Real-time Monitoring in Printing Inspection
In today’s highly competitive printing market, the demand for flawless print quality and minimal waste is greater than ever before. As printing speeds grow and the expectations of customers become more higher, the traditional post-process printing inspections are no longer enough. Real-time monitoring in printing inspection makes use of advanced sensors, AI-powered vision systems and automated feedback loops that detect and correct defects as they happen, which reduces waste and improves efficiency.
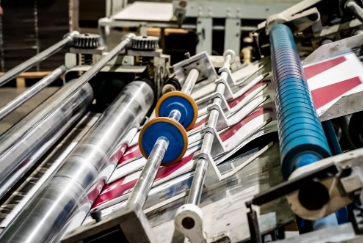
Table of Contents
Why Real-time Monitoring is Essential in Printing Inspection
Through continuous evaluation of the printed material during its production, this real-time monitoring technology ensures that defects are caught and addressed instantly rather than after the damage is done.
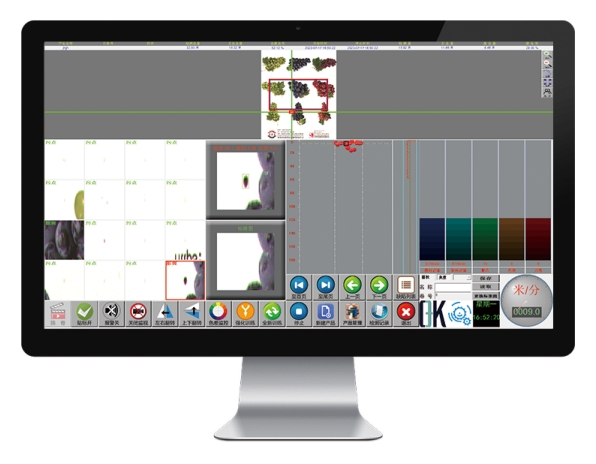
Minimizing Waste and Reducing Costs
Traditional inspection techniques depend on post-process inspections or random sampling. This could allow for defects to be missed until large quantities of material are printed. Monitoring in real-time prevents this from happening by identifying issues before they arise. It doesn’t matter if it’s a label that’s not aligned or color inconsistency or a printing streak the moment it is discovered, the corrective action is immediately taken to stop waste from accumulating. This drastically reduces material losses and reduces the need for reprints and optimizes use of resources throughout manufacturing.
Ensuring Consistent Print Quality
In the food industry, such as packaging, pharmaceuticals and commercial branding, consistency is not a matter of debate. Monitoring in real-time provides continuous supervision to ensure that each millimeter of printed output meets the highest quality standards. It eliminates variation between printing batches, helps to maintain brand integrity and guarantees that the printing process is in compliance with strict regulations. minor mistakes can cause serious harm.
Enhancing Production Efficiency
In conjunction with printing equipment, real-time monitoring systems can speed up the process. These web inspection systems in the printing operations, let printers perform at a high speed without compromising quality. Automatic detection and alert functions remove the need for inspections by hand at different points, allowing the workers to concentrate on producing instead of visual inspections. In environments with high volumes this leads to increased productivity and lower labor costs.
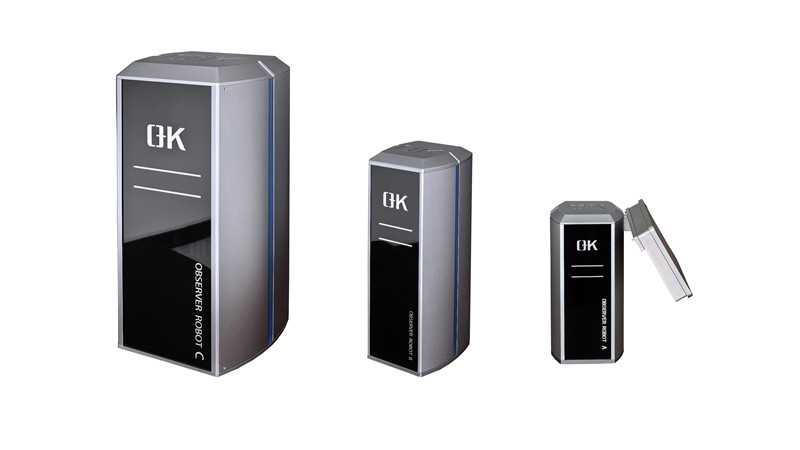
Enabling Immediate Corrective Action
One of the most distinctive characteristics in real-time tracking is the ability to provide instant feedback. When a defect is identified the system can notify to the operator, document the issue and in some instances alter the machine’s settings or even stop the line completely. The ability to respond immediately reduces downtime and helps avoid sending damaged products out to consumers, keeping business relationships intact and ensuring confidence in the brand.
Supporting Data Traceability and Process Optimization
Modern real-time monitoring systems typically have advanced technology for data logging. Each print inspection is recorded, resulting in an extensive record of the quality metrics, conditions of production and the identified defects. This data allows the analysis of root causes, continuous process improvement, and also audits of regulatory compliance. In time, this information is a valuable resource in improving printing performance and preventing the occurrence of problems.
Keeping Pace with Industry Trends
As the market shifts towards short print times, more customized packaging, and quicker delivery times The margin for error shrinks. Monitoring in real-time allows printing companies to adjust to changing trends by providing a solid quality control system that doesn’t hinder the process. It guarantees high performance when faced with increasing complexity and speed of production.
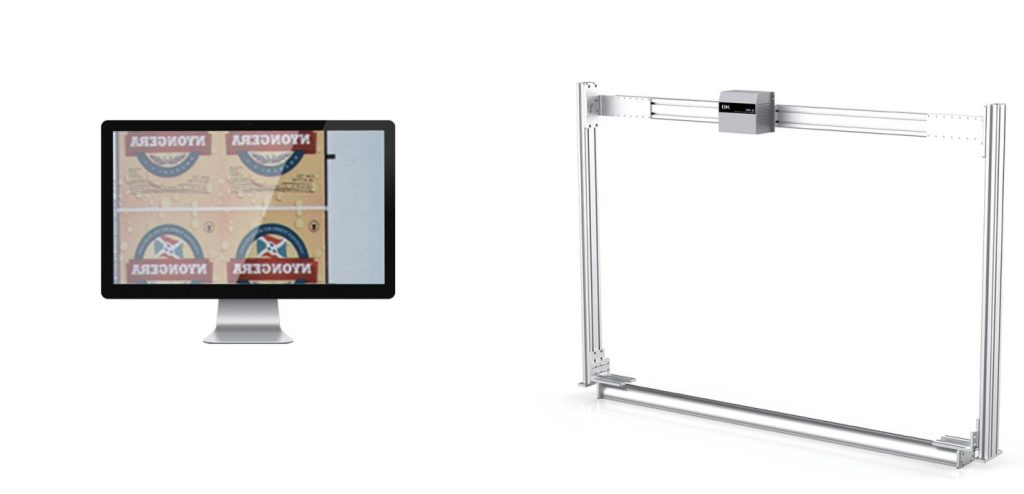
Core Technologies Enabling Real-time Monitoring in Printing Inspection
Real-time monitoring in printing inspection relies on a combination of advanced technologies that work to detect defects when they occur, which allows for prompt response and minimal waste.
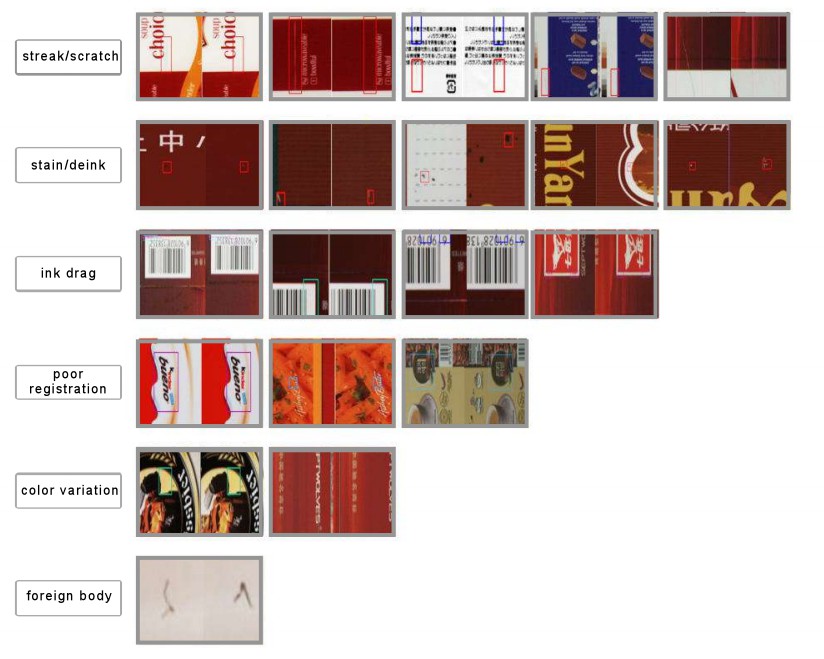
1. High-Resolution Line Scan and Area Scan Cameras
At the core of every real-time print inspection system is a high-resolution cameras, either the line or area. Line scanner cameras are especially suitable for continuous printing on web-based printers and can capture only one line at a given time with a high degree of accuracy. Area scanners, on the other hand, can capture full-frame photos and are employed in label or sheet-fed applications. Both cameras can run at high speed and have the necessary resolution for detecting even the tiniest print imperfections like smudges or ink spots or registration mistakes.
2. Advanced Illumination Systems
Lighting plays an important part in exposing imperfections in print and surface. Modern cameras employ LED-based illumination that can be programmed to use back-lighting, front-lighting or multi-angle lighting based on the print and substrate kind. Consistent and uniform illumination assures that the camera can capture exact representations of the printed image without blurring caused by shadows or glare. Certain systems employ the strobed LED light that is synchronized with shutters to capture high-speed images without blurring in motion.
3. Real-Time Image Processing Software
The image data that is captured can only be useful when it is quickly examined. The real-time processing program analyzes live images to predefined references – such in master template or artwork to identify any deviations. These algorithms analyze various quality metrics, such as alignment, color consistency with the print’s completeness, and overall readability. The latest software solutions are designed to process high-resolution information in milliseconds, allowing them to keep up even with the fastest printing lines.
4. Artificial Intelligence and Machine Learning
To decrease false positives and improve decision-making, many of the latest inspection systems have AI and machine-learning capabilities. These tools enable the system to differentiate the difference between acceptable deviations (like small color variations within the tolerance) and real defects (such as the wrong characters or incorrect content). In time AI “learns” from repeated patterns constantly improving its precision. AI also allows an adaptive inspection, by automatically altering parameters in response to environmental changes or other job requirements.
5. Edge Computing
In order to ensure that the performance is always in real-time, Many print inspection systems use edge computing, where the processing of data occurs near the point of origin (i.e. in the device or close to where the printer is). This helps eliminate latency issues that come with the transfer of large image data to remote servers or cloud storage. Edge processors can provide immediate alerts, autonomous decision making, and seamless connectivity with print presses to immediately corrective actions.
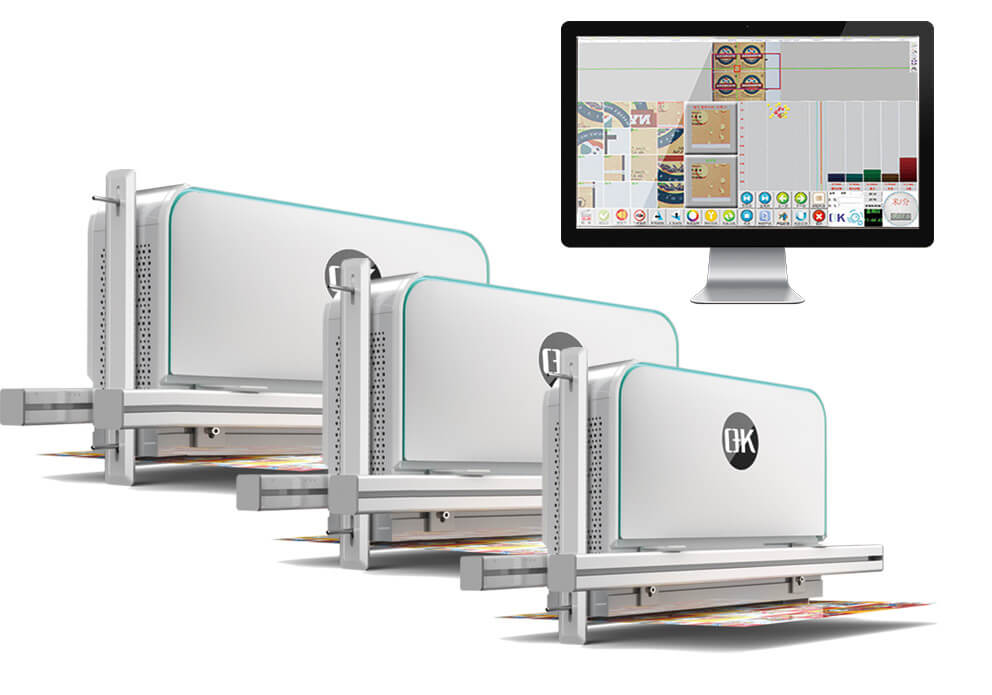
6. Closed-Loop Feedback Integration
Advanced systems do more than just identify problems, they act upon them. Closed-loop feedback allows an inspection device to directly communicate with the unit controlling the press. If there is a defect it can notify the press to stop or adjust parameters (e.g. the density of ink or alignment of the print head) or to reject the defective material downstream. This loop is automated, which significantly minimizes the need for operator intervention and guarantees an even quality throughout the entire production run.
7. Data Logging and Traceability Platforms
Another crucial aspect of real-time monitoring is extensive management of data. 100% printing inspection systems track every incident or defect and adjust in the course of a printing job. These logs can be traced to audits, quality report, and claims from customers. Software platforms that integrate often offer the visualization of dashboards as well as defect classification along with statistical analytics tools that assist manufacturers in making informed decisions to improve their products continuously.
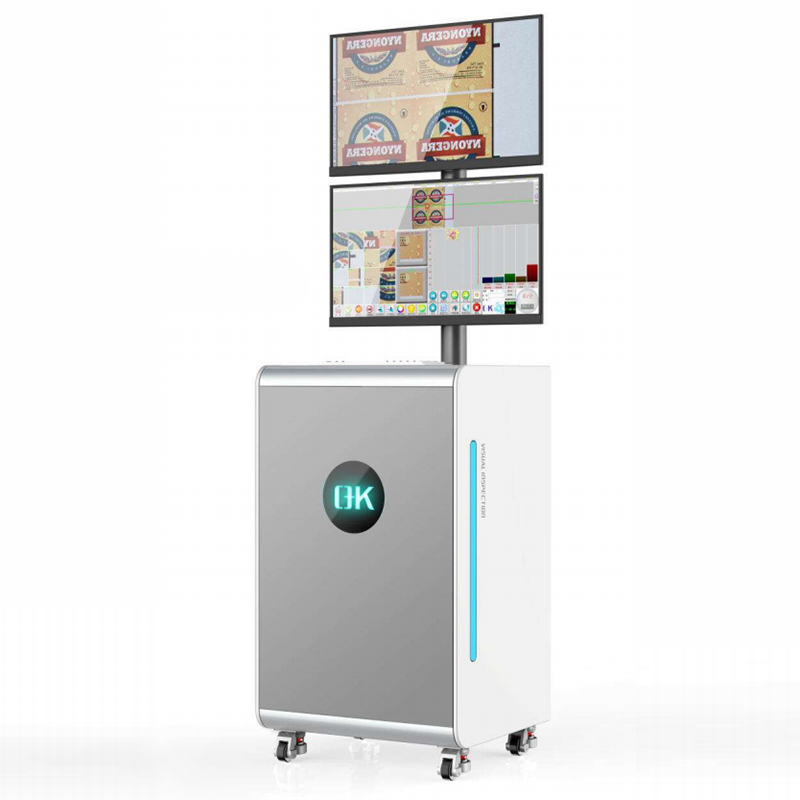
Applications of Real-time Monitoring Across the Printing Industry
Printing Sector | Application of Real-Time Monitoring | Key Benefits |
Packaging Printing | It detects color shifts, misregistration as well as barcode readability issues in rigid and flexible packaging | It ensures consistency of brand, decreases recalls, and increases the quality of compliance |
Label Printing | Monitors alignment of labels as well as text that is missing, and the integrity of serial numbers on high-speed lines | Reduces waste and assures exact product identification |
Pharmaceutical Printing | Examine the batch numbers and expiry dates as well as the regulatory information in the packaging and blisters | Improves patient safety and adheres to strict regulations |
Security Printing | Verifies the presence of anti-counterfeit elements like microtext, guilloche designs, and Holograms | Guards against counterfeits, brand and financial instruments |
Commercial Printing | It ensures consistency of color in registration accuracy, color consistency, and image clarity in catalogs and brochures. | Professional output, and client satisfaction |
Newspaper Printing | The system detects ghosting in the text as well as ink coverage variations and plate misalignment in real time. | Reduces production downtime, ensures timely distribution |
Corrugated Printing | Monitors the alignment of die-cut graphics and monitors die-cut graphics on corrugated boards during high-speed production | Minimizes rework time and material cost and improves legibility of print |
Flexible Film Printing | Film deformation, effects of tension and the integrity of prints on plastic films. | Reduces waste from film and increases the shelf-styling of your product |
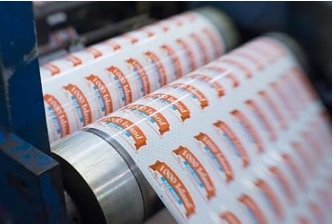
Challenges and Future Innovations in Real-time Monitoring for Printing Inspection
Challenges | Description | Future Innovations |
High Initial Investment | Real-time monitoring systems need expensive cameras, processors, as well as tools for integration. | The development of cost-effective and modular inspection solutions designed for smaller and mid-sized printers. |
Complex Calibration Requirements | Systems need to be adjusted to different substrates as well as inks and print kinds. | AI-driven auto-calibration changes parameters dynamically in real-time. |
False Positives and Missed Defects | Settings that are sensitive or too sensitive could miss mistakes or even flag prints that are acceptable. | Modern machine-learning algorithms can better discern between minor and critical imperfections. |
Integration with Legacy Equipment | A lot of older presses do not have the interfaces that are required to run modern real-time systems. | Plug-and-play, retrofit-friendly monitoring modules for older press lines. |
Data Overload and Management | Continuous monitoring creates huge quantities of defect and image information. | Cloud-based analytics platforms, with intelligent display and optimized storage. |
Operator Training and Interpretation | The ability to interpret warnings from inspections is usually required. | Friendly interfaces for users with guided diagnostics as well as automated correction suggestions. |
Variable Environmental Conditions | Variations in light or vibration can impact accuracy. | Environmentally-adaptive sensors and robust inspection enclosures. |
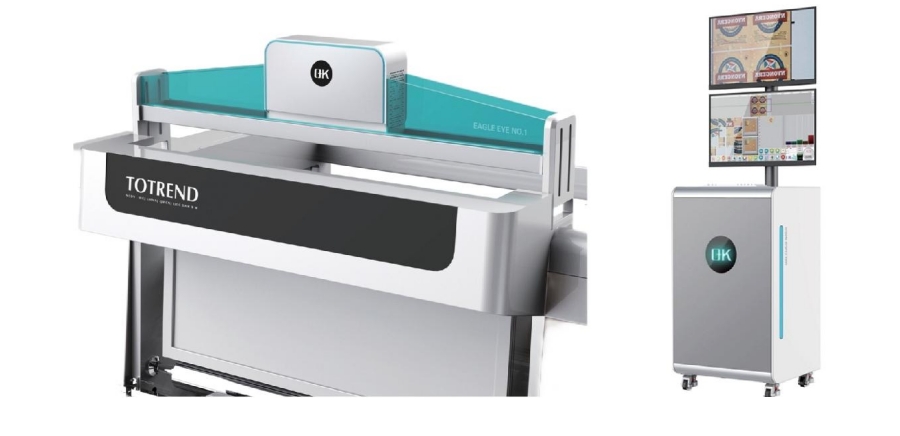
Summary
Real-time monitoring in printing inspection is not just a tool for quality control and it’s a key competitive advantage in print industry. Through combining speed, precision and intelligence, that allows printers to satisfy the stringent quality standards and reduce operating costs, providing consistent results on every printing job.