque overload. Protect in overload situation and extend service life.
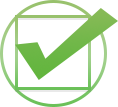
4. Anti-rust Protective Film
Carefully wrapped with plastic transparent film to prevent oil stains from penetrating’and scattering. Safe and secure.
Working Principle Of The Magnetic Powder Brake
1: The powder brake adopts a magnetic powder as a medium, a magnetic particle chain is formed to transmit torque with power on, which is mainly composed of an inner rotor, outer rotor, magnetic coil and magnetic powder.
2: When the coil is not powered, the active rotor rotates, due to the action of centrifugation, the magnetic powder is smashed on the inner wall of the active rotor and there is no contact between the magnetic powder and the driven rotor, the active rotor idling.
3: After the DC power is powered on, the electromagnetic field is generated and the magnetic particle chain is formed by the magnetic particle of the working medium under the action of magnetic lines. The inner rotor and the outer rotor are connected, thus achieving the purpose of transmitting, braking torque.
Applications Of The Magnetic Powder Brake
- Buffer start, and stop with the smooth characteristics and the constant torque
- Continuous sliding, tension control
- Torque Limiter
- High-speed response requirement
- Power absorption
- Positioning stop
- Simulated load
Installation And Use Of The Magnetic Powder Brake
The magnetic powder brake operates using DC as its excitation power supply. The drive shaft of a magnetic particle brake should be installed horizontally, with a permissible deviation of +0.03 mm for the mounting of the drive shaft and the axis of the shaft. It is not compatible with radial bearing main power transmission installation methods.
For initial use, the magnetic powder brake should be powered off after 10 seconds of operation, followed by powering on repeatedly to ensure the fluidity and even distribution of magnetic particles. It is crucial not to exceed the normal torque and rotation speed limits during operation, as doing so will significantly decrease the lifespan of the magnetic powder.