What are Key Miniaturization Techniques in Tension Sensors
In the applications of tension sensors, miniaturization is crucial for creating compact, efficient, and precise instruments capable of measuring forces in applications where space and weight are critical constraints. This article explores the techniques used to miniaturize tension sensors, their advantages, and the applications benefiting from these advancements.
Understanding Tension Sensors
Tension sensors measure the force exerted along a flexible medium, such as a cable, wire, or fiber, which is crucial in applications where precise force measurement is required, including industrial machinery, robotics, medical devices, and aerospace systems. Miniaturizing these sensors involves reducing their size and weight while maintaining or enhancing their accuracy, reliability, and functionality.
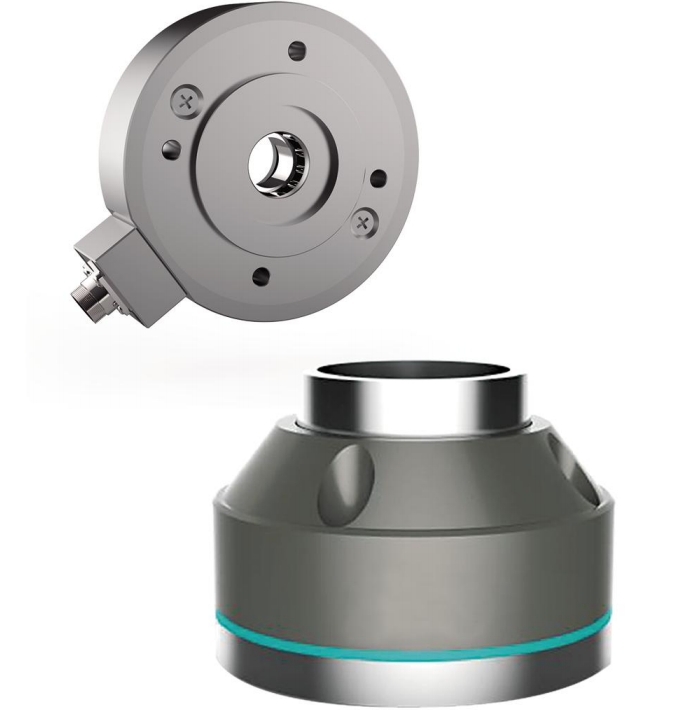
Key Techniques Employed to Achieve Miniaturization in Tension Sensors
1. Advanced Materials
Microelectromechanical Systems (MEMS)
MEMS technology incorporates microscopic mechanical and electromechanical elements. MEMS-based tension sensors use tiny mechanical parts, typically fabricated from silicon, to measure tension. The benefits of MEMS technology include:
- Compact Size: Microelectromechanical system devices can be made very small, fitting into spaces where traditional sensors cannot.
- Integration: MEMS sensors can integrate multiple functions (e.g., sensing, signal processing) on a single chip.
- Low Power Consumption: Microelectromechanical Systems devices typically consume less power, which is advantageous in battery-operated applications.
Nano-materials
Nano-materials, such as carbon nanotubes and graphene, offer exceptional strength-to-weight ratios and excellent electrical properties, which are ideal for miniaturized tension sensors. The advantages include:
- High Sensitivity: Nano-materials provide high sensitivity due to their large surface area to volume ratio.
- Durability: These materials are robust and can withstand harsh environments.
- Lightweight: Nano-materials contribute to reducing the overall weight of the sensor.
2. Integrated Electronics
System-on-Chip (SoC)
SoC technology integrates all necessary electronic components, including sensors, processors, and communication modules, onto a single chip. This consolidation reduces size and complexity, offering several benefits:
- Miniaturization: Combining all components into one chip drastically reduces the overall footprint.
- Performance: SoC solutions often provide faster processing and improved performance.
- Energy Efficiency: SoC designs can be optimized for low power consumption.
3. Application-Specific Integrated Circuits (ASICs)
ASICs are custom-designed circuits tailored for specific applications. Using ASICs in tension sensors allows for the integration of specific functionalities, leading to:
- Reduced Size: Customization ensures that only necessary components are included, minimizing size.
- Enhanced Functionality: ASICs can be designed to handle complex signal processing directly within the sensor package.
- Improved Reliability: ASICs can be optimized for the specific operating conditions of the sensor, enhancing reliability.
4. Microfabrication Techniques
Photolithography
Photolithography is a process used to pattern precise and intricate features on a substrate. It is essential for creating micro-scale components in miniaturized tension sensors. Key benefits include:
- Precision: Photolithography allows for highly accurate patterning of sensor elements.
- Scalability: This technique is well-suited for mass production, ensuring consistency and reliability.
Etching Processes
Etching processes, including wet and dry etching, are used to remove material selectively and create micro-scale features. The advantages are:
- Detailing: Etching can produce fine details necessary for miniature components.
- Versatility: Different etching techniques can be used for various materials and applications.
5. Wireless Technology
Bluetooth Low Energy (BLE) and Near Field Communication (NFC)
Incorporating wireless communication technologies, such as BLE and NFC, eliminates the need for bulky connectors and wires. Benefits include:
- Reduced Size: Wireless technology removes the need for physical connectors, shrinking the sensor size.
- Ease of Integration: Wireless sensors can be easily integrated into existing systems.
- Remote Monitoring: Enables real-time data transmission and remote monitoring capabilities.
6. Packaging and Assembly
3D Printing
3D printing technology allows for the creation of complex and custom sensor housings that optimize space usage. The advantages of 3D printing in miniaturization include:
- Customization: Tailored designs can be created to fit specific application needs.
- Rapid Prototyping: Quick iterations and prototyping are possible, speeding up development cycles.
- Complex Geometries: 3D printing can produce complex shapes that traditional manufacturing methods cannot.
Micro-assembly
Automated micro-assembly techniques enable the precise placement and bonding of miniature components. This ensures high accuracy and repeatability, crucial for maintaining performance in miniaturized tension sensors. Benefits include:
- Precision: High-precision placement of components ensures sensor accuracy.
- Scalability: Automated assembly allows for consistent production at scale.
- Reliability: Micro-assembly techniques enhance the overall reliability of the sensor by ensuring consistent quality.
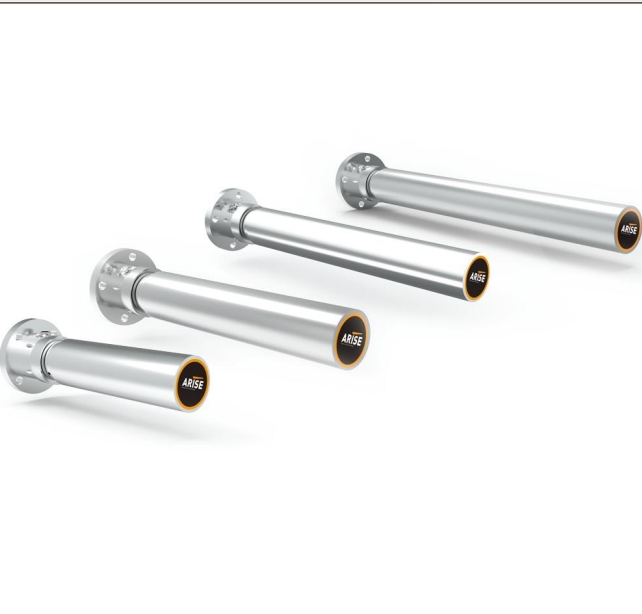
Applications Benefiting from Miniaturized Tension Sensors
1. Medical Devices
Wearable Health Monitors
Miniaturized tension sensors are integral to wearable health monitors that track physical activity, heart rate, and other vital signs. Their small size ensures comfort and unobtrusiveness for continuous monitoring.
Surgical Instruments
In minimally invasive surgery, miniaturized tension sensors provide precise force measurements, aiding surgeons in performing delicate procedures with greater accuracy and control. These sensors help in preventing excessive force application that could damage tissues.
Implantable Devices
Implantable medical devices, such as pacemakers and drug delivery systems, benefit from miniaturized tension sensors due to their small footprint and high reliability. These sensors ensure the proper functioning of the devices while occupying minimal space within the body.
2. Aerospace Engineering
Satellite Systems
Weight and space constraints are critical in satellite design. Miniaturized tension sensors are used to monitor structural integrity and ensure the proper tension of cables and other components, contributing to the satellite’s reliability and performance.
Unmanned Aerial Vehicles (UAVs)
In UAVs, miniaturized tension sensors help manage and monitor the forces in control surfaces and structural components. Their lightweight nature is crucial for maintaining the UAV’s payload capacity and flight efficiency.
Structural Health Monitoring
Aerospace structures, such as aircraft wings and fuselage, require constant monitoring to detect stress and strain. Miniaturized tension sensors embedded within these structures provide real-time data, enhancing safety and maintenance efficiency.
3. Robotics
Precision Grippers
Miniaturized tension sensors enable robotic grippers to handle delicate objects with precision. These sensors provide feedback on the force applied, preventing damage to fragile items and improving the robot’s dexterity.
Robotic Joints
In robotic arms and other articulated systems, miniaturized tension sensors monitor the forces exerted at joints, ensuring smooth and precise movements. This is essential for tasks that require high accuracy, such as assembly and surgical robots.
Autonomous Systems
Autonomous robots in various industries, from manufacturing to exploration, use miniaturized tension sensors to navigate and manipulate objects in their environment. These sensors contribute to the robots’ ability to perform complex tasks autonomously.
4. Industrial Automation
Machinery and Equipment Monitoring
In industrial settings, miniaturized tension sensors are integrated into machinery to monitor the forces during operation. This helps in preventing equipment failure, reducing downtime, and improving overall efficiency.
Conveyor Systems
Tension sensors ensure that conveyor belts maintain the correct tension, preventing slippage and optimizing the transportation of materials. Miniaturized sensors are ideal for integration into compact conveyor systems.
Assembly Lines
Automated assembly lines use miniaturized tension sensors to apply precise forces during component assembly. This ensures consistency and quality in the manufacturing process, especially for delicate or high-precision parts.
5. Consumer Electronics
Wearable Technology
Miniaturized tension sensors are used in smartwatches, fitness trackers, and other wearable devices to monitor user activity and provide haptic feedback. Their small size allows them to be embedded in compact, lightweight designs.
Smartphones and Tablets
In mobile devices, miniaturized tension sensors can be used to detect pressure on screens or buttons, enabling force-sensitive touch interfaces and enhancing user interaction.
6. Automotive Industry
Advanced Driver-Assistance Systems (ADAS)
Miniaturized tension sensors are used in ADAS to monitor the forces in steering systems and suspension components. This data helps improve vehicle safety and performance by enabling real-time adjustments.
Electric Vehicles (EVs)
In EVs, tension sensors monitor the stress on battery packs and other critical components. Their small size and high precision help in optimizing the vehicle’s performance and ensuring safety.
7. Research and Development
Scientific Instruments
Miniaturized tension sensors are essential in scientific research, where precise force measurements are required in experiments and instrumentation. Their small size allows them to be used in a wide range of experimental setups.
Material Testing
In material science, miniaturized tension sensors help in testing the tensile strength and elasticity of new materials. Their high precision and reliability are crucial for accurate data collection.
Conclusion
The miniaturization of tension sensors is a rapidly advancing field, driven by innovations in materials, fabrication techniques, and electronics integration. These advancements enable the development of compact, efficient, and precise sensors that meet the demands of modern applications across various industries.