How Advanced Sensors are Used for Improving Tension Control Accuracy
In industries where web material handling is critical, tension control is a fundamental aspect of maintaining the correct tension, ensuring that materials move smoothly through machines without stretching, wrinkling, tearing, or becoming misaligned. As industries continue to demand higher quality and efficiency, advanced sensors have emerged as a key technology for significantly improving the accuracy of tension control systems.
Table of Contents
The Importance of Accurate Tension Control
- Ensuring Consistent Product Quality
The most immediate and noticeable benefit of accurate tension control is its impact on product quality. In industries like printing, textiles, and packaging, even slight variations in material tension can lead to defects like wrinkles, misalignment, or inconsistent coatings. Inaccurate tension can cause web breakages, leading to downtime and defective output. By maintaining precise tension, manufacturers can ensure that materials are consistently processed without defects, resulting in higher-quality finished products that meet stringent industry standards.
- Enhancing Operational Efficiency
Precise tension control is not only about the product—it also plays a vital role in optimizing the manufacturing process itself. When tension is consistently controlled, the machinery operates more smoothly, reducing strain on motors, rollers, and other mechanical components. This leads to fewer mechanical failures and less frequent maintenance. Furthermore, by preventing issues like material wastage and downtime caused by tension inconsistencies, manufacturers can maintain a steady production flow, increasing overall throughput and efficiency.
- Reducing Material Waste and Cost
In industries where materials are costly or in short supply—such as flexible electronics or specialty films—accurate tension control becomes even more critical. When tension is off, materials can stretch, tear, or become misaligned, leading to substantial waste. With precise tension control, the material is used optimally, reducing scrap and waste. This has a direct impact on lowering production costs and improving the bottom line for manufacturers.
- Protecting Equipment and Extending Its Lifespan
In any manufacturing system, equipment longevity is vital to controlling maintenance costs. Inaccurate tension can place undue stress on machinery components such as motors, rollers, and brakes. Over time, this strain accelerates wear and tear, leading to more frequent breakdowns and costly repairs. Accurate tension control systems help prevent this, ensuring the smooth operation of machinery and extending its lifespan. By reducing mechanical stress, manufacturers can improve the overall reliability of their production lines.
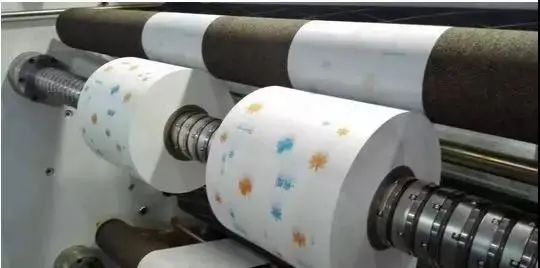
- Meeting Safety and Regulatory Standards
In certain industries, especially in sectors like pharmaceuticals, food packaging, and electronics, maintaining precise tension control is not just an operational issue but a regulatory one. Failure to ensure accurate tension can lead to non-compliance with safety standards, which might result in costly penalties or recalls. By integrating advanced tension control systems, manufacturers can meet these safety requirements and ensure compliance with relevant regulations, protecting both their products and their brand reputation.
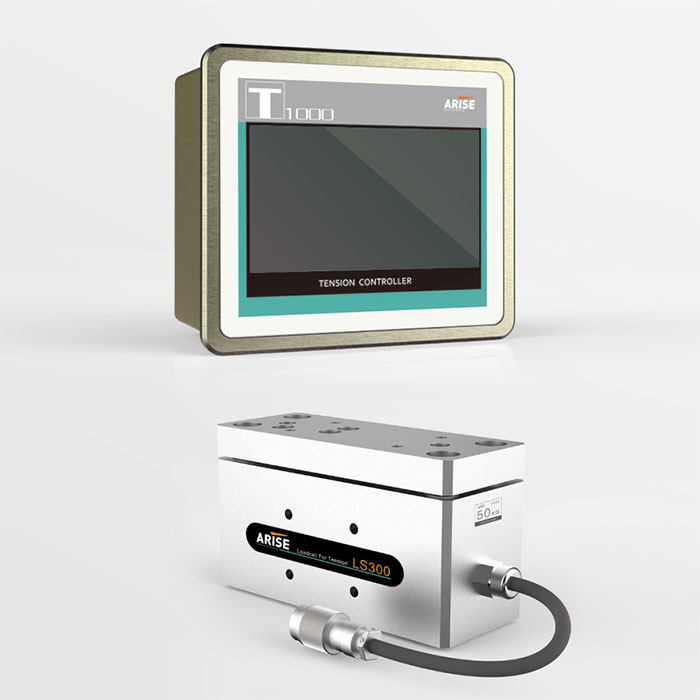
Types of Advanced Sensors Used for Accurate Tension Control
1. Load Cells
Load cells are among the most essential components in modern tension control systems. They measure the force exerted by the material being processed, typically through highly sensitive strain gauge elements. These tension sensors provide direct, real-time feedback, allowing the control system to detect even minute variations in tension. Advanced load cells are built to offer high linearity, thermal stability, and resistance to industrial noise, making them ideal for applications requiring continuous and highly accurate monitoring.
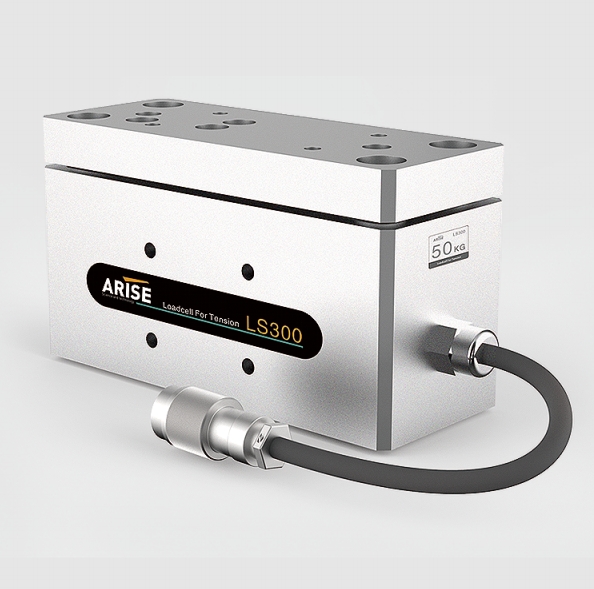
2. Optical Sensors
Optical sensors play a crucial role in non-contact tension measurement, especially in processes where delicate or ultra-thin materials are involved. Using technologies like laser triangulation or infrared detection, optical sensors monitor web alignment, position, and speed. By analyzing slight changes in material behavior, these sensors indirectly help maintain consistent tension without physically interacting with the product. Their precision and non-invasive nature make them invaluable in high-speed, high-sensitivity production lines.
3. Ultrasonic Sensors
Ultrasonic sensors offer another non-contact solution, particularly effective in monitoring wide or flexible webs. By emitting high-frequency sound waves and measuring the time it takes for the echo to return, ultrasonic sensors can detect material sag and web positioning. Changes in these parameters provide indirect measurements of tension variations, allowing systems to adjust braking or drive forces dynamically. Ultrasonic technology is especially robust in environments where dust, moisture, or contamination could interfere with optical systems.
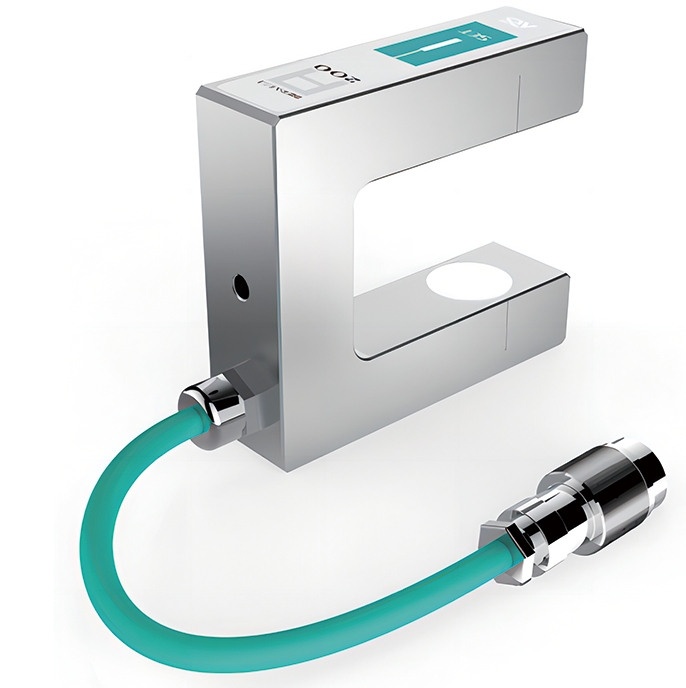
4. Eddy Current Sensors
Eddy current sensors are widely used for displacement measurement in metallic components, providing an indirect but highly responsive method of tension monitoring. By detecting changes in electromagnetic fields caused by metallic movement, these sensors can identify small shifts in rollers or moving parts that correlate to tension fluctuations. Their high-speed response and durability under dynamic conditions make them particularly suitable for applications involving rapid changes in load or material speed.
5. Capacitive Sensors
Capacitive sensors excel in environments where small positional or thickness changes must be measured with extreme precision. These sensors work by detecting changes in capacitance as the material moves or shifts, allowing very sensitive detection of tension-related variations. They are especially effective when working with extremely thin films or flexible electronics, where other types of sensors might struggle to achieve the necessary sensitivity or reliability.
How Advanced Sensors Drive Improvements in Tension Control Accuracy
1. Real-Time Feedback
One of the most critical contributions of advanced tension sensors is the ability to deliver real-time data. Load cells, for instance, measure the direct force applied to moving materials. This immediate feedback allows control systems to instantly detect and correct deviations from target tension levels. Unlike traditional tension control methods that relied on inferred data from motor torque or roller speed, advanced sensors provide direct, high-fidelity measurements, greatly enhancing system responsiveness and reliability.
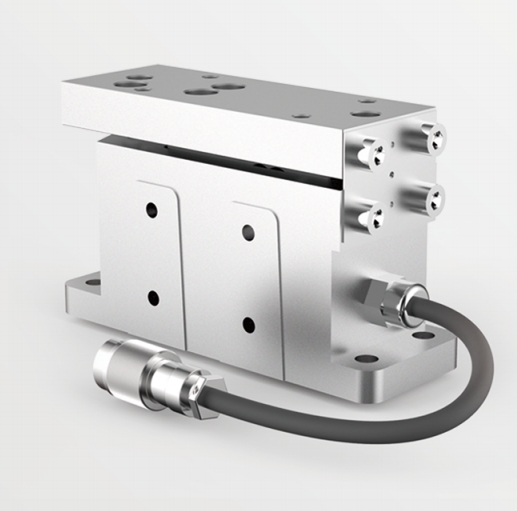
2. Non-Contact Sensing Technologies
For sensitive or delicate materials, non-contact sensors such as optical and ultrasonic devices play a pivotal role. Optical sensors utilize laser or infrared technologies to track material position, edge alignment, and speed. By analyzing these parameters, the system can infer tension variations without physically touching the material, avoiding potential damage. Ultrasonic sensors offer a similar advantage, using sound waves to detect sagging or displacement in webs and fabrics. These technologies ensure that tension adjustments are made with high precision, even for ultra-thin or fragile materials.
3. Adapting to Dynamic Process Changes
Production environments are rarely static. Material properties can change, machine speeds can fluctuate, and external factors like temperature or humidity can affect tension dynamics. Advanced sensors such as eddy current and capacitive sensors provide the agility needed to adapt to these dynamic changes. Eddy current sensors monitor the position of metallic components with extremely fast response times, while capacitive sensors detect fine variations in material thickness or displacement. Their sensitivity ensures that tension control systems can adjust to evolving conditions in real-time, maintaining stable operations without manual intervention.
4. Integration and Multi-Sensor Systems
Many modern tension control systems integrate multiple sensor types to enhance accuracy and resilience. For example, a system might use load cells for direct tension measurement while simultaneously employing optical sensors to monitor web alignment. By cross-referencing multiple data points, control algorithms can more accurately diagnose issues and maintain tighter tension tolerances. This layered approach also builds redundancy into the system, reducing the risk of faults or shutdowns due to a single sensor failure.
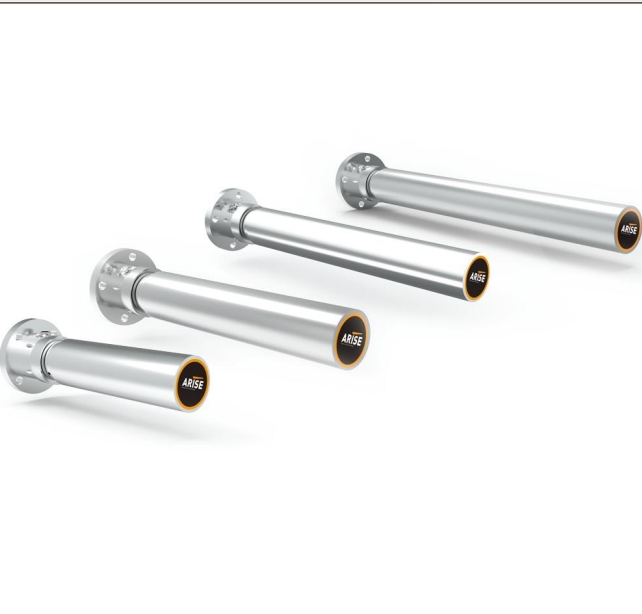
Future Trends in Tension Sensors for Improving Tension Control Accuracy
Trend | Description |
Smart Sensor Integration | Sensors embedded with processors and AI for self-calibration and adaptive control. |
Wireless and IoT Connectivity | Wireless tension sensors enabling remote monitoring, diagnostics, and predictive maintenance. |
Higher Sensitivity and Resolution | Development of sensors capable of detecting even micro-variations in tension for ultra-precise control. |
Miniaturization | Smaller, lighter sensors to fit compact or high-speed machinery without affecting material flow. |
Energy-Efficient Sensor Designs | Sensors optimized for lower power consumption, important for IoT and mobile systems. |
Advanced Non-Contact Sensing | Broader adoption of optical, laser, and ultrasonic non-contact technologies for delicate materials. |
Data Analytics and Predictive Tension Control | Integration of sensor data into big-data platforms for predicting and preventing tension-related defects. |
Self-Healing Materials and Sensors | Use of materials that can self-repair minor damages, increasing sensor lifespan and reliability. |
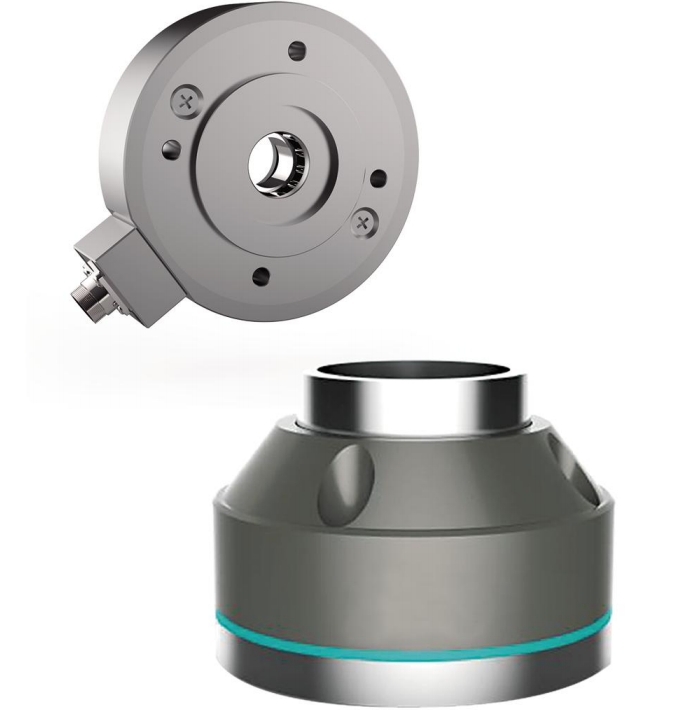
Final Thoughts
Advanced tension sensors have greatly improved the accuracy of tension control, moving industries toward smarter, faster, and more reliable production systems. Their ability to deliver high-precision, real-time feedback has made it possible to maintain optimal tension under a wide range of conditions, ensuring better product quality, lower material waste and improved overall productivity. Manufacturers looking to maintain a competitive edge should seriously consider investing in advanced sensor-based tension control systems for achieving higher precision and operational intelligence in the manufacturing process.