How to Seamlessly Integrate Quality Inspection Systems with Printing Workflows
In the fast-paced development of printing industry, maintaining high standards of quality is crucial. Any deviation can result in costly reprints, customer dissatisfaction, and damage to the brand’s reputation. The integration of quality inspection systems with printing workflows has become a necessity to ensure that each product meets the high standards. This article delves into the importance of seamless integration, the technologies involved, the benefits this integration brings to the printing industry and the challenges the integration meets .
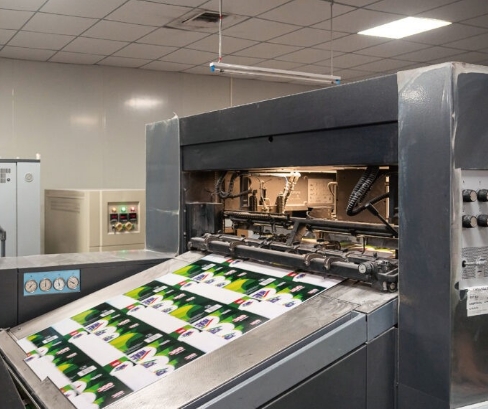
The Importance of Quality Inspection in Printing
Quality inspection in printing ensures that every product meets predefined standards before reaching the customer. It involves checking for color consistency, print accuracy, material defects, and other critical factors. Traditional inspection methods, often manual and time-consuming, are increasingly being replaced by automated systems that offer higher accuracy and efficiency.
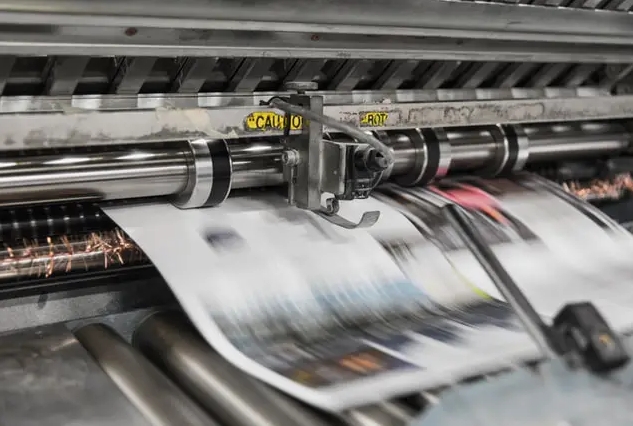
Technologies Enabling Seamless Integration of Quality Inspection Systems with Printing Workflows
Seamless integration of quality inspection systems with printing workflows hinges on a combination of advanced technologies. These technologies work in concert to enhance accuracy, efficiency, and overall quality.
1. High-Resolution Cameras and Sensors
High-resolution cameras and sensors are foundational to modern quality inspection systems. They capture detailed images and data from printed materials, enabling precise detection of defects such as color inconsistencies, misalignments, and material flaws. Key features include:
- Resolution and Clarity: Capable of capturing minute details, ensuring even the smallest defects are identified.
- Speed: High-speed cameras can keep up with fast production lines, providing real-time inspection without slowing down the workflow.
2. Machine Learning and Artificial Intelligence
Machine learning (ML) and artificial intelligence (AI) algorithms play a critical role in analyzing the vast amounts of data generated by inspection systems. These technologies offer several advantages:
- Pattern Recognition: AI algorithms can identify patterns and anomalies that might be missed by traditional methods.
- Continuous Improvement: ML models improve over time as they process more data, leading to increasingly accurate defect detection.
- Customization: Systems can be trained to recognize specific defects pertinent to different printing processes and materials.
3. Real-Time Data Processing
Real-time data processing is essential for immediate defect detection and correction. This technology enables the following:
- Instant Feedback: Systems can alert operators to defects as they occur, allowing for quick adjustments.
- Minimized Waste: By catching defects early, real-time processing reduces material waste and prevents defective products from advancing through the production line.
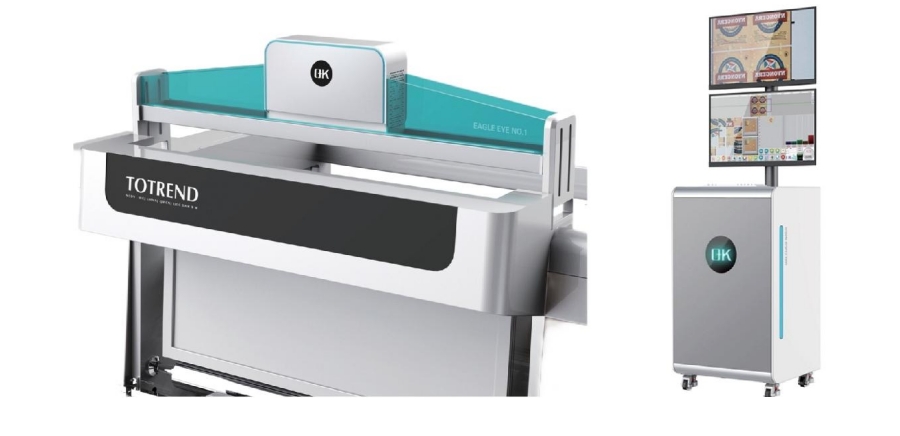
4. Interoperable Software Platforms
Software platforms that facilitate seamless communication between printing machinery and quality inspection systems are vital. These platforms ensure that data flows smoothly and operations are synchronized. Key aspects include:
Integration Capability: Software must integrate with various types of printing equipment and inspection systems.
User-Friendly Interfaces: Intuitive interfaces allow operators to easily monitor and control the inspection process.
Data Management: Effective data management systems store and analyze inspection data, providing insights for continuous improvement.
5. Advanced Image Processing
Advanced image processing technologies enhance the capability of inspection systems to detect and classify print defects accurately. Features include:
- Edge Detection: Identifies edges and contours in printed materials, crucial for assessing print alignment and clarity.
- Color Analysis: Ensures color consistency across prints by analyzing color values and detecting deviations.
- 3D Imaging: Provides a three-dimensional view of printed surfaces, helping detect depth-related defects like embossing errors.
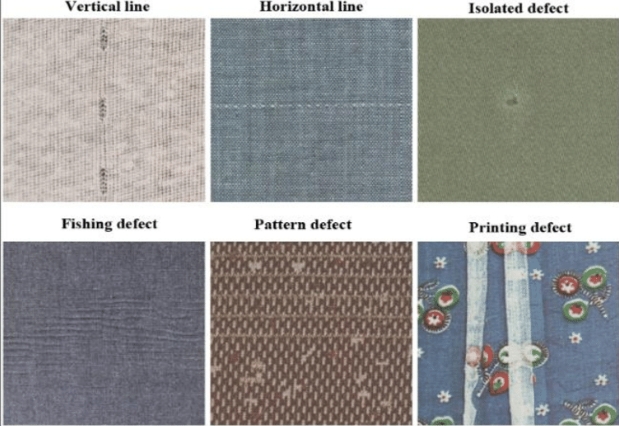
6. Connectivity and IoT
The Internet of Things (IoT) and connectivity technologies enable devices to communicate and share data seamlessly. This interconnectedness offers several benefits:
- Remote Monitoring: Operators can monitor the inspection process remotely, ensuring consistent quality even from offsite locations.
- Predictive Maintenance: IoT devices can predict equipment failures and schedule maintenance proactively, reducing downtime.
- Data Sharing: Real-time data sharing across devices ensures synchronized operations and enhances decision-making.
7. Robotics and Automation
Robotics and automation streamline the inspection process, making it faster and more reliable. Key benefits include:
- Precision Handling: Robots can handle materials with high precision, ensuring consistent positioning for inspection.
- Increased Throughput: Automation speeds up the inspection process, allowing for higher production rates without compromising quality.
- Consistency: Robots provide consistent inspection processes, reducing the variability inherent in manual inspections.
8. Cloud Computing and Big Data Analytics
Cloud computing and big data analytics enable the storage and analysis of vast amounts of inspection data. These technologies provide:
- Scalability: Cloud platforms can scale to accommodate growing data needs.
- Advanced Analytics: Big data tools analyze inspection data to identify trends, root causes of defects, and areas for improvement.
- Accessibility: Data stored in the cloud can be accessed from anywhere, facilitating remote operations and collaboration.
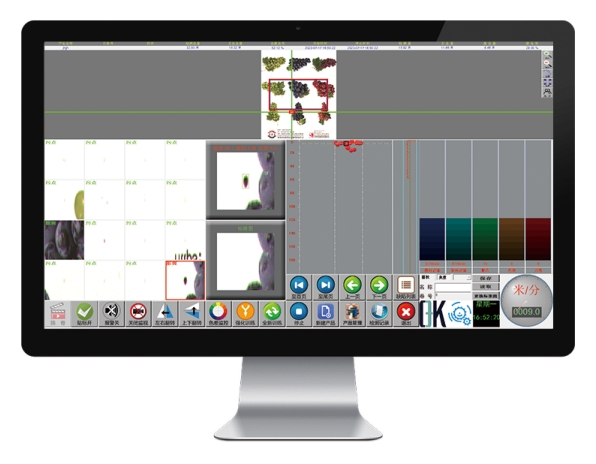
Benefits of Integrating Quality Inspection Systems with Printing Workflows
Integrating quality inspection systems with printing workflows offers numerous benefits that enhance the overall efficiency, accuracy, and profitability of printing operations.
1. Enhanced Quality Control
- Consistent and Objective Assessment: Automated inspection systems provide consistent and objective evaluations of print quality, eliminating the variability and potential biases of manual inspections.
- High Precision: Advanced technologies like high-resolution cameras and AI algorithms can detect minute defects that might be overlooked by human inspectors, ensuring a higher standard of quality.
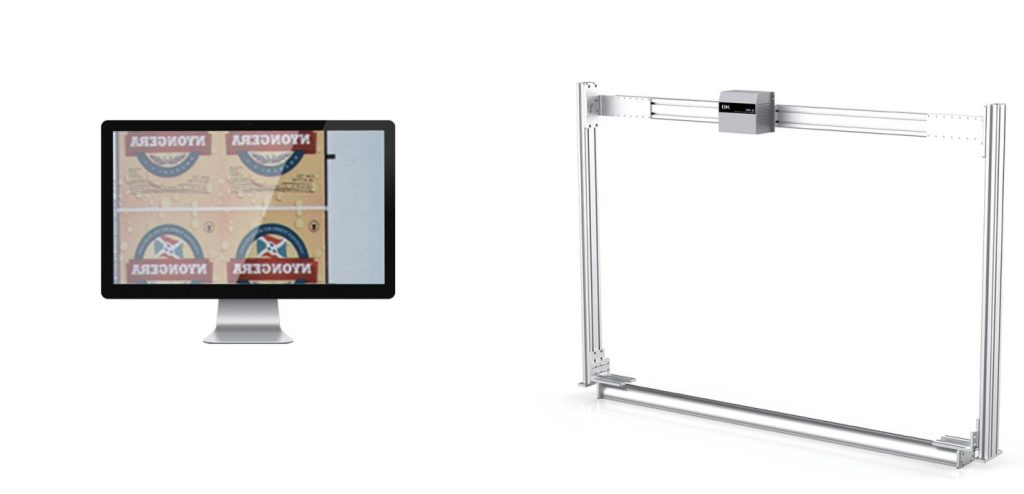
2. Increased Efficiency
- Streamlined Operations: By integrating inspection systems directly into the printing workflow, companies can reduce the time and effort required for separate inspection processes, leading to faster production cycles.
- Reduced Downtime: Real-time detection and correction of defects minimize the need for reprints and reduce production stoppages, enhancing overall workflow efficiency.
- Automated Adjustments: Integrated systems can automatically adjust printing parameters based on inspection feedback, ensuring optimal print quality without manual intervention.
3. Cost Savings
- Reduction in Waste: Early detection of defects prevents defective products from advancing in the production line, reducing material waste and associated costs.
- Lower Labor Costs: Automation of the inspection process reduces the need for manual labor, cutting down on labor costs and reallocating human resources to more strategic tasks.
- Minimized Reprints: By catching defects early, the need for costly reprints is significantly reduced, saving both time and resources.
4. Data-Driven Decision Making
- Valuable Insights: Integrated systems generate comprehensive data on production quality, which can be analyzed to identify trends, recurring issues, and areas for improvement.
- Informed Process Enhancements: Data analysis helps companies make informed decisions about process adjustments and enhancements, leading to continuous improvement in quality and efficiency.
- Resource Allocation: Insights from inspection data enable better resource allocation, ensuring that efforts and investments are directed towards areas with the highest impact on quality and productivity.
5. Compliance and Traceability
- Regulatory Compliance: Quality inspection systems help ensure that products comply with industry standards and regulations, reducing the risk of non-compliance penalties.
- Traceability: Integrated systems provide detailed records of the inspection process, allowing companies to trace the quality of each batch of products. This is crucial for audits, customer assurance, and addressing any quality issues that arise post-production.
- Documented Quality Assurance: Maintaining comprehensive records of quality inspections aids in demonstrating quality assurance to customers and regulatory bodies, enhancing the company’s credibility and reputation.
6. Improved Customer Satisfaction
- Higher Quality Products: Enhanced quality control leads to higher quality products, which in turn increases customer satisfaction and loyalty.
- Consistent Deliverables: Consistency in print quality ensures that customers receive products that meet their expectations every time, fostering trust and long-term relationships.
- Reduced Defects and Returns: By minimizing defects, the incidence of product returns and customer complaints is significantly reduced, leading to a better overall customer experience.
7. Competitive Advantage
- Market Differentiation: Companies that integrate advanced quality inspection systems can differentiate themselves in the market by consistently delivering high-standard printing products.
- Enhanced Reputation: A strong reputation for quality and reliability can attract more customers and lead to increased market share.
- Innovation and Leadership: Embracing advanced technologies for quality inspection positions a company as an industry leader and innovator, which can attract top talent and strategic partnerships.
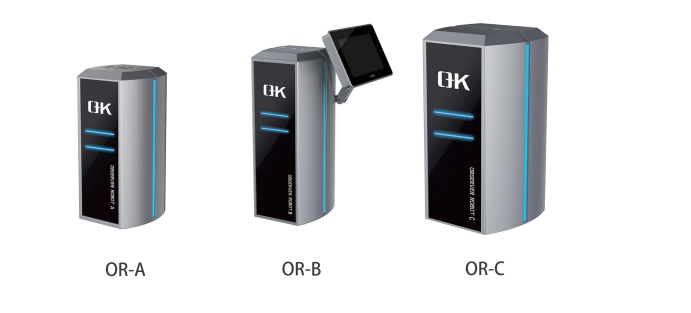
Challenges and Future Solutions in Integrating Quality Inspection Systems with Printing Workflows
Challenges | Future Solutions |
Initial Investment High upfront costs for implementing advanced inspection systems can be a barrier. | Cost Reduction through Technological Advancements As technology advances and becomes more widespread, costs are expected to decrease, making it more accessible for companies of all sizes. |
Compatibility Issues Ensuring that new inspection systems are compatible with existing printing equipment can be complex. | Standardization and Interoperability Development of standardized protocols and interoperable systems to ensure seamless integration with various types of printing machinery. |
Training and Adaptation Staff need training to operate and maintain new systems, leading to a learning curve and potential temporary productivity loss. | User-Friendly Interfaces and Training Programs Implementation of intuitive user interfaces and comprehensive training programs to facilitate quicker adaptation and effective use of new technologies. |
Data Management and Security Managing the vast amount of data generated by inspection systems and ensuring its security can be challenging. | Enhanced Data Management Systems and Security Protocols Development of robust data management systems and advanced security measures to handle large data volumes and protect sensitive information. |
Scalability Scaling inspection systems to match the growth of production capacity can be difficult. | Modular and Scalable Solutions Introduction of modular inspection solutions that can be easily scaled up or down according to production needs. |
Maintenance and Downtime Regular maintenance is required to keep systems running efficiently, and unexpected downtimes can disrupt workflows. | Predictive Maintenance and IoT Integration Utilization of predictive maintenance technologies and IoT integration to anticipate and address maintenance needs proactively, reducing downtime. |
Real-time Processing Limitations Processing inspection data in real-time can be resource-intensive and may face technical limitations. | Advanced Real-time Processing Technologies Development of more powerful real-time processing technologies and optimization algorithms to handle data efficiently and promptly. |
Regulatory Compliance Ensuring compliance with industry standards and regulations can be complex and time-consuming. | Automated Compliance Monitoring Integration of automated compliance monitoring systems to ensure ongoing adherence to regulatory requirements without manual intervention. |
By addressing these challenges with innovative solutions, the printing industry can further optimize the integration of quality inspection systems with workflows, enhancing efficiency, quality, and overall performance.
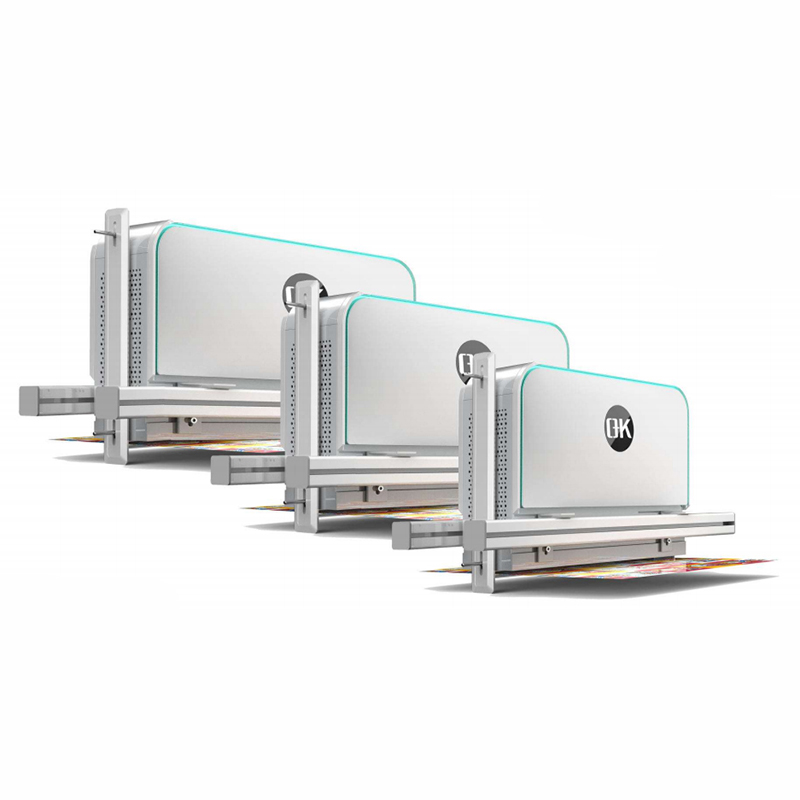
In summary, the seamless integration of quality inspection systems with printing workflows represents a significant advancement in the printing industry. Adopting advanced technologies, companies can enhance quality control, increase efficiency, and achieve substantial cost savings.