How to Optimize Tension Control in Label and Packaging Printing
In the highly competitive label and packaging printing industry, maintaining consistent print quality and minimizing waste are top priorities. One critical factor influencing the quality and waste in label and packaging printing is web tension control. Optimizing tension control is not only essential for print accuracy but also crucial for process stability, material integrity and equipment longevity.
Table of Contents
Understanding Tension Control
Tension control refers to the regulation of the longitudinal pulling force applied to the web as it moves through various processing stations. This control must be accurate and stable, regardless of changes in roll diameter, machine speed, or substrate type. Whether printing on paper, film, foil, or composite materials, maintaining steady web tension prevents issues such as stretching, wrinkling, misregistration, and breaks.
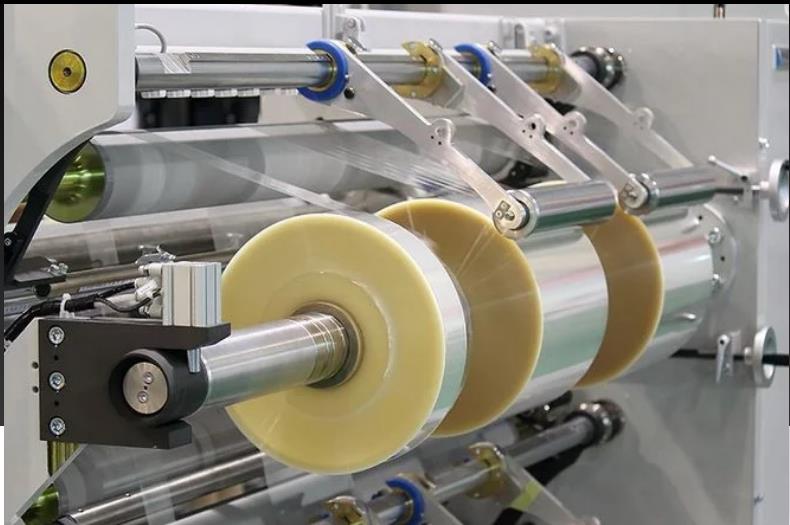
Why Tension Control Matters in Label and Packaging Printing
In label and packaging applications, where high precision and aesthetic appeal are essential, improper tension can compromise the entire production. If tension is too high, substrates may elongate, affecting the alignment of colors or die-cut patterns. If tension is too low, the material might wander off-track, causing uneven printing or jams. This is particularly problematic in multi-process setups that include lamination, slitting, or embossing, as variations in tension affect each step differently.
The importance of maintaining proper tension is amplified in high-speed operations. Modern presses are designed to run faster and more efficiently, but with increased speed comes a reduced margin for error. Even minor fluctuations in web tension at high speeds can quickly lead to misprints, material waste, and downtime.
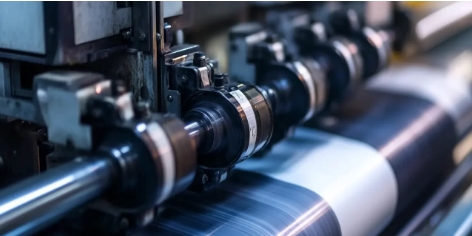
Common Challenges in Tension Control for Label and Packaging Printing
Challenge | Possible Causes | Recommended Solutions |
Misregistration | Fluctuating web tension; inconsistent line speed | Implement closed-loop tension control; synchronize drive systems |
Web Wrinkling | Uneven tension across web; roller misalignment | Inspect and align rollers; use spreader or bowed rollers |
Material Stretching or Curling | Over-tensioning; elastic substrate sensitivity | Adjust tension based on material type; use low-inertia rollers |
Poor Die-Cutting Accuracy | Tension fluctuations at cutting stage | Isolate tension zones; use dedicated sensors in die-cutting section |
Telescoping Rolls | Improper winding tension; over-speeding rewind section | Apply taper tension; monitor roll hardness during winding |
Edge Damage or Tearing | Excessive tension; misaligned web edges | Lower web tension; use edge guidance systems |
Ink Smudging or Misalignment | Web Slack or excessive speed variations during print | Maintain steady tension; optimize tension during print transfer |
Roll Slack or Bagging | Insufficient tension at rewind; poor tension taper control | Increase rewind tension; calibrate taper tension settings |
Waste from Setup Errors | Manual tension adjustments, lack of automation | Use preset tension profiles; automate job changeovers |
Machine Downtime | Tension system alarms; operator misjudgment | Train operators on tension control systems; schedule preventive maintenance |
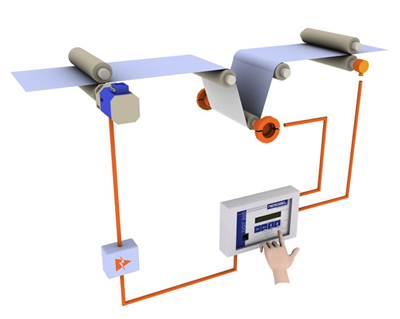
Strategies for Optimizing Tension Control in Label and Packaging Printing
Effective web tension control ensures that substrates move smoothly and consistently through the press, laminator, cutter, or slitter. To achieve optimal results, printers must implement targeted strategies that account for material properties, process complexity, and system design.
1. Understanding Material-Specific Requirements
Different substrates, such as paper, polypropylene, polyester, or laminated films, respond uniquely under tension. For example, plastic films are more susceptible to stretching, while paper may tear or wrinkle under excessive tension. A key optimization strategy is to develop tension profiles tailored to the mechanical properties of each material type. These profiles should be based on empirical testing and retained in the control system for rapid retrieval during changeovers.
2. Implement Closed-Loop Tension Control Systems
Advanced web presses benefit greatly from closed-loop tension control systems. These systems monitor tension in real time using sensors such as load cells or dancer rollers and automatically adjust torque, brake pressure, or motor speed to maintain stability. By eliminating manual intervention and responding instantly to changes in web dynamics—like roll diameter or line speed—closed-loop systems offer superior precision and consistency compared to open-loop setups.
Key Components
This chart provides a clear overview of each key component’s role in maintaining an efficient and responsive closed-loop tension control system.
Component | Description | Function in the Tension Control System |
Load Cells | Tension sensors used to measure the amount of tension applied to the web. | Continuously monitor the tension and provide real-time data for control adjustments. |
Dancer Arms | A mechanical device that moves in response to changes in web tension. | Act as a feedback sensor to detect tension variations and communicate with control systems. |
Control System (PLC or PC) | A digital platform that processes signals from sensors and sends commands to actuators. | Process real-time data to adjust motor speeds, brakes, or other components to maintain stable tension. |
Motors | Drive motors (or brakes) that control the speed of the rollers or web handling equipment. | Adjust the web’s speed and tension by varying motor speed or applying braking force. |
Brake or Clutch Mechanisms | Devices that apply or release force to control the tension on the web. | Provide corrective tension adjustments when load cells or dancer arms signal deviations. |
Tension Controllers | Specialized hardware or software algorithms that ensure tension is within the desired range. | Fine-tune and maintain constant tension through automated adjustments. |
Web Guide Systems | Sensors or mechanical systems that monitor and correct the position of the web. | Ensure the web remains centered, minimizing tension variations caused by misalignment. |
HMI (Human-Machine Interface) | A user interface that displays tension readings and allows operators to adjust system settings. | Provides operators with real-time feedback and control over tension system parameters. |
Feedback Loop | The system’s process of continually adjusting tension based on sensor input. | Creates continuous adjustments in real-time to ensure optimal tension is maintained across all zones. |
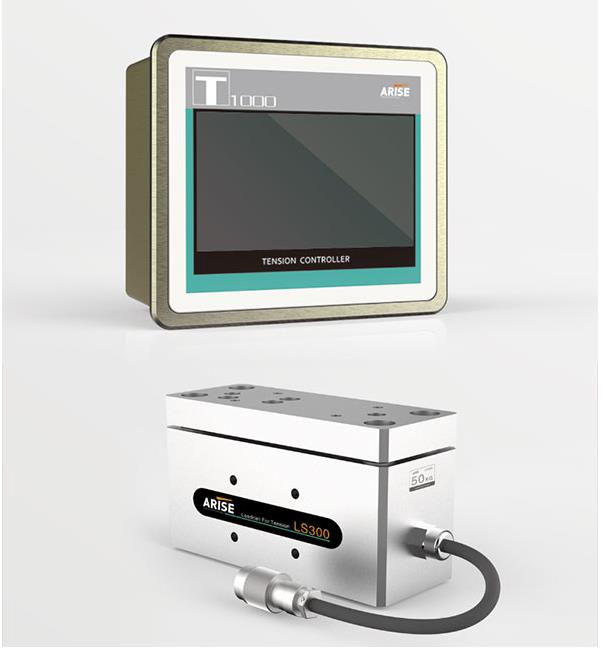
3. Segment Tension Zones
Dividing the printing and converting line into tension zones—typically unwind, printing, drying, die-cutting, and rewind—is a strategic approach to optimize control. Each zone requires specific tension settings based on its function. For example, printing zones require high precision to maintain registration, while rewind zones must be flexible to accommodate roll buildup. Isolating tension zones prevents disturbances in one area from affecting the entire web path.
4. Utilize Pre-Set and Adaptive Tension Profiles
To reduce setup time and improve reproducibility across jobs, printers can implement pre-set tension profiles based on material type and job requirements. More advanced systems may use adaptive profiles that change in real-time based on input from machine sensors and control algorithms. These profiles are especially valuable in short-run digital or hybrid printing environments where quick changeovers are frequent.
5. Prioritize Alignment and Mechanical Maintenance
Even the most sophisticated tension control systems can’t perform well without a solid mechanical foundation. Roll misalignment, bearing wear, or imbalanced rollers can introduce tension inconsistencies. Routine machine inspections and alignment checks are crucial for ensuring optimal web handling. Investing in precision-guided rollers and stable unwind/rewind units also contributes to smoother tension performance.
6. Integrate Tension Control with Registration and Vision Systems
For multi-color and high-resolution printing, maintaining perfect registration is crucial. Tension control should be tightly integrated with the press’s registration system and web inspection vision systems to detect and correct deviations in real time. This integration enhances print accuracy and reduces spoilage, particularly when working with materials prone to stretching or movement.
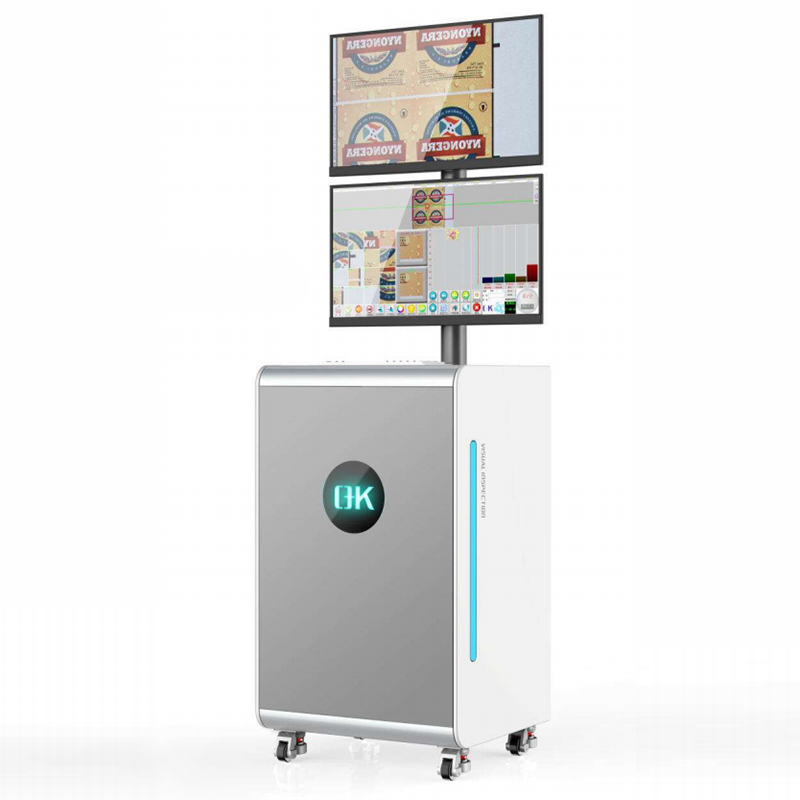
7. Train Operators and Standardize Procedures
Human error remains a common cause of tension-related issues. Comprehensive operator training and standardized procedures help ensure that tension settings are applied consistently and adjusted correctly. Easy-to-use control interfaces with visual indicators or alerts also help operators monitor and react to tension changes promptly.
8. Monitor and Analyze Performance Data
Leveraging data analytics from tension control systems enables proactive adjustments and long-term optimization. Printers can track performance trends, identify recurring problems, and make data-driven improvements. This predictive approach supports better quality control, preventive maintenance, and resource planning.
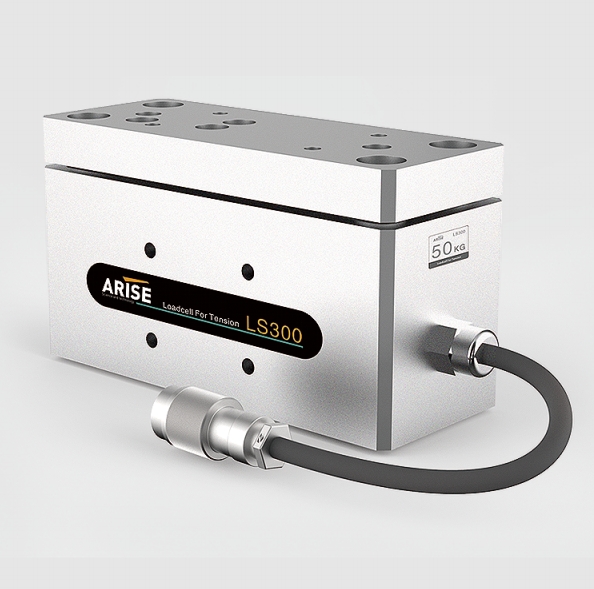
Summary
Optimizing tension control in label and packaging printing is an ongoing strategy that involves technical, mechanical and operational components. Through combining material knowledge, advanced automation, precise system integration, and well-trained personnel, printers can significantly enhance print quality, reduce waste, and maintain efficiency even in the most demanding production environments.