Advanced Imaging and Sensor Technologies for Printing Inspection Systems
In the printing industry, where precision, speed, and quality are vital, inspection systems have become indispensable. At the heart of printing inspection systems are sophisticated imaging and sensor technologies designed to detect, diagnose, and prevent defects in real-time. These technologies ensure consistent quality across a wide range of printing applications. As customer expectations and regulatory standards tighten, understanding the imaging and sensor technologies of print inspection systems is critical for manufacturers and print service providers.
Table of Contents
Key Imaging Technologies Used in Printing Inspection Systems
Printing inspection systems rely on a range of advanced imaging technologies that detect defects with high speed and precision.
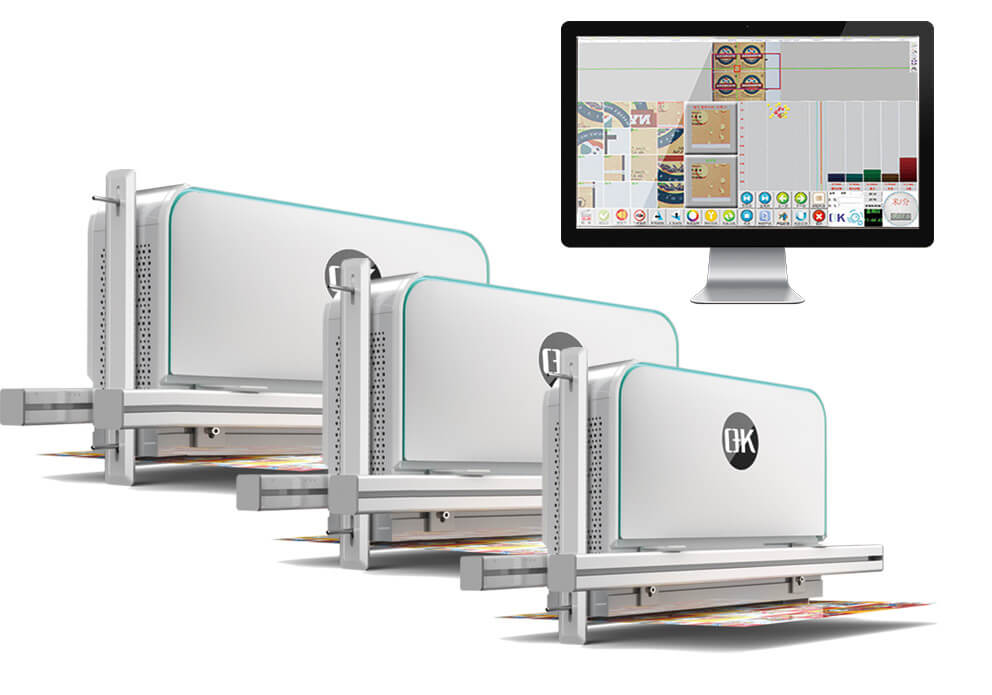
1. Line Scan Cameras
Line scan cameras are the cornerstone of inspection in web-based printing processes. These cameras capture a single row of pixels continuously as the printed material moves past the sensor. They are ideal for high-speed and high-resolution inspections of labels, flexible packaging, and newspapers. The seamless image construction and real-time analysis make them excellent for detecting defects like streaks, misalignment, smudges, and missing text across long production runs.
2. Area Scan Cameras
Area scan cameras capture full-frame, two-dimensional images in a single snapshot. These are commonly used in sheet-fed printing or for inspecting discrete components such as cartons, brochures, or barcodes. They provide high flexibility in image acquisition and are well-suited for applications where the inspection can occur during a pause or stop in the printing process.
3. Multispectral Imaging
Multispectral imaging uses specific bands of light—including visible, ultraviolet (UV), and near-infrared (NIR)—to detect variations that human eyes and conventional cameras might miss. It enhances defect detection in security printing, pharmaceutical packaging, and food labeling by revealing differences in ink chemistry, substrate materials, and even contamination.
4. Hyperspectral Imaging
Hyperspectral imaging goes beyond multispectral by collecting hundreds of narrow spectral bands per pixel. This provides a rich dataset that can be used to identify precise material compositions and subtle variations in print or coating quality. It is especially valuable in high-security printing environments where authenticity, traceability, and anti-counterfeiting measures are critical.
5. Infrared (IR) Imaging
Infrared imaging captures heat patterns and wavelengths beyond the visible spectrum. In printing inspection, IR imaging is used to detect drying defects, verify thermal treatments, or identify invisible ink layers. This technology is commonly used in conjunction with thermal curing processes and specialized ink formulations.
6. Ultraviolet (UV) Imaging
UV imaging enables inspection of UV-reactive inks and coatings. This is crucial in security printing applications such as passports, banknotes, or product authentication labels. Under UV illumination, hidden features can be validated, ensuring that counterfeit elements are easily detected.
7. 3D Imaging and Structured Light
3D imaging systems use structured light or laser triangulation to capture the surface topology of printed materials. These systems measure variations in height and texture, making them ideal for embossed prints, tactile Braille, or raised security features. They provide an added layer of verification for print elements that go beyond visual characteristics.
8. High Dynamic Range (HDR) Imaging
HDR imaging addresses challenges in capturing prints with high contrast or reflective surfaces. By combining multiple exposures, HDR cameras can balance bright and dark regions within a single image. This ensures accurate inspection of glossy packages, metallic labels, or designs with complex visual tones.
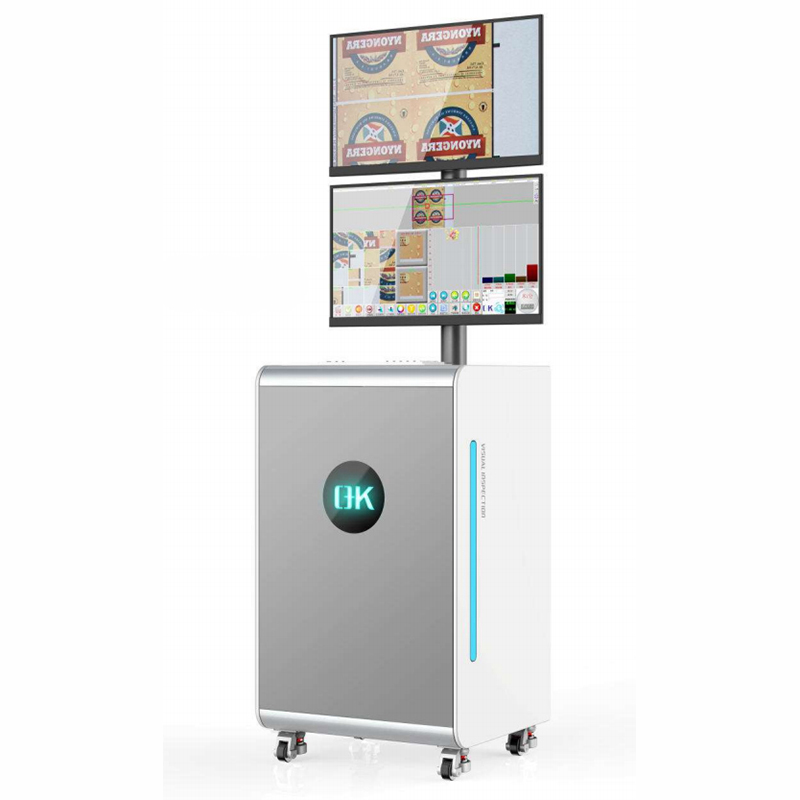
Common Sensor Types in Printing Inspection Systems
In advanced 100% printing inspection systems, sensors play a pivotal role in ensuring the accuracy, consistency, and quality of printed materials. These sensors work in conjunction with imaging technologies to detect defects, monitor print alignment, and validate the presence and position of visual elements in real time.
1. Optical Sensors
Optical sensors are fundamental components in printing inspection, used to detect light intensity, color, and contrast. They serve various purposes such as mark detection, label positioning, and edge tracking. These sensors often use infrared or visible light to differentiate between printed and non-printed areas, making them essential for applications like registration mark alignment and print presence verification.
2. Color Sensors
Color sensors analyze the color composition of the printed output by separating red, green, and blue channels or using spectral methods. These sensors ensure that printed colors remain within specified tolerances, crucial for brand consistency in packaging, label printing, and high-end marketing materials. They are typically used for inline color monitoring and ink density control.
3. Contrast Sensors
Contrast sensors are used to detect differences in brightness or reflectivity between surfaces. In printing applications, they are typically used to identify print marks, detect the leading and trailing edges of printed objects, or trigger camera systems at precise intervals. Their fast response time and accuracy make them indispensable for timing-critical operations.
4. Proximity Sensors
These sensors detect the presence or absence of an object without physical contact. In printing inspection, proximity sensors are used to confirm that sheets or labels are correctly fed through the system. They help reduce mechanical wear and increase system reliability by enabling non-contact detection of moving parts or substrates.
5. Ultrasonic Sensors
Ultrasonic sensors measure distance using high-frequency sound waves and are especially effective in detecting transparent or glossy materials that optical sensors may struggle with. In the printing industry, they are commonly used for web edge detection and to verify material presence in challenging visual conditions.
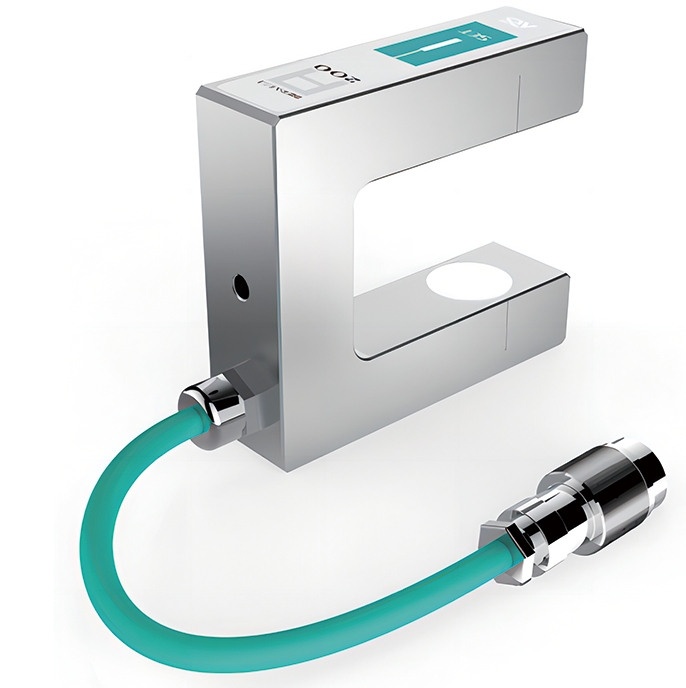
6. Laser Displacement Sensors
These high-precision sensors are used to measure the distance from the sensor to the object surface, detecting variations in thickness, warping, or raised printing. Laser displacement sensors are critical in 3D inspection applications where topographic details like embossing, Braille, or textured coatings need to be validated.
7. Encoders
Rotary and linear encoders measure the position and speed of moving parts, such as print rollers or conveyors. Encoders provide real-time feedback for synchronizing imaging and inspection processes, ensuring that images are captured at the correct intervals relative to material movement.
8. Bar Code and 2D Code Readers
These specialized sensors decode 1D and 2D barcodes printed on packaging or labels. They are integrated into inspection systems to validate that the correct code is present, readable, and matches the expected data. This function is vital for traceability, serialization, and anti-counterfeiting efforts.
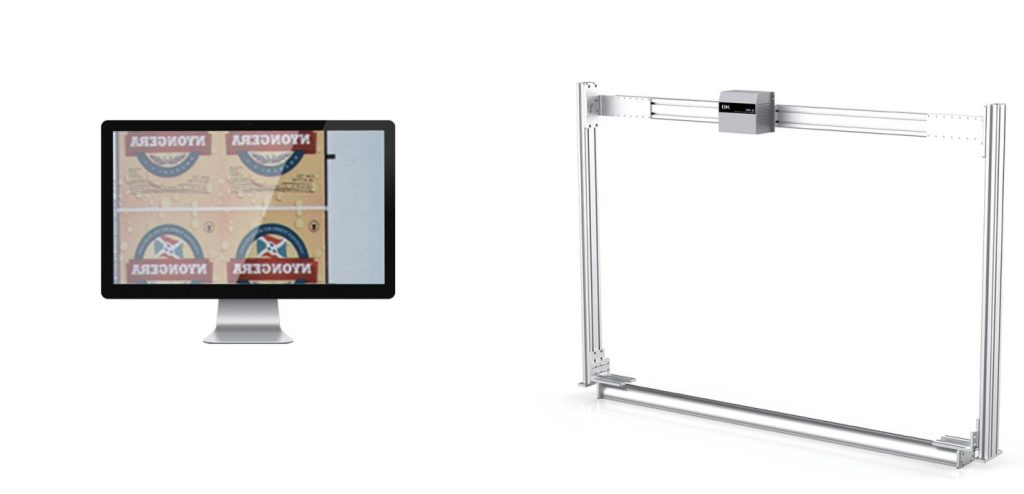
Integration of AI, Machine Learning, and Vision Systems in Printing Inspection Systems
As the printing industry continues to evolve, the demand for smarter, faster, and more accurate inspection has led to the integration of artificial intelligence (AI), machine learning (ML), and advanced vision systems into printing inspection systems. This convergence enables a new era of automated quality assurance, where systems not only detect defects but also learn from data to continuously improve performance.
1. Enhanced Defect Detection Through AI
Traditional vision systems rely on rule-based algorithms that can struggle with complex or subtle print defects. By integrating AI, particularly deep learning techniques, print inspection systems can now identify a broader range of anomalies, including smudges, ink splatter, missing characters, or improper color tones—that were previously difficult to detect using fixed thresholds. AI-driven models are trained on large datasets of known defects and can generalize to new variations with remarkable accuracy.
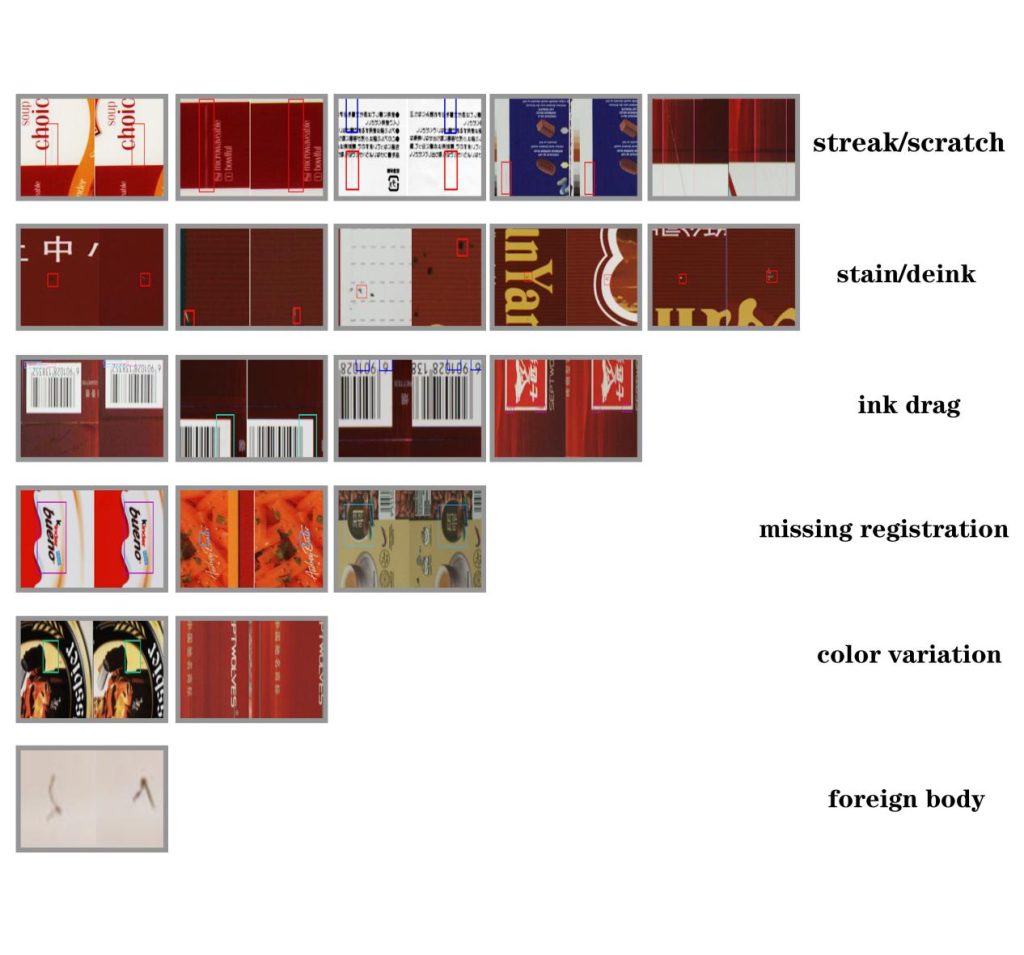
2. Adaptive Inspection with Machine Learning
Machine learning allows inspection systems to evolve over time. Instead of rigid programming, ML algorithms learn from new data collected during production. For example, in variable data printing (VDP), such as personalized packaging or labels, ML models can analyze and verify dynamic content in real time. They also reduce false positives by distinguishing acceptable process variations from true quality issues, leading to fewer unnecessary rejections and greater production efficiency.
3. Real-Time Decision Making
The integration of AI and ML with vision systems allows real-time decision-making based on live image data. When a defect is detected, the system can trigger automatic actions such as stopping the press, marking defective products, or adjusting the printing parameters. This proactive approach minimizes downtime and waste while maintaining consistent output quality.
4. Deep Learning for OCR and Pattern Recognition
Optical Character Recognition (OCR) is a critical component of many inspection systems, especially in pharmaceuticals and food packaging. Deep learning enhances OCR capabilities by recognizing diverse fonts, distorted characters, and even poorly printed or partially missing text. AI also improves pattern recognition for barcodes, logos, and graphic elements—ensuring compliance and brand consistency.
5. Intelligent Classification and Root Cause Analysis
AI-enabled vision systems can classify defects by type, severity, and location, giving manufacturers deeper insights into production trends. Over time, this data can be analyzed to pinpoint root causes of recurring issues, such as printhead misalignment or substrate inconsistencies. These insights facilitate preventive maintenance and continuous process optimization.
6. Seamless Integration into Existing Systems
Modern web inspection vision systems for printing quality are designed for modular integration into existing printing lines. They support common industrial protocols and can be adapted to work with legacy hardware, making it easier for manufacturers to adopt intelligent inspection technologies without overhauling their entire infrastructure.
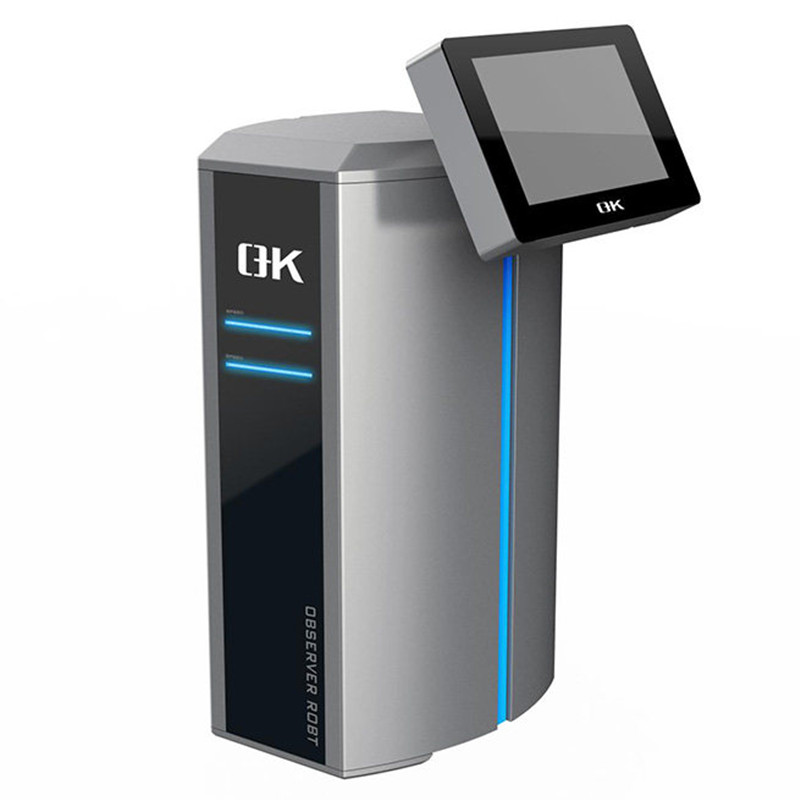
Key Applications of Printing Inspection Systems in the Print Industry
This chart provides a clear overview of how printing inspection systems are applied across various aspects of print production, helping businesses maintain quality standards and optimize operations.
Application | Description | Benefits |
Defect Detection | Identifying print defects such as smudges, misprints, color inconsistencies, and alignment errors. | Ensures high-quality output, reduces product wastage. |
Registration Mark Verification | Verifying proper alignment of registration marks to ensure accurate print positioning. | Prevents misalignment errors and improves precision. |
Color Consistency Monitoring | Ensuring color accuracy across prints using color sensors and imaging. | Maintains brand consistency, ensures visual appeal. |
Barcode/QR Code Verification | Verifying the readability and accuracy of barcodes, QR codes, or other machine-readable marks. | Improves traceability and data integrity. |
Substrate Inspection | Inspecting the quality of substrates (e.g., paper, film) for defects such as creases or tears. | Prevents material wastage and ensures print quality. |
3D Surface Inspection | Analyzing embossed or textured prints to ensure uniformity and quality. | Validates complex print structures and textures. |
Packaging Validation | Inspecting packaging prints, such as labels, for completeness and accuracy. | Guarantees that packaging meets regulatory standards. |
Inline Print Quality Control | Continuous monitoring of print quality during the production process. | Reduces the need for manual inspection, speeds up production. |
Security Printing | Verifying security features on documents such as anti-counterfeit marks, microtext, or holograms. | Ensures authenticity and prevents fraud. |
Final Product Inspection | Inspecting final printed products for overall quality, including packaging, labels, and printed materials. | Ensures the finished product meets customer expectations. |
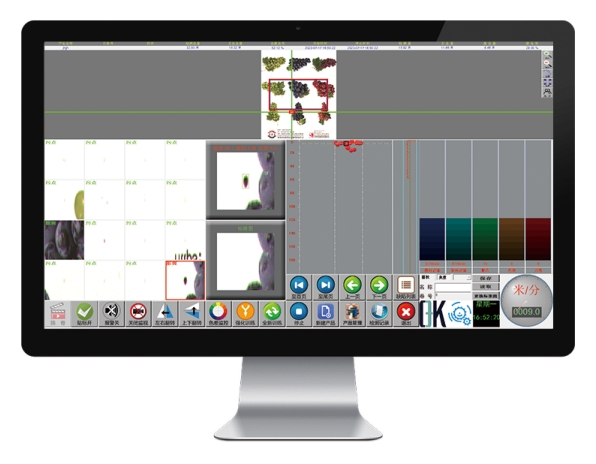
Future Trends in Imaging and Sensor Technologies for Printing Inspection Systems
1. Integration of 3D Vision and Surface Profiling
While 2D imaging remains the foundation for many printing inspection systems, the future will see a more significant shift toward 3D imaging technologies. 3D vision systems, including structured light sensors and laser triangulation devices, will be increasingly used to inspect the surface topography of printed materials. These systems can measure embossing, textured surfaces, and even raised ink layers, ensuring consistency and quality in materials like luxury packaging, labels, or security documents.
The integration of 3D imaging will also be vital for detecting defects in substrates that are prone to deformation, such as flexible packaging materials. This level of precision will enable faster and more accurate measurements, especially in situations where traditional 2D sensors may fall short.
2. Edge AI and Edge Computing for Faster Decision-Making
In the future, there will be a greater emphasis on processing data at the source, near the inspection point, through edge computing. By placing AI and sensor processing capabilities directly within the printing equipment, real-time decision-making can be achieved without relying on centralized cloud computing. This reduces latency and ensures faster responses, such as automatic corrections during the printing process, thereby preventing errors before they accumulate.
Edge AI will allow for the integration of more sophisticated algorithms capable of adaptive learning, meaning the inspection system will be able to dynamically adjust its focus based on the type of print job, material, and substrate being used.
3. Miniaturization of Sensors and Integration with IoT
The future of sensor technology will likely see further miniaturization, with smaller, more compact sensors being integrated into the printing system itself. These sensors will be able to detect defects in real-time, and their small size will allow for integration into tight spaces or on individual printing elements, such as print heads or rollers.
Additionally, sensors in printing inspection systems will be increasingly connected through the Internet of Things (IoT). This will enable smarter data exchange between various devices on the production line, including printers, inspection systems, and other automated equipment. IoT-enabled sensors can provide continuous feedback on print quality and equipment health, helping to prevent costly downtimes and improve overall operational efficiency.
4. Real-Time Predictive Maintenance and Performance Monitoring
As sensor technologies evolve, the integration of predictive maintenance capabilities into printing inspection systems will become more widespread. Sensors will continuously monitor key equipment components—such as print heads, rollers, and conveyors—and predict when they are likely to require maintenance, based on wear patterns and environmental conditions.
Predictive maintenance will help manufacturers avoid unexpected failures by addressing issues before they lead to costly downtime. Coupled with AI, sensors will analyze historical and real-time data to determine patterns and optimize equipment longevity and performance.
5. Cloud-Based Inspection Systems for Enhanced Scalability
Cloud computing will play a significant role in the future of printing inspection systems by enabling centralized data storage, sharing, and analysis. Cloud-based systems will allow manufacturers to store vast amounts of inspection data, which can then be used to optimize printing processes, track quality trends, and even compare performance across different locations or print jobs.
This cloud integration will enable manufacturers to scale their inspection capabilities more easily, offering insights that can lead to better quality control and process optimization across multiple production lines.
6. Integration of Robotics for Physical Inspection
As the demand for highly automated production grows, robots will play a more active role in physical inspection tasks. These robots, equipped with advanced sensors and imaging technology, will handle more intricate and delicate inspection processes. From analyzing small components to performing final checks on finished products, robots will ensure that products are free of defects before they are packaged or shipped.
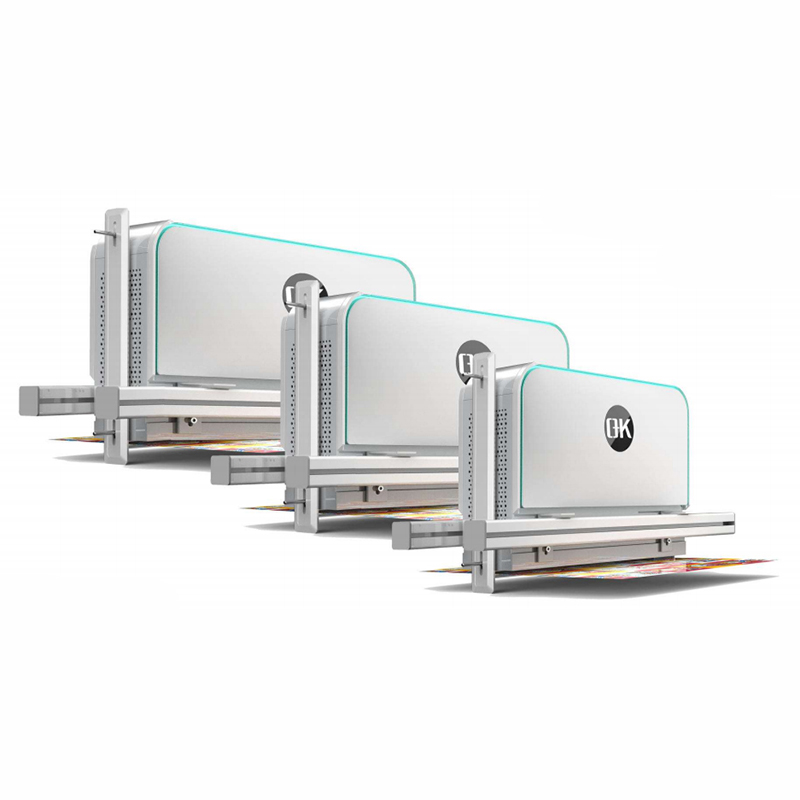
Summary
Imaging and sensor technologies are critical for printing inspection systems, enabling consistent, high-quality output across diverse printing applications. As printing becomes more complex and customer demands more stringent, the integration of advanced sensor and AI technologies will be crucial for quality assurance, operational efficiency and competitive differentiation.