The Vital Role of Tension Sensors in Precision Engineering
The precise measurement of tension plays a crucial role in ensuring product quality, operational efficiency, and safety. Tension sensors, also known as tension transducers or load cells, are fundamental instruments used to gauge the force applied to an object by measuring the tension in a material or structure. This article delves into the essence of tension sensors, unraveling their significance, workings, and evolution in the modern technological landscape.
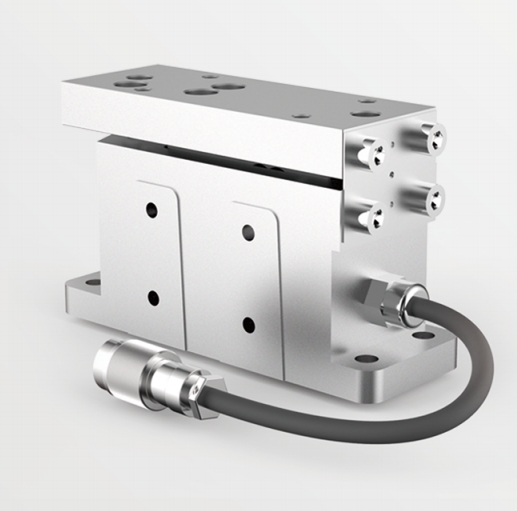
Understanding Tension Sensors
At their core, tension sensors are instruments designed to measure the force or tension applied to an object or material. Whether it’s monitoring the tension in a conveyor belt, a surgical suture, or an aircraft cable, these sensors provide invaluable insights into the mechanical dynamics of various systems.
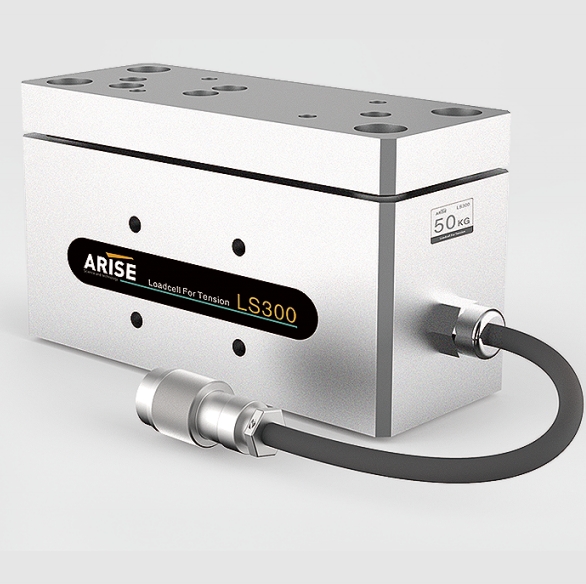
Working Principles of Tension Sensors
Tension sensors operate on various principles, each tailored to specific applications and requirements.
1. Strain Gauge Technology
This method is one of the most widely used in tension sensors. It relies on the principle that the electrical resistance of a conductor changes when it is stretched or compressed. In tension sensors, thin metallic foil patterns called strain gauges are bonded to a flexible substrate. When tension is applied to the sensor, the strain gauges experience deformation, causing a change in their electrical resistance. This change in resistance is proportional to the applied force or tension and is measured using Wheatstone bridge circuits or similar techniques.
2. Load Cell Designs
Load cells are transducers that convert mechanical force into electrical signals. They typically consist of a mechanical element, such as a bending beam, diaphragm, or shear beam, and strain gauges bonded to the element. When tension is applied to the load cell, the mechanical element deforms, causing a change in the strain gauge’s resistance. This change in resistance is then converted into an electrical signal proportional to the applied force.
3. Piezoelectric Effect
Some tension sensors utilize materials with piezoelectric properties. Piezoelectric materials generate an electric charge in response to mechanical stress. When tension is applied to the sensor, the piezoelectric material deforms, producing a voltage output proportional to the applied force. This voltage signal can be measured and used to determine the tension in the material.
4. Capacitive Sensing
Capacitive tension sensors measure the change in capacitance between two conductive plates as tension is applied to the sensor. When tension is applied, the distance between the plates changes, altering the capacitance. By measuring this change in capacitance, the tension in the material can be determined.
5. Magnetic Induction
In magnetic induction tension sensors, a magnet and a coil are used to measure the tension in a material. When tension is applied, it causes a change in the magnetic field between the magnet and the coil, inducing a voltage in the coil. This induced voltage is proportional to the applied force and can be measured to determine the tension in the material.
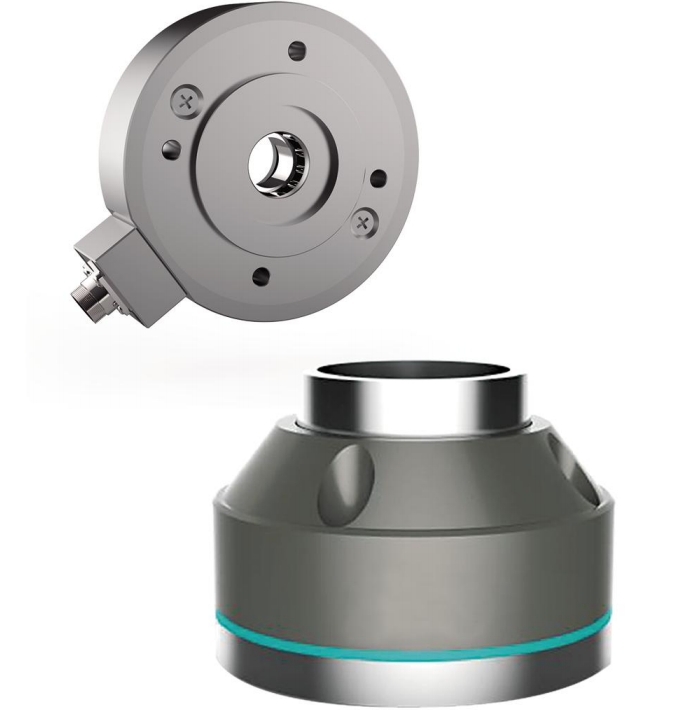
Applications Across Industries of Tension Sensors
Tension sensors are versatile instruments with applications across various industries, playing a pivotal role in monitoring and controlling tension or force in different materials and structures.
1. Manufacturing Industry
- Textile Production: Tension sensors are crucial for maintaining the proper tension in fibers and yarns during spinning, weaving, and knitting processes, ensuring the quality and integrity of the textile products.
- Papermaking: In paper manufacturing, tension sensors help control the tension in the paper web as it moves through various stages of production, including forming, pressing, and drying, to prevent wrinkles, tears, and other defects.
- Printing: Tension sensors are used in printing presses to regulate the tension of the paper or substrate, ensuring accurate registration of colors and preventing misfeeds or jams.
- Film and Foil Processing: Tension sensors are employed in processes such as film stretching, slitting, and laminating to maintain uniform tension, resulting in consistent product quality and performance.
2. Automotive Industry
- Timing Belt Tensioning: Tension sensors are utilized to monitor and adjust the tension in timing belts, ensuring proper timing and synchronization of engine components for optimal performance and efficiency.
- Drive Belt Tensioning: In vehicles with accessory drive belts, tension sensors help maintain the correct tension to prevent slippage and premature wear, extending the lifespan of the belts and associated components.
- Suspension Systems: Tension sensors are used in suspension systems to measure the tension in cables, springs, and dampers, providing feedback for adaptive suspension systems and active safety features.
3. Aerospace Industry
- Aircraft Structures: Tension sensors play a critical role in aircraft assembly and maintenance, ensuring precise tension in cables, wires, and composite materials used in airframes, wings, and control surfaces.
- Parachute Deployment: Tension sensors are integrated into parachute deployment systems to monitor the force applied during deployment, ensuring safe and controlled descent during emergency situations.
- Satellite Deployment: Tension sensors are used in the deployment mechanisms of satellite payloads to ensure the proper deployment of solar panels, antennas, and other components in the zero-gravity environment of space.
4. Medical Industry
- Surgical Robotics: Tension sensors are incorporated into surgical robotic systems to provide haptic feedback to surgeons, allowing them to accurately control the force applied during minimally invasive procedures such as laparoscopy and robotic-assisted surgery.
- Prosthetics and Orthotics: Tension sensors are utilized in prosthetic limbs and orthotic devices to monitor the tension in artificial muscles, tendons, and joints, providing users with natural and responsive movement.
5. Material Handling and Packaging Industry
- Conveyor Systems: Tension sensors are essential for maintaining proper tension in conveyor belts, chains, and rollers, ensuring smooth and efficient material handling in industries such as logistics, warehousing, and distribution.
- Packaging Machinery: Tension sensors are integrated into packaging machines to control the tension of packaging materials such as film, tape, and strapping, ensuring secure and uniform packaging of products.
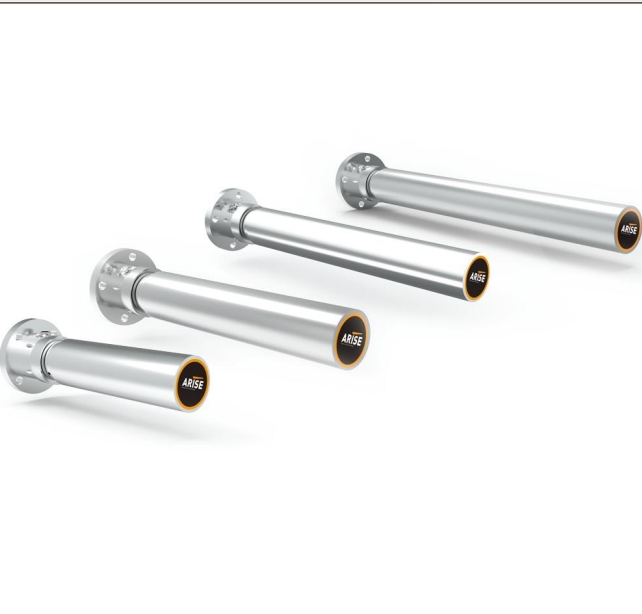
Notable Advancements in Tension Sensors
Recent advancements in tension sensor technology have brought about significant improvements in accuracy, reliability, versatility, and integration capabilities.
1. Miniaturization
- Advancements in microfabrication techniques have led to the development of miniaturized tension sensors with reduced size and weight.
- Miniaturization enables the integration of tension sensors into compact devices, wearable technology, and microsystems for applications in healthcare, robotics, and consumer electronics.
- Smaller sensors offer greater flexibility and accessibility in monitoring tension in confined spaces or on small-scale components.
2. Wireless Connectivity
- Integration of wireless communication capabilities allows tension sensors to transmit data without the need for physical wiring.
- Wireless connectivity enables real-time monitoring of tension in remote or inaccessible locations, facilitating predictive maintenance and optimization of systems.
- Tension sensors with wireless capabilities can be integrated into IoT (Internet of Things) platforms, enabling seamless integration with data analytics, cloud storage, and control systems.
3. Multi-Axis Sensing
- Modern tension sensors are capable of measuring tension in multiple axes simultaneously, providing comprehensive data for complex applications.
- Multi-axis sensing allows for the precise measurement of tension in three-dimensional structures, such as robotic arms, suspension bridges, and aerospace components.
- Tension sensors with multi-axis capabilities offer enhanced versatility and accuracy in dynamic and multidirectional force measurement applications.
4. Smart Sensing Algorithms
- Advanced signal processing algorithms have been developed to enhance the accuracy and reliability of tension measurements.
- Smart sensing algorithms compensate for environmental factors, nonlinearities, and dynamic changes in tension, resulting in more robust and stable performance.
- Machine learning and AI techniques are being applied to analyze sensor data, identify patterns, and predict tension variations, enabling proactive maintenance and optimization strategies.
5. Integration with IoT and Industry 4.0
- Tension sensors are increasingly being integrated into IoT-enabled systems as part of Industry 4.0 initiatives.
- IoT integration allows for seamless data collection, analysis, and visualization of tension measurements across the entire manufacturing or production process.
- Integration with IoT platforms enables predictive maintenance, remote monitoring, and adaptive control of tension in real time, leading to improved efficiency and productivity.
6. Enhanced Material Properties
- Advances in materials science have led to the development of new materials with enhanced mechanical properties for tension sensors.
- Novel materials offer improved sensitivity, durability, and stability under harsh operating conditions, expanding the range of applications for tension sensing technology.
- Composite materials and nanomaterials are being explored for their potential to further enhance the performance and functionality of tension sensors.
Conclusion
Tension sensors, though often unseen, are the unsung heroes of precision engineering, ensuring that the invisible threads of tension are carefully monitored and controlled across industries. As technology continues to evolve, advancements in sensor design, materials, and data processing capabilities will further enhance their performance and expand their range of applications, contributing to improved efficiency, safety, and quality in numerous sectors.