Custom In-line Measurement Solutions for Specific Applications
Table of Contents
The need for real-time, accurate data is essential for maintaining quality control, optimizing processes, and ensuring safety. Custom in-line measurement solutions offer tailored systems that integrate directly into production lines to provide immediate feedback on critical parameters, enabling businesses to monitor and control their operations in real-time. These custom solutions for in-line measurement system are designed to meet the specific needs of different industries, ensuring accurate measurements that align with the unique requirements of each application.
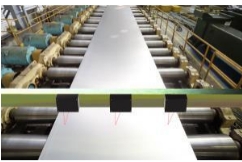
Why Custom In-line Measurement Solutions Matter
Standard measurement systems may not always meet the precise needs of specialized applications. Whether it’s the chemical industry, food processing, pharmaceuticals, or automotive manufacturing, off-the-shelf measurement tools can sometimes fall short when unique conditions and parameters are in play.
Custom in-line measurement solutions are engineered to accommodate the specific variables of an application, such as temperature ranges, material composition, and environmental factors. These in-line measurement systems offer enhanced accuracy, seamless integration into existing workflows, and scalability to accommodate future process changes.
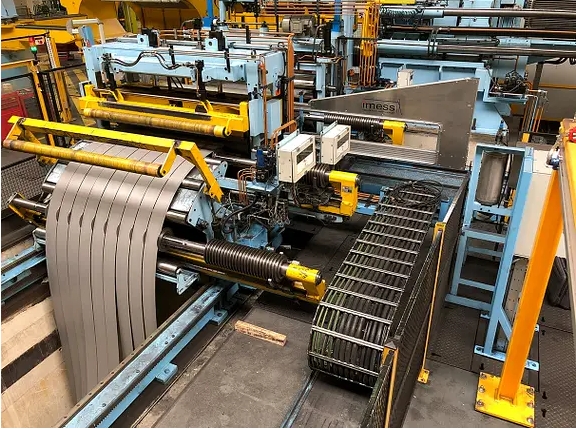
Benefits of Custom In-line Measurement Solutions
This chart highlights how custom in-line measurement solutions can deliver significant improvements in production performance, cost efficiency, and quality assurance across various industries.
Benefit | Description |
Real-time Monitoring | Provides continuous data feedback, enabling immediate adjustments and process optimization. |
Increased Accuracy | Custom solutions are designed for specific applications, ensuring precise measurements of critical parameters. |
Improved Product Quality | Ensures consistent quality by monitoring key variables during production, reducing defects and variability. |
Enhanced Efficiency | Minimizes downtime and errors through automated monitoring, optimizing production flow. |
Regulatory Compliance | Ensures adherence to industry standards (FDA, ISO, HACCP) by providing accurate data for audits and inspections. |
Cost Savings | Reduces waste, rework, and resource consumption by maintaining optimal process conditions. |
Seamless Integration | Easily integrates with existing systems, minimizing disruption during implementation. |
Scalability | Can be adapted and expanded as production requirements change, ensuring long-term flexibility. |
Reduced Manual Intervention | Automates data collection and reporting, minimizing the need for manual measurement and human error. |
Predictive Maintenance | Facilitates early detection of potential equipment issues, reducing unexpected downtime. |
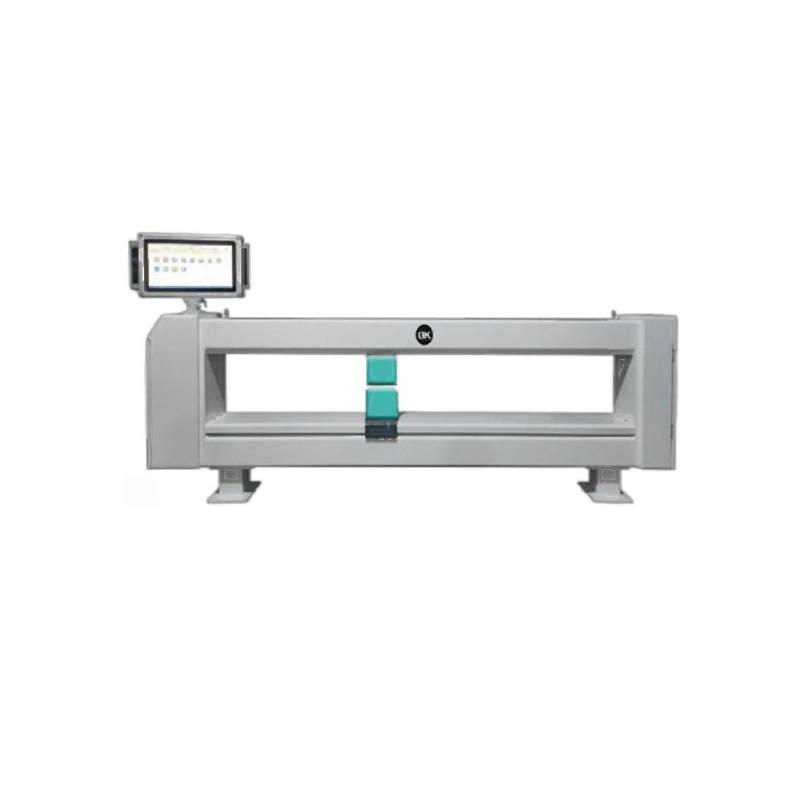
Key Features of Custom In-line Measurement Systems
- Tailored Sensor Design: Custom in-line systems utilize sensors specifically designed or selected based on the unique variables of the application, such as temperature, pressure, material composition, and chemical exposure. This ensures that the system performs accurately in the conditions specific to the process.
- Real-time Data Acquisition: These solutions provide continuous monitoring of critical parameters, transmitting real-time data to control systems. This enables operators to make immediate adjustments and optimize the production process without delays.
- Seamless Integration: Custom in-line measurement systems are designed to integrate effortlessly with existing equipment and workflows. This reduces downtime and ensures a smooth transition without significant disruptions to production.
- Industry-Specific Calibration: Calibration is tailored to the industry’s specific requirements or client needs, ensuring that the system delivers reliable and precise measurements in accordance with regulatory and quality standards.
- Automation Compatibility: Many production environments are automated, and custom in-line measurement systems are designed to work alongside these automated processes. The system’s data feeds directly into automation systems for real-time process adjustments, reducing the need for manual oversight.
- Customizable Software and Reporting: Custom systems often include software tailored to the user’s needs, enabling configurable reporting formats, real-time alerts, and integration with other enterprise systems for centralized monitoring.
- Enhanced Durability and Reliability: The components of these systems are built to withstand the specific environmental conditions of the application, whether that involves high temperatures, corrosive substances, or other challenging environments.
- Modularity and Scalability: Custom in-line measurement solutions can be designed with modular components, allowing for future upgrades or adjustments as production needs evolve. They are scalable to accommodate growing or changing production lines.
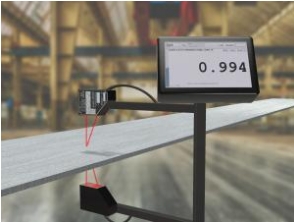
Applications Across Various Industries of Custom In-line Measurement Solutions
This chart provides a quick overview of how custom in-line measurement systems are applied in different industries to monitor key parameters and improve process efficiency.
Industry | Applications | Key Parameters Measured |
Pharmaceutical | Tablet manufacturing, liquid mixing, coating, packaging | Ingredient composition, temperature, pressure, viscosity, drug formulation consistency |
Food and Beverage | Pasteurization, fermentation, filling, packaging | Moisture content, pH levels, viscosity, temperature, weight, ingredient concentration |
Automotive | Assembly line production, part manufacturing, fluid systems | Torque, material composition, fluid levels, pressure, dimensional accuracy |
Chemical and Petrochemical | Refining, blending, distillation, chemical reaction monitoring | Temperature, pH levels, flow rates, chemical composition, pressure |
Textile | Dyeing, fabric thickness control, tension monitoring | Fabric thickness, tension, dye consistency, moisture levels |
Energy and Utilities | Power plant operation, pipeline monitoring, fluid control | Flow rates, temperature, pressure, fluid composition, energy consumption |
Plastics and Packaging | Plastic extrusion, polymer molding, film manufacturing, container quality control | Extrusion thickness, melt temperature, polymer flow, material thickness, seal integrity |
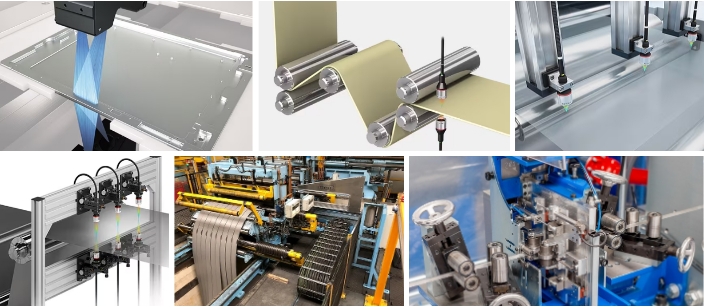
How to Select the Right Provider for Custom In-line Measurement Solutions
Choosing the right provider for custom in-line measurement solutions is critical to ensuring that your system meets the specific needs of your application. The right partner will not only deliver a tailored solution but also offer ongoing support and innovation to keep your processes optimized.
- Industry Expertise: The provider should have extensive experience in your specific industry. Each industry has unique requirements, whether it’s regulatory compliance in pharmaceuticals, precise control in food processing, or robust materials in petrochemical applications. A provider with a proven track record in your sector will understand these challenges and design a solution that addresses them.
- Customization Capabilities: Customization is key in in-line measurement solutions. The provider should be capable of designing systems that are tailored to your specific process variables, such as temperature, pressure, flow rate, or material composition. They should offer flexibility in sensor design, data integration, and reporting to meet your exact needs.
- Technological Expertise: The provider should offer cutting-edge technologies for in-line measurement systems in sensor development, data acquisition and automation integration. Look for providers who are leveraging advancements such as IoT, machine learning, and real-time data analytics to offer enhanced process control and predictive maintenance capabilities.
- Integration Support: The solution should seamlessly integrate with your existing production line, machinery, and software systems. A good provider will assess your current setup and ensure that the new system is compatible with minimal disruption. Look for companies that offer integration with enterprise resource planning (ERP), manufacturing execution systems (MES), and other control systems.
- Ongoing Support and Maintenance: Measurement systems require regular maintenance, calibration, and updates to ensure long-term performance and accuracy. The provider should offer ongoing support, including regular system check-ups, calibration services, and software updates to keep your system functioning optimally.
- Cost-Effectiveness: While custom in-line measurement solutions can require an upfront investment, the long-term benefits in terms of increased accuracy, efficiency, and reduced downtime can lead to significant cost savings. The right provider will offer solutions that provide a solid return on investment (ROI), minimizing production errors and improving overall process control.
- Client References and Reputation: A strong provider will have a solid reputation in the industry. Ask for client references or case studies where they have successfully implemented custom solutions. This will give you insight into their reliability, expertise, and the quality of their solutions.
- Innovation and Future-readiness: The industry is always evolving, and so should your measurement solutions. Look for a provider that is continuously innovating and staying ahead of industry trends. This ensures that your system will not become obsolete and that you’ll have access to the latest technologies in measurement and process optimization.
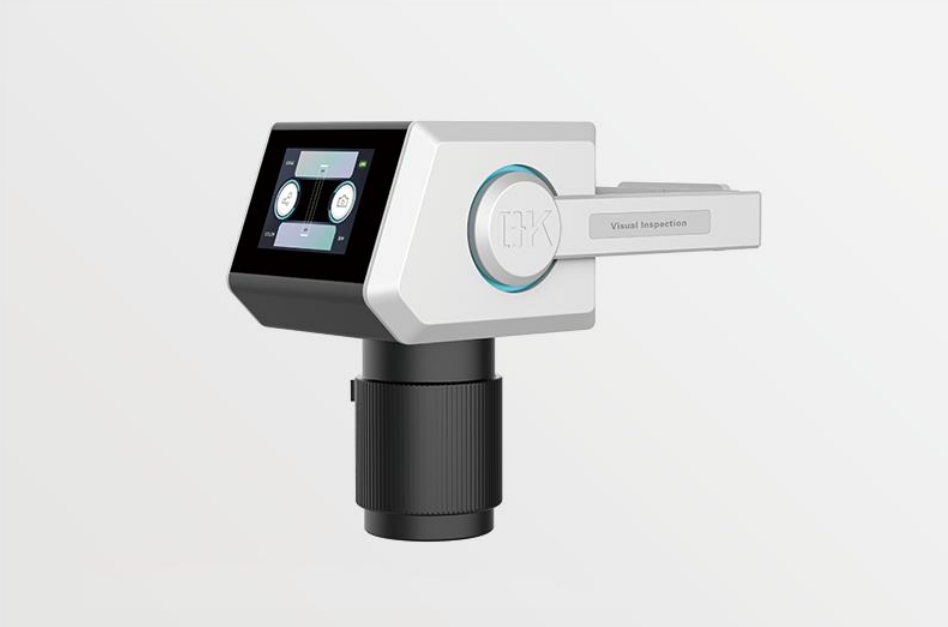
A trusted provider of Custom In-line Measurement Solutions – Arise
Arise is a leading provider of custom in-line measurement solutions, such as width measurement system, thickness measurement system. It is specializing in tailored systems that deliver precise, real-time data for various industries. With expertise in sensor design, seamless integration and industry-specific calibration, Arise ensures optimal performance and accuracy. Their solutions are designed to meet the unique needs of each application, offering enhanced process control and compliance with regulatory standards.
Overall, custom in-line measurement solutions offer significant advantages for businesses that require precision and adaptability in their production processes. These systems provide real-time data, enhancing product quality, improving efficiency, and ensure regulatory compliance. By selecting the right provider and investing in the right technology, businesses across various industries can that will not only meet your current needs but also grow with your future requirements.