How Web Guiding Systems Work in Film and Foil Production
In the film and foil manufacturing, maintaining precise control over material alignment is essential. Whether producing packaging films, aluminum foils, or specialized laminates, any deviation from the correct web path can result in costly defects, wasted material, and production downtime. Web guiding systems can ensure that the continuous roll of web material remains perfectly aligned throughout the production process. This article explores the role, function, benefits, and best practices of web guide systems in film and foil production.
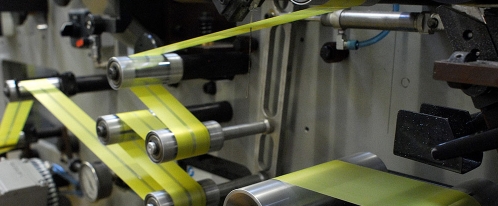
Table of Contents
The Role of Web Guiding Systems in Film and Foil Production
Film and foil materials are produced in continuous rolls that must be precisely guided through processes like coating, laminating, printing, and winding. Web guiding systems are engineered to keep these materials centered or aligned along a designated path, ensuring that each production step occurs accurately and uniformly. This helps avoid problems like wrinkles, misregistration, and uneven tension.
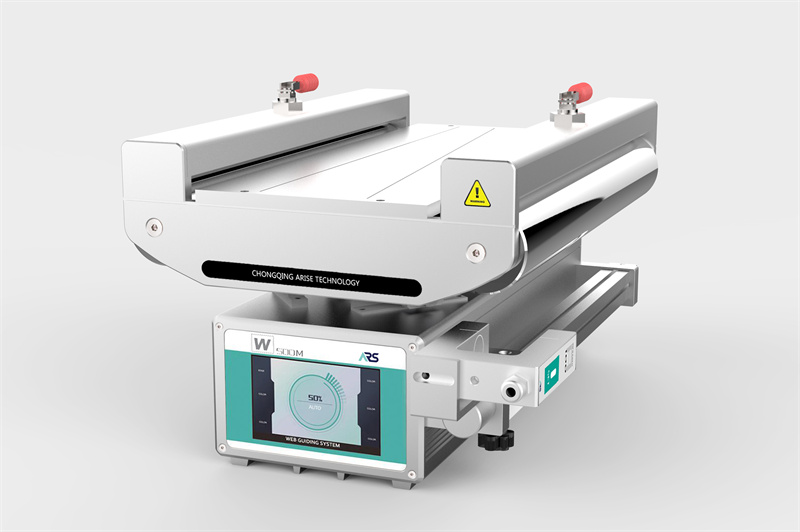
Key Components of a Web Guiding System
A web guiding system is built around three primary components that function together in a closed-loop control cycle: sensors, controllers, and actuators.
- Sensors: These web guiding sensors monitor the lateral position of the web. Depending on the material and application, sensors can be optical, ultrasonic, or infrared. Optical sensors work well with printed or transparent webs, while ultrasonic sensors are effective with opaque or thicker materials. The choice of sensor is critical in detecting web edges or centerlines accurately in real time.
- Controller: Web guide controller is the brain of the system. It receives data from the sensors and compares the current position of the web to a pre-set reference point. If the web is detected to be drifting out of alignment, the controller sends corrective signals to the actuator.
- Actuator: Web guide actuator physically adjusts the position of the web. It can be motor-driven guide rollers, linear actuators, or pivoting frames, depending on the type of guiding required. The actuator responds quickly to the controller’s commands, bringing the web back into proper alignment without interrupting the production process.
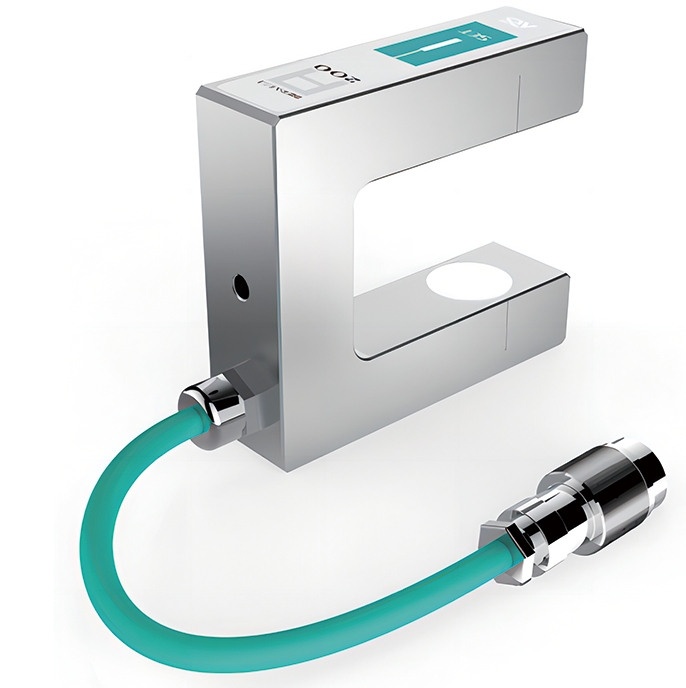
Real-Time Feedback and Correction
Web guiding systems operate in a real-time feedback loop. As the web moves through the production line, the sensors continuously feed data to the controller. The system’s responsiveness allows it to correct even the slightest deviations immediately. This is especially important in high-speed applications, where delay or manual correction is not feasible.
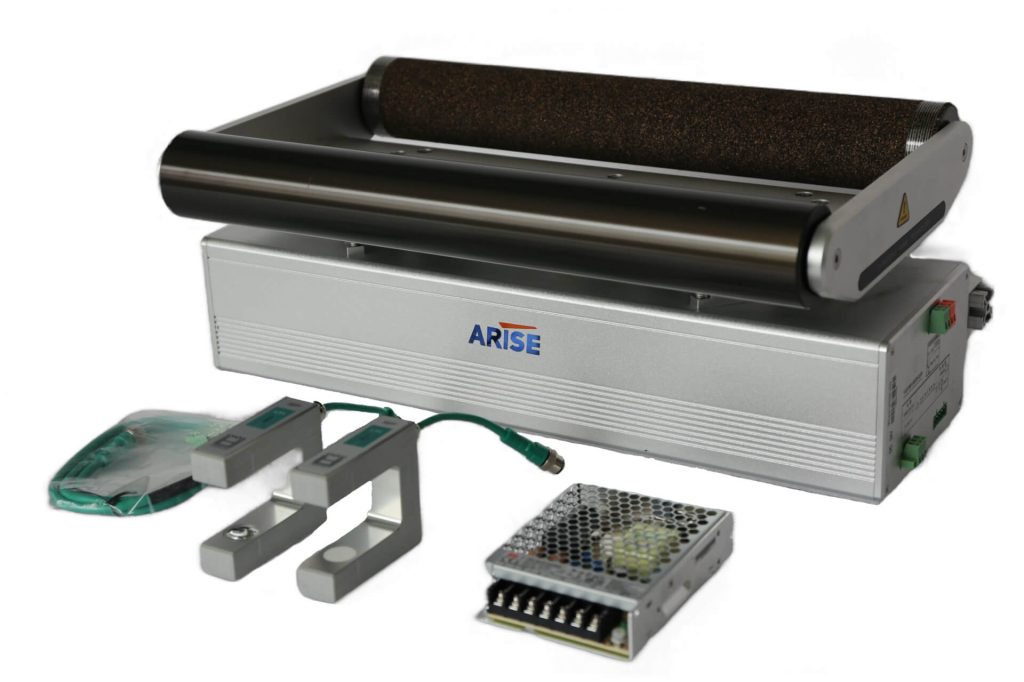
Key Advantages of Web Guiding Systems in Film and Foil Applications
- Precision and Alignment
In film and foil production, materials are processed in high-speed, continuous web formats. These materials, often thin, flexible, and delicate, are prone to misalignment, which can lead to edge damage, wrinkling, and costly defects. Web guiding systems are essential because they ensure these webs stay properly aligned throughout each stage of processing, whether it’s coating, laminating, printing, or slitting.
- Ensuring High Product Quality
Product quality is directly influenced by the accuracy of web positioning. Misalignment can cause poor print registration, uneven coating, or flawed laminates, making the end product unsellable. Web guiding systems maintain consistent lateral positioning, helping manufacturers achieve precise and uniform results across every roll produced.
- Minimizing Waste and Material Loss
By continuously correcting the web’s path in real time, web guiding systems help prevent material drift that leads to unusable output. This minimizes scrap rates, conserves raw materials, and supports sustainable production practices—an increasingly important goal for today’s film and foil manufacturers.
- Reducing Downtime and Manual Intervention
Without a guiding system, operators would need to manually monitor and adjust the web’s position, especially at high speeds. This not only slows down production but increases the risk of human error. Web guiding control systems automate this process, reducing downtime and enabling longer, uninterrupted runs.
- Supporting Smart Manufacturing
Modern web guide systems often come with digital controllers, remote access features, and data integration capabilities. These technologies allow operators to monitor performance in real time, analyze web behavior, and make proactive adjustments. As a result, manufacturers can maintain optimal efficiency while embracing Industry 4.0 standards.
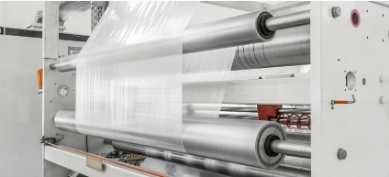
Types of Web Guiding Systems Used in Film and Foil Production
Different types of web guiding systems are employed depending on the application, material type, and alignment requirements. Each system is engineered to correct lateral deviations using specific mechanical and control strategies.
1. Edge Guiding Systems
Edge web guiding systems monitor and control the position of one edge of the web. They use edge-detecting sensors—such as optical or ultrasonic sensors—to follow the material’s edge and keep it aligned with a set reference point. These systems are ideal for operations where maintaining a constant edge position is crucial, such as slitting or rewinding.
Best For:
- Uniform-width webs
- Applications requiring consistent edge alignment
- Simpler production lines
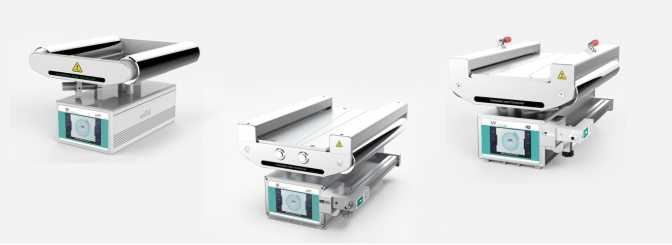
2. Center Guiding Systems
Center web guiding systems focus on keeping the centerline of the web aligned rather than just one edge. Sensors detect both edges to calculate the center point, and actuators adjust the web position accordingly. This method is beneficial when material width varies or symmetrical processes, like coating or printing, require alignment around the web’s center.
Best For:
- Variable-width materials
- Symmetrical processes (e.g., gravure printing, laminating)
- Applications demanding high accuracy
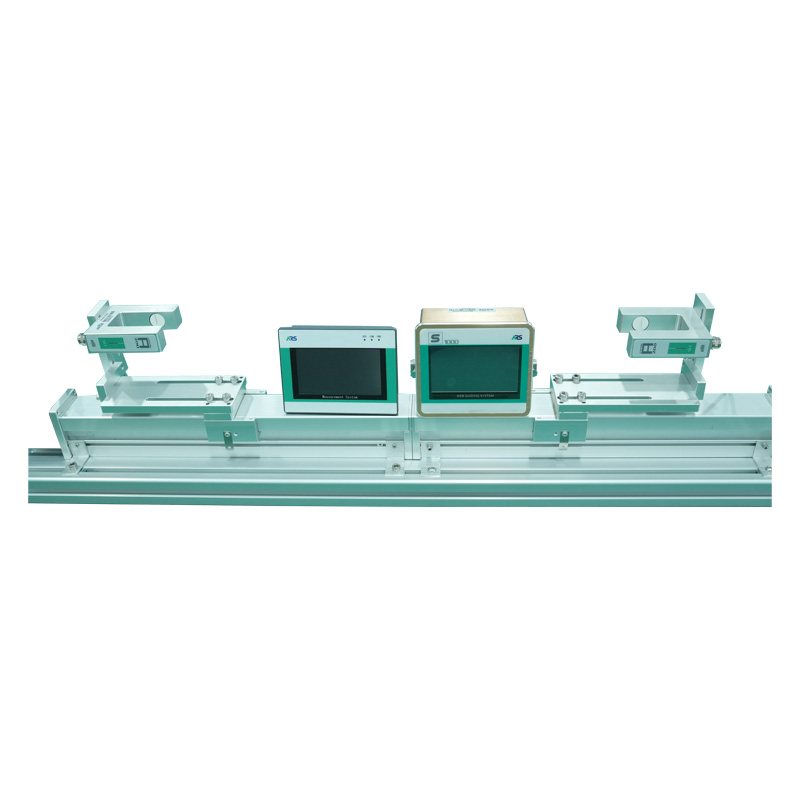
3. Line Guiding Systems
Line guiding systems use contrast-based sensors to follow printed lines or patterns on the web rather than physical edges. This method is particularly effective for pre-printed films or foils where the visual element needs precise positioning, such as in label printing or decorative foils.
Best For:
- Printed or pre-patterned materials
- High-speed print registration
- Applications requiring visual pattern alignment
4. Pivot Frame Guiding Systems
This system utilizes a pivoting guide frame to make angular corrections to the web path. By rotating the entire guiding section, it gently steers the web back to the correct alignment. Pivot frame systems are widely used due to their ability to handle light to medium web tensions effectively.
Best For:
- General-purpose guiding
- Medium-speed production lines
- Compact layout requirements
5. Steering Roller Guiding Systems
Steering roller systems make use of rotating rollers that adjust the web’s path. These are suitable for heavier materials or higher web tensions, providing more forceful and accurate correction compared to pivot frames.
Best For:
- Heavy webs or high-tension applications
- Long web paths
- High-speed operations
6. Displacement Guiding Systems
These systems shift the web laterally without altering its entry or exit angle, making them suitable for areas where space constraints prevent angular corrections. Displacement guides are often used for narrow webs or in zones with fixed roller arrangements.
Best For:
- Tight-space installations
- Delicate materials
- Minimal angular deviation requirements
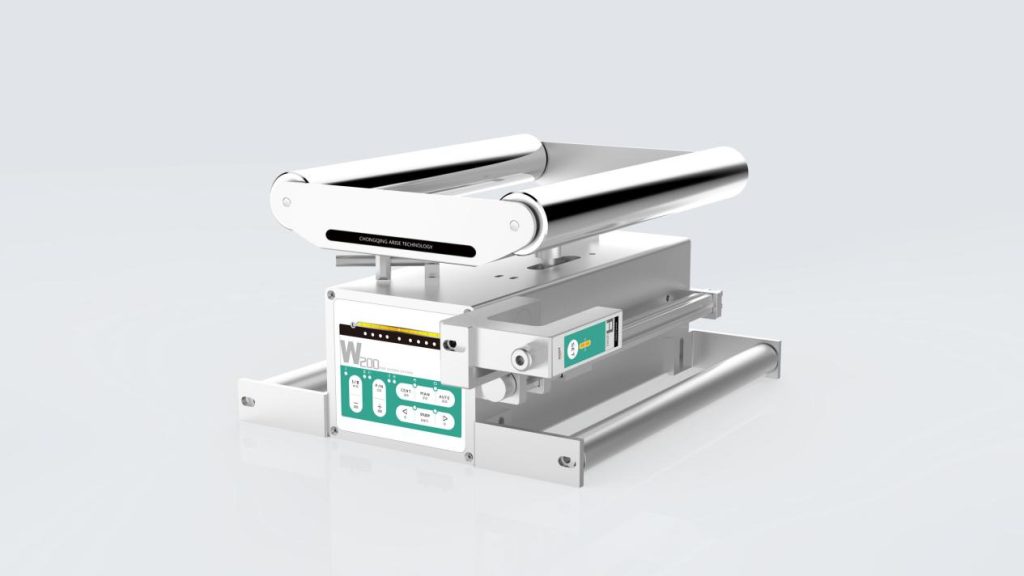
Best Practices for Using Web Guiding Systems in Film and Foil Production
Best Practice | Description | Benefit |
Sensor Selection and Placement | Choose appropriate sensors (optical, ultrasonic, line-following) based on material type. | Ensures accurate web detection and minimizes misreads. |
Routine Calibration and Alignment | Regularly calibrate sensors and check mechanical alignment of guides. | Maintains precision and prevents drift or errors. |
Consistent Tension Control | Use tension control systems or dancer rolls to maintain stable web tension. | Prevents wrinkles and ensures smooth guiding. |
Regular Maintenance | Clean sensors and inspect actuators and rollers periodically. | Extends system lifespan and improves performance. |
System Integration | Integrate web guiding systems with central control or PLC systems for real-time monitoring. | Enables better process control and quicker troubleshooting. |
Operator Training | Train staff on system operation, troubleshooting, and safety protocols. | Reduces downtime and human error during operation. |
Adaptation to Material Variability | Adjust guiding settings when switching between different web materials or widths. | Ensures accuracy across diverse production runs. |
Use of Feedback Systems | Implement closed-loop feedback where applicable for automatic correction. | Improves dynamic response and correction accuracy. |
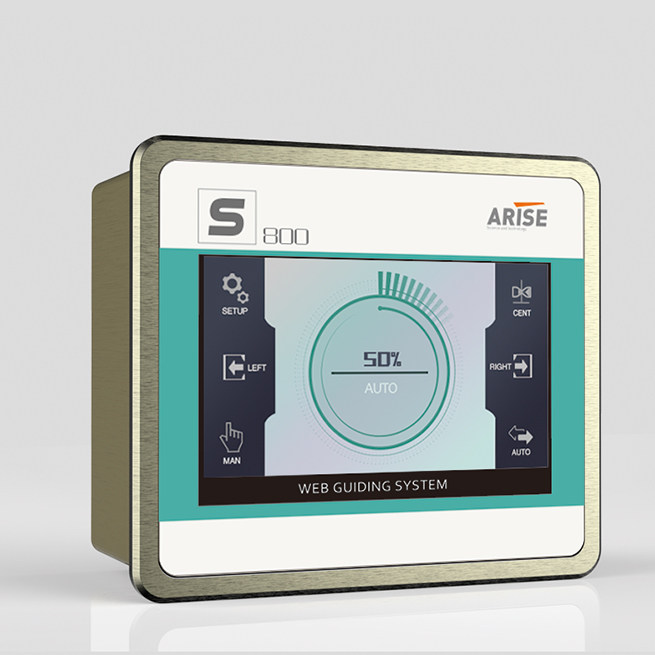
Final Thoughts
Web guiding systems can keep the web on its intended path, reducing defects, lowering waste, and improving throughput of film and foil production lines. As production demands continue to grow, the role of precise web handling becomes even more critical. For manufacturers in the film and foil industry, adopting advanced web guiding technologies is not just about process optimization and it’s about delivering high-quality products with consistent quality and reliability.