What Is Web Guide PID Controller
PID control in a web guiding system improves precision, reduces variability, has a faster response time, and is adaptable to varied web materials. In this section, we will define web guide PID controller and discuss its definition, operating principle, benefits, applications, and obstacles related with its use.
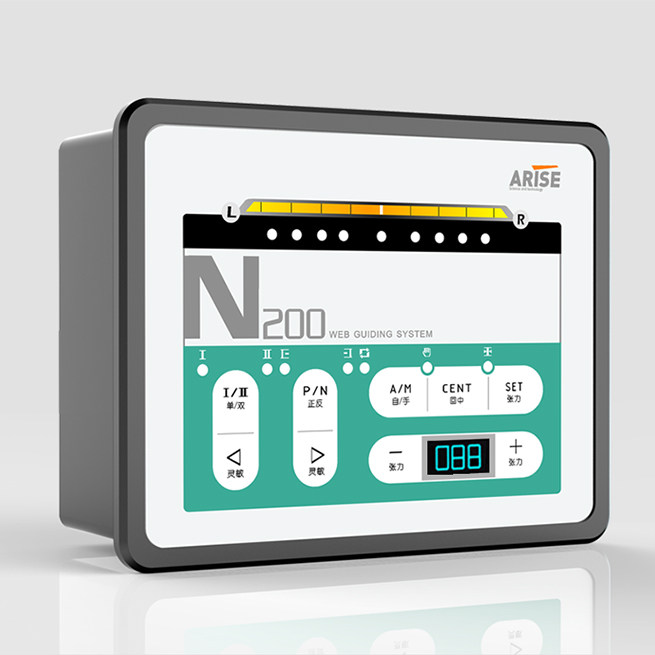
Definition of Web Guide PID Controller
A web guide PID (Proportional-Integral-Derivative) controller is a closed-loop control system that uses sensor feedback to automatically modify the location of a moving web material, such as paper, plastic, or fabric, in order to keep it aligned with a desired route or edge. The web guide controller continuously checks the web material’s position and calculates an error signal based on the difference between the desired and actual positions. The PID controller then modifies the output of an actuator, such as a motor or pneumatic cylinder, to correct the web material’s position. The PID controller employs three control components to alter the output signal based on the error signal, the rate of change of the error signal, and the integral of the error signal over time, respectively.
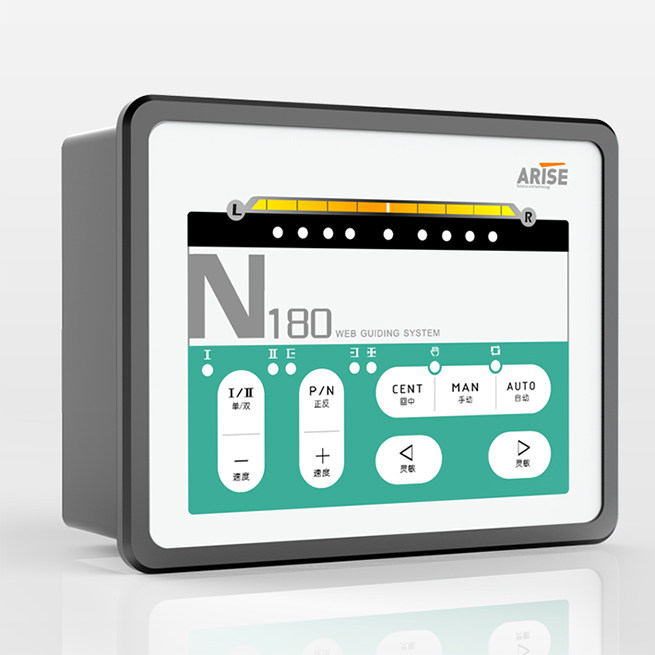
Working Principle of Web Guide PID Controller
The working principle The web guide PID controller is concerned with keeping a moving web material aligned.
The internet manual using one or more sensors, the PID controller continuously monitors the position of the web material. Depending on the application, these sensors could be edge guide sensors, line sensors, or other types of sensors. The controller calculates an error signal based on the difference between the actual position of the web material and a desired path or edge.
The PID controller then modifies the output of an actuator, such as a motor or pneumatic cylinder, to correct the web material’s position. The actuator may be connected to a guide roller, a steering roller, or another component of the web handling system, depending on the specific design.
The PID controller’s Proportional, Integral, and Derivative components are used to alter the output signal based on the error signal, the rate of change of the error signal, and the integral of the error signal over time, in that order. This allows the controller to make precise and accurate adjustments to the web material’s position.
The proportional component of the PID controller is typically used in a web guiding system to respond quickly to changes in the position of the web material, while the integral component is used to eliminate steady-state errors and the derivative component is used to reduce overshoot and dampen the response to disturbances.
The PID controller’s tuning parameters can be changed to maximize its performance for varied web materials, speeds, and other operating situations. Depending on the complexity of the web handling system, the web guide PID controller can be set to work in various modes, such as single-axis, dual-axis, or multi-axis control.
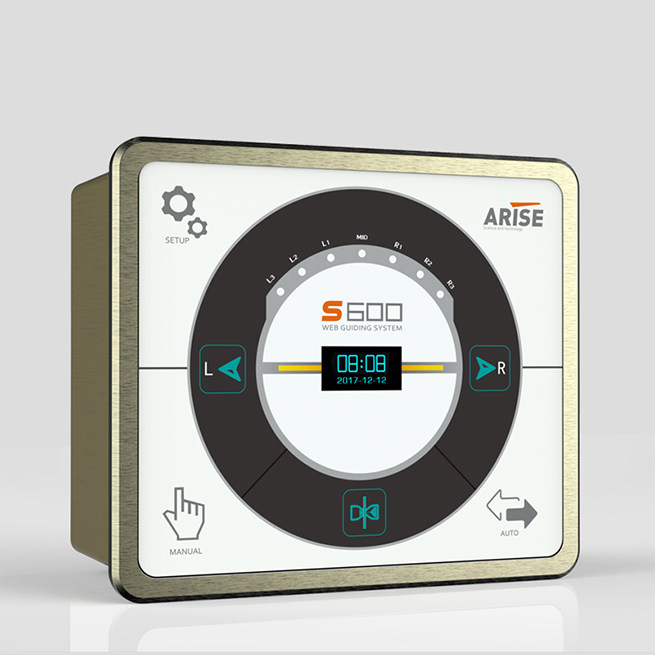
Advantages of Web Guide PID Controller
Improved accuracy and precision
The PID controller can precisely modify the location of the web material, improving the accuracy and precision of the web handling system.
Reduced waste
The web guide controller can eliminate waste caused by misalignment, wrinkling, or other material flaws by ensuring correct alignment of the web material.
Increased productivity
The controller can keep the web material aligned at high speeds, increasing the web handling system’s productivity.
Flexibility
Depending on the complexity of the web handling system, the PID controller can be set to work in various modes, such as single-axis, dual-axis, or multi-axis control. This makes it a versatile solution for a variety of web-handling applications.
Adaptability
To maintain perfect alignment of the web material, the web guide controller can respond to changes in the web handling system, such as variations in web speed, tension, or material qualities.
Reduced operator intervention
The web guide PID controller can run autonomously, minimizing the requirement for user intervention and boosting the system’s reliability.
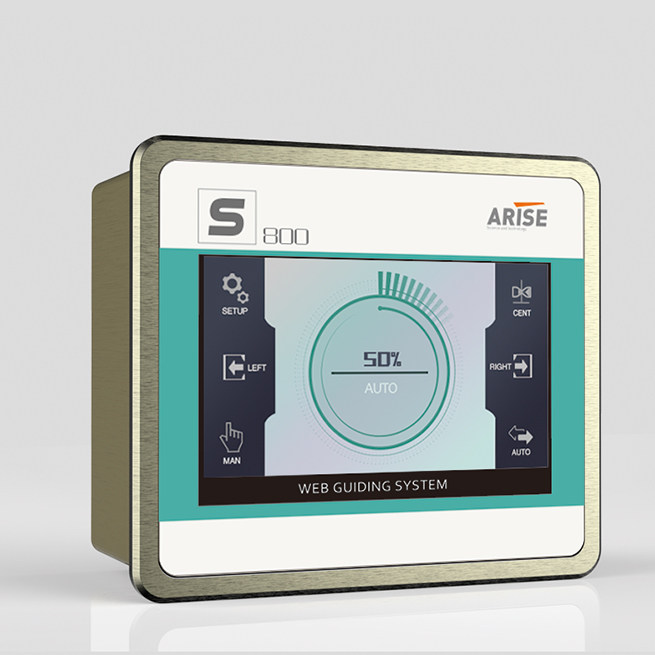
Wide Applications of Web Guide PID Controller
Web guide PID controllers are used in a wide range of manufacturing and processing applications where precise control of web materials is required.
Printing
In printing applications, web guide PID controllers are used to maintain accurate alignment of the web material during printing, reducing waste and improving print quality.
Converting
Web guide PID controllers are used in converting applications such as cutting or slitting of materials to maintain correct alignment of the web material, decreasing waste and enhancing the quality of the converted result.
Packaging
Web guides are used in packaging applications. PID controllers are utilized to maintain correct web material alignment during packaging operations, decreasing waste and improving packaged product quality.
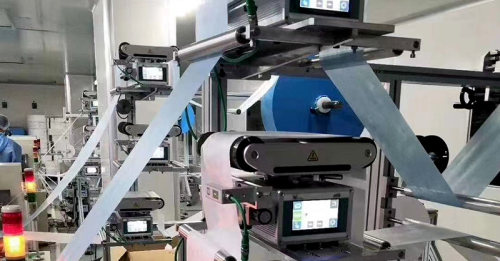
Coating
Web guide PID controllers are used in coating applications, such as coating films or papers, to maintain correct alignment of the web material, enhancing the quality of the coated result.
Textile
Web guide PID controllers are used in textile applications to maintain perfect fabric alignment during weaving or knitting operations, hence reducing wastage and improving quality.
Automotive
Web guide PID controllers are used in automotive production applications to maintain the perfect alignment of materials during processes such as cutting, stamping, or laminating, hence improving the quality of the produced automobile parts.
Challenges of Web Guide PID Controller
While web guide PID controllers have many advantages in web handling systems, they also have some challenges.
Non-linear behavior of web materials
Web materials can display non-linear behavior, making it difficult to predict and regulate the position of the material. In the control system, this might cause oscillations or overshoot.
Varying material properties
The features of web materials, such as thickness, elasticity, or surface characteristics, might influence the behavior of the web handling system. This can make tuning the PID controller for optimal performance challenging.
External disturbances
External disturbances, such as changes in web tension or air drafts, might impact the position of the web material, resulting in control system inaccuracies.
Sensor placement and accuracy
The accuracy and positioning of sensors used to measure the position of the web material can have an impact on the control system’s performance. Incorrect control actions can be caused by inaccurate sensor readings.
Maintenance and calibration
To ensure optimal performance, the PID controller and accompanying hardware components must be serviced and calibrated on a regular basis. This may necessitate downtime for the web handling system, which may have an impact on production timelines.
Cost
Implementing a web guide PID controller can be expensive, especially for complicated web handling systems with several axes of control.
Summary
Web guide PID controller is an important technology for managing the position of web materials, allowing manufacturers and processors to improve efficiency and product quality, minimizing waste.