A Comprehensive Guide to Printing Inspection: Enhancing Quality Assurance
Ensuring product quality is paramount in the printing industry, where even the smallest imperfection can lead to significant repercussions. Printing inspection serves as a critical component in maintaining quality standards, enabling businesses to detect and rectify errors before they reach the hands of consumers. From packaging materials to labels and printed electronics, the importance of rigorous inspection processes cannot be overstated. In this article, we delve into the significance of printing inspection, its methodologies, challenges and innovative technologies, and the pivotal role it plays in maintaining quality assurance standards across industries.
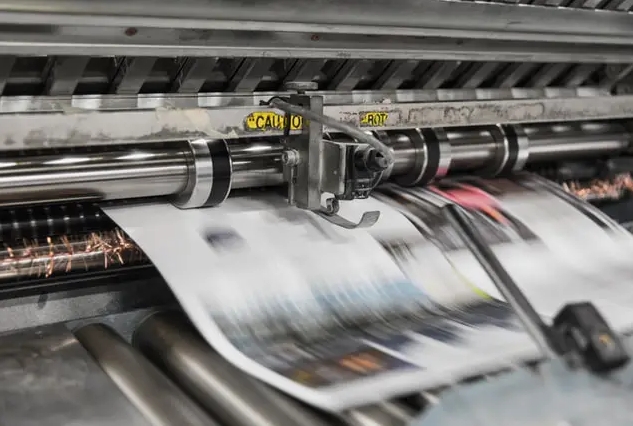
The Significance of Printing Inspection Across Different Sectors
Printing inspection holds immense importance in various industries where printed materials serve critical functions. Whether it’s packaging for consumer goods, labels for pharmaceutical products, or informational brochures, the quality and accuracy of printed materials directly impact brand reputation, consumer safety, and regulatory compliance.
1. Ensuring Quality and Consistency
In industries such as consumer packaged goods (CPG), cosmetics, and food and beverage, packaging plays a crucial role in brand identity and product presentation. Printing inspection ensures that packaging materials meet quality standards, including color accuracy, print clarity, and overall aesthetics. Consistent printing quality across packaging not only enhances brand perception but also instills trust and confidence in consumers.
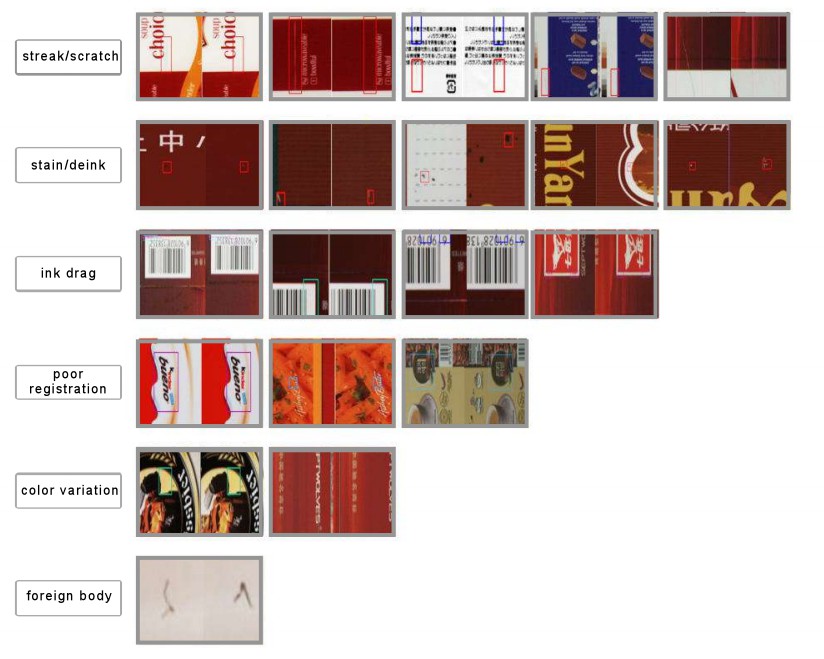
2. Compliance with Regulatory Standards
In highly regulated sectors like pharmaceuticals, medical devices, and food packaging, printing inspection is essential for ensuring compliance with stringent regulatory requirements. Printed materials in these industries often contain critical information such as dosage instructions, expiration dates, and safety warnings. Any inaccuracies or defects in printing could lead to serious consequences, including regulatory sanctions, product recalls, or compromised consumer safety.
3. Brand Protection and Reputation Management
For businesses across all industries, maintaining brand integrity is paramount. Printing inspection plays a pivotal role in safeguarding brand reputation by ensuring that printed materials align with brand guidelines and quality standards. Consistently high-quality printing reflects positively on the brand, reinforcing its image as reliable and trustworthy in the eyes of consumers.
4. Waste Reduction and Cost Savings
Printing defects can result in significant material wastage and production inefficiencies. By detecting errors early in the printing process, inspection systems help minimize waste, reduce rework, and optimize resource utilization. This leads to cost savings for manufacturers and contributes to overall operational efficiency.
5. Enhancing Consumer Experience
Printed materials serve as a means of communication between businesses and consumers. Whether it’s product labels, instruction manuals, or promotional materials, clear and accurate printing enhances the consumer experience. Printing inspection ensures that information is legible, coherent, and free from errors, thereby facilitating better understanding and usability of the product.
6. Supporting Sustainable Practices
In an era where sustainability is a growing concern, printing inspection contributes to environmentally responsible practices. By minimizing printing defects and waste, inspection systems help reduce the environmental footprint associated with print manufacturing. Additionally, by ensuring compliance with labeling regulations, printing inspection supports transparency and accountability in product information, which is increasingly important to environmentally conscious consumers.
Commonly Used Methods in Printing Inspection
Print inspection employs various methods and technologies to ensure the quality and accuracy of printed materials.
1. Visual Inspection
a. Manual Visual Inspection
- Human Operators: Trained personnel visually examine printed materials to identify defects such as misprints, smudges, color inconsistencies, and registration errors.
- Visual Comparison: Printed materials are compared against reference samples or design specifications to detect deviations and anomalies.
2. Automated Inspection Systems
a. Machine Vision:
- High-Speed Cameras: Utilize high-speed cameras to capture images of printed materials with exceptional detail and resolution.
- Image Processing Algorithms: Advanced algorithms analyze captured images to detect defects, such as misprints, streaks, or missing elements.
- Pattern Recognition: vision printing inspection systems recognize patterns and shapes, allowing for the detection of irregularities in printed text, graphics, or barcodes.
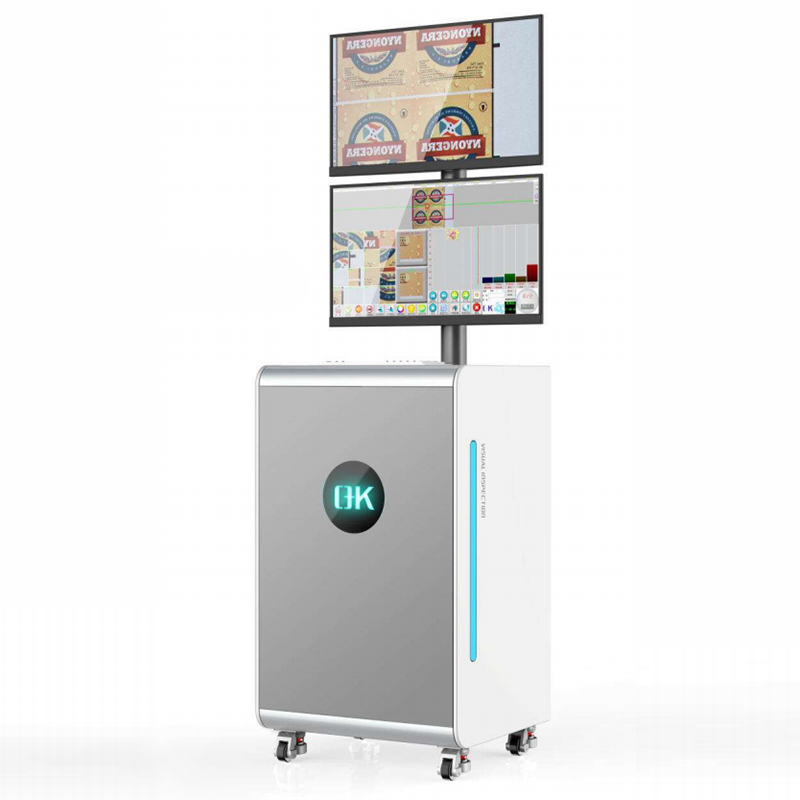
b. Optical Character Recognition (OCR) and Text Verification:
- OCR Technology: Optical character recognition technology extracts text from printed materials and compares it against predefined databases or templates to verify accuracy and completeness.
- Text Verification Algorithms: Algorithms analyze printed text for spelling errors, formatting inconsistencies, or missing information, ensuring readability and compliance with standards.
c. Color Measurement Devices
- Spectrophotometers: Measure spectral reflectance and transmittance properties of printed materials to assess color accuracy and consistency.
- Colorimeters: Provide objective color measurements based on human perception, verifying adherence to predefined color standards and specifications.
d. Barcode Verification Systems
- Barcode Scanners: Scan printed barcodes to verify readability, accuracy, and compliance with industry standards (e.g., GS1).
- Barcode Verification Software: Analyze barcode quality based on parameters such as bar width, contrast, and edge definition, ensuring compliance with ISO/IEC standards.
3. Digital Printing Inspection
a. Real-Time Inspection
- Inline Inspection Systems: Integrated directly into digital printing presses, these systems inspect printed output in real-time, enabling immediate feedback and adjustment.
- Printhead Monitoring: Monitor printhead performance and ink deposition during the printing process to detect issues such as missing ink droplets or printhead misalignment.
b. Post-Printing Inspection
Offline Inspection Systems: Analyze printed output after the printing process for defects or inconsistencies, allowing for batch-level inspection and quality control.
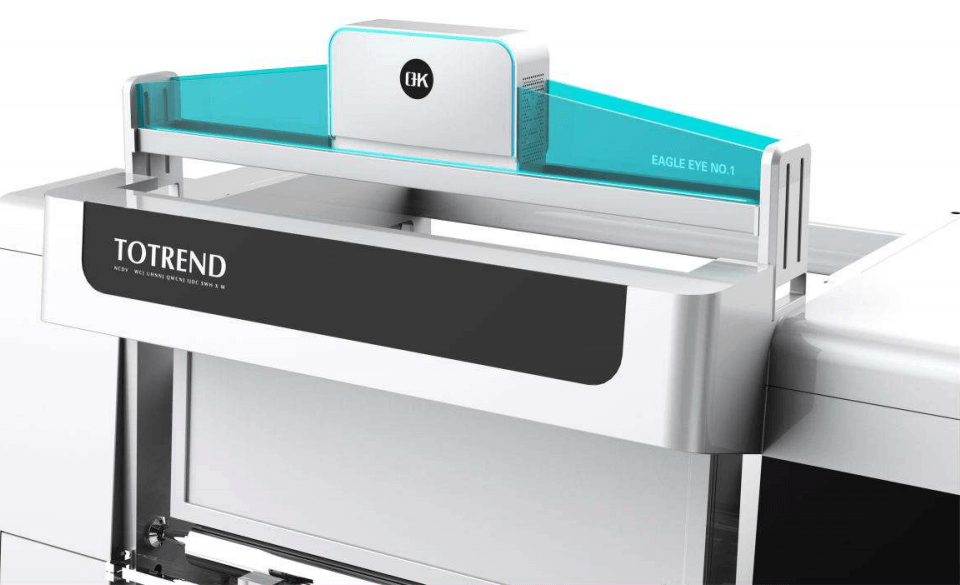
4. Statistical Process Control (SPC)
- Data Analysis: Utilize statistical methods to analyze printing process data and identify trends, variations, or abnormalities that may indicate potential printing defects.
- Control Charts: Monitor key process parameters over time and set control limits to ensure printing processes remain within acceptable bounds.
Challenges and Considerations in Printing Inspection
These challenges span technological, operational, and organizational aspects, and addressing them is essential for maximizing the effectiveness of print inspection processes.
1. Complexity of Print Processes
- Variability in Printing Technologies: Different printing technologies (e.g., offset, flexography, digital) have unique characteristics and requirements, making it challenging to develop universal inspection solutions that can accommodate all processes effectively.
- Diverse Substrates and Materials: Printing may occur on various substrates, including paper, plastics, metals, and textiles, each with its own surface properties and challenges for inspection systems to address.
2. Defect Detection and Classification
- Detection of Subtle Defects: Some printing defects, such as minor misregistrations, color variations, or fine print defects, can be challenging to detect, requiring advanced inspection technologies and algorithms with high sensitivity and specificity.
- Defect Classification and Prioritization: Once defects are detected, accurately classifying and prioritizing them based on severity and impact on product quality is essential for effective corrective action and resource allocation.
3. Speed and Throughput
- High-Speed Production Environments: In industries with high-speed printing processes, inspection systems must operate at high throughput rates to keep pace with production without causing bottlenecks or delays.
- Real-Time Inspection Requirements: Real-time inspection is critical for inline printing processes to detect defects as they occur and enable immediate corrective action. Achieving real-time inspection while maintaining accuracy and reliability can be challenging.
4. Integration with Production Workflow
- Integration Complexity: Integrating printing inspection systems into existing production workflows can be complex and may require customization to ensure seamless operation and minimal disruption to production schedules.
- Compatibility with Equipment and Software: Inspection systems must be compatible with various printing equipment and software platforms, requiring coordination and collaboration between different vendors and stakeholders.
5. Training and Expertise
- Operator Training: Training operators to use and interpret inspection systems effectively is crucial for maximizing their utility and ensuring accurate defect detection and classification.
- Technical Expertise: Maintenance and troubleshooting of inspection systems require technical expertise, including knowledge of optics, electronics, software, and data analysis techniques.
6. Cost and ROI
- Initial Investment: Implementing printing inspection systems involves significant upfront costs, including equipment acquisition, installation, training, and integration with existing infrastructure.
- Return on Investment (ROI): Demonstrating the ROI of printing inspection systems can be challenging, as it often involves quantifying the value of avoided defects, reduced rework, and improved product quality over time.
7. Data Security and Privacy
- Data Handling: Inspection systems generate large volumes of sensitive data related to production processes, product quality, and defect analysis, requiring robust data handling protocols to ensure confidentiality, integrity, and compliance with data privacy regulations.
- Cybersecurity: With increasing connectivity and digitization in manufacturing, ensuring the cybersecurity of inspection systems and protecting them from cyber threats, such as hacking or data breaches, is essential.
Innovative Technologies to Address the Challenges in Printing Inspection

1. Advanced Machine Vision Systems
- Deep Learning and AI: Utilizing deep learning algorithms and artificial intelligence (AI) techniques, machine vision systems can enhance defect detection capabilities by learning from large datasets and adapting to new printing environments. These systems can detect subtle defects and anomalies with higher accuracy and reliability.
- Convolutional Neural Networks (CNNs): CNNs are a type of deep learning algorithm specifically designed for image processing tasks. They can automatically learn features from printed images and classify defects based on learned patterns, improving the efficiency of printing inspection.
2. Real-Time Monitoring and Control
- IoT-enabled Sensors: Internet of Things (IoT) sensors embedded in printing equipment can monitor key process parameters in real-time, such as ink viscosity, temperature, and pressure. By continuously monitoring these parameters, printing processes can be optimized, and deviations from optimal conditions can be detected early, minimizing the risk of defects.
- Closed-Loop Control Systems: Closed-loop control systems use feedback from sensors to adjust printing parameters dynamically in real-time. For example, if a defect is detected during inspection, the system can automatically make adjustments to printing settings to correct the issue before further printing occurs.
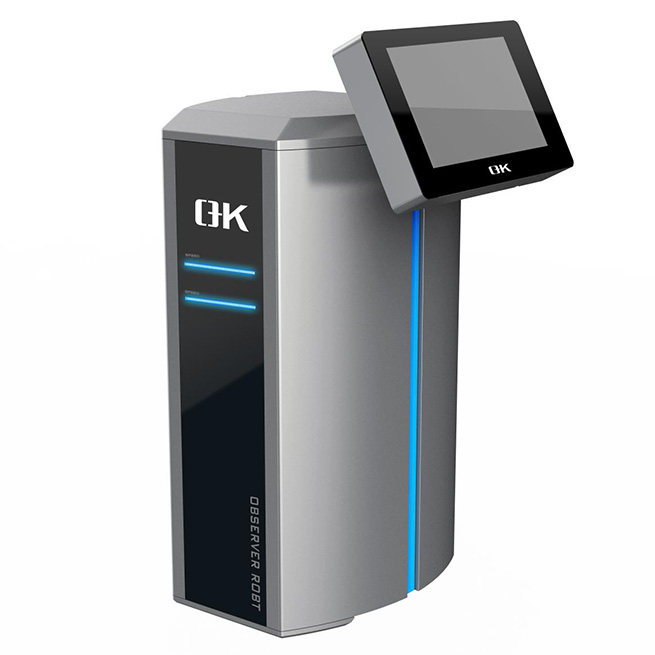
3. Multi-Sensor Fusion
- Integration of Multiple Inspection Techniques: Combining multiple inspection techniques, such as machine vision, spectroscopy, and thermal imaging, allows for comprehensive defect detection and characterization. By fusing data from different sensors, a more accurate and complete picture of printing quality can be obtained, enabling better decision-making and process control.
- Data Fusion Algorithms: Advanced data fusion algorithms integrate information from multiple sensors and sources to provide a holistic view of printing processes. These algorithms analyze and correlate data from different sources to identify patterns, trends, and anomalies, enabling more effective defect detection and root cause analysis.
4. Augmented Reality (AR) and Virtual Reality (VR)
- AR-assisted Inspection: AR technologies overlay digital information, such as defect locations or inspection guidelines, onto the real-world view of printed materials, assisting operators in visual inspection tasks. This enhances inspection accuracy and efficiency by providing real-time guidance and feedback.
- VR-based Training Simulations: VR simulations can be used to train operators in printing inspection tasks in a virtual environment. Operators can practice inspecting printed materials under various conditions and scenarios, improving their skills and confidence in performing inspection tasks accurately.
5. Blockchain for Traceability and Authentication
Blockchain Technology: Blockchain-based solutions can provide a secure and tamper-proof record of printing processes, including inspection results, quality data, and product traceability information. This ensures transparency, authenticity, and integrity throughout the supply chain, enhancing trust and accountability in printed products.
Conclusion
Printing inspection plays a pivotal role in upholding quality standards, driving operational efficiency, and ensuring regulatory compliance across diverse industries. Addressing the challenges and considerations in printing inspection requires a holistic approach that encompasses technological innovation, operational optimization, and organizational readiness. As the printing industry continues to evolve, investing in robust inspection practices and staying ahead of technological advancements will be instrumental in maintaining a competitive edge and driving sustained growth.