Exploring the Advancements in Surface Inspection of Printed Materials
Ensuring the quality of printed materials is important, as defects can impact brand reputation, customer satisfaction, and overall product performance. Surface inspection systems play a crucial role in detecting and addressing defects, ensuring that printed materials meet the highest standards of quality. Surface inspection involves various techniques and technologies to scrutinize the printed surface for imperfections such as misprints, color deviations, streaks, smudges, and scratches. This article explores the significance of surface inspection of printed materials and highlights advancements in printing inspection technologies.
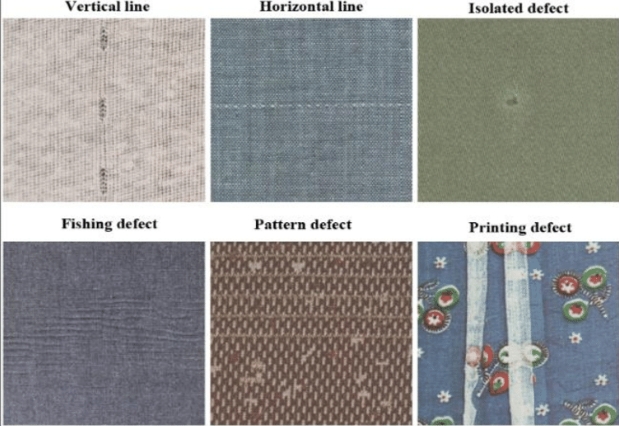
Importance of Surface Inspection in Printed Materials
1. Quality Assurance
Surface inspection helps maintain high standards of quality by identifying and rectifying defects such as misprints, color inconsistencies, streaks, smudges, and registration errors. Ensuring that printed materials meet quality specifications is vital for customer satisfaction and brand reputation.
2. Compliance and Consistency
In industries like packaging and labeling, compliance with regulatory requirements and brand consistency is crucial. Surface inspection ensures that printed materials adhere to color, content, safety, and legal standards consistently across batches.
3. Minimizing Waste
Detecting defects early in the printing process helps minimize material waste and rework. Surface inspection allows for proactive measures to address issues promptly, reducing production downtime and cost overruns associated with remanufacturing.
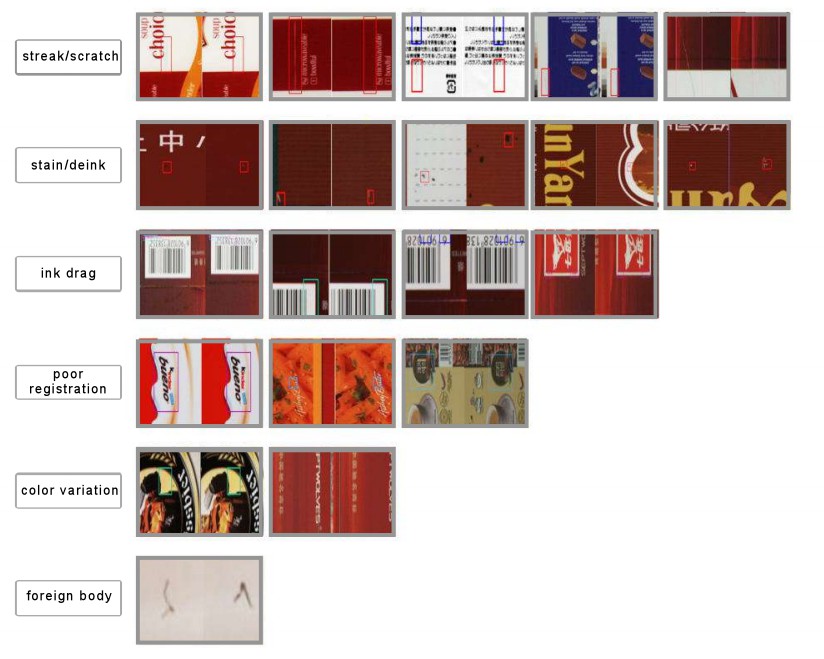
4. Preventing Defective Products
Surface inspection helps prevent the distribution of defective products to consumers, which can lead to customer complaints, returns, and damage to brand reputation. By identifying and addressing defects before products leave the production facility, manufacturers can uphold quality standards and avoid costly recalls.
5. Optimizing Production Efficiency
Surface inspection systems can be integrated into the printing process to provide real-time feedback to operators. This allows for immediate adjustments and corrections, optimizing production efficiency and reducing the likelihood of producing substandard materials.
6. Ensuring Print Accuracy
Surface inspection verifies print accuracy, readability, and alignment, ensuring that text, graphics, and images are reproduced faithfully according to the original design. This is essential for maintaining the visual appeal and usability of printed materials.
7. Security and Authenticity
In applications such as security printing (e.g., currency, passports, ID cards), surface inspection helps ensure the authenticity and integrity of printed security features. Detecting counterfeit or tampered documents is critical for security and fraud prevention.
8. Customer Satisfaction
High-quality printed materials contribute to positive customer experiences and perceptions of a brand. Surface inspection helps deliver products that meet or exceed customer expectations in terms of appearance, durability, and functionality.
Techniques and Technologies Used in Surface Inspection of Printed Materials
1. Automated Optical Inspection (AOI)
- Principle: AOI systems use high-resolution cameras and advanced image processing algorithms to capture detailed images of the printed surface.
- Functionality: These automated printing inspection systems can inspect the surface of printed materials at high speeds, detecting defects such as misprints, color variations, registration errors, and print quality issues.
- Applications: AOI is widely used in the printing industry for quality control in applications such as packaging, labels, newspapers, and commercial printing.
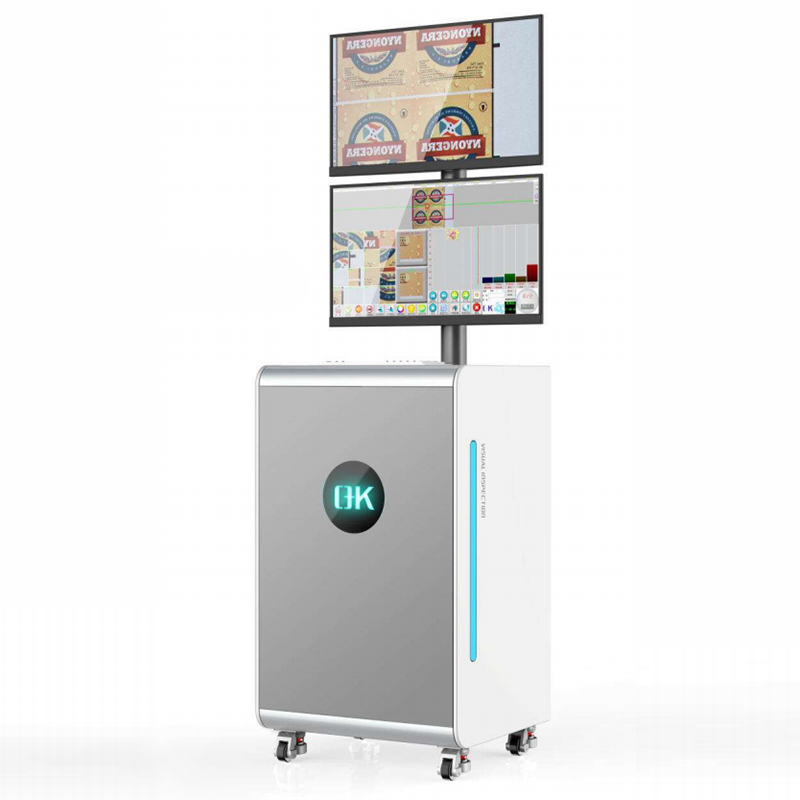
1. Spectrophotometry
- Principle: Spectrophotometric devices measure color accuracy and consistency by analyzing the spectral characteristics of printed materials.
- Functionality: These devices quantify color values and compare them against predefined color standards to ensure consistency across batches.
- Applications: Spectrophotometry is used to verify color accuracy and maintain color consistency in printed materials, ensuring compliance with brand standards and regulatory requirements.
2. 3D Surface Profiling
- Principle: 3D surface profiling technologies employ laser or optical sensors to create detailed three-dimensional maps of printed surfaces.
- Functionality: These systems capture surface topography and detect defects such as embossing errors, substrate irregularities, and print thickness variations.
- Applications: 3D surface profiling is used to ensure the structural integrity and dimensional accuracy of printed materials, particularly in applications where surface topography is critical, such as packaging and security printing.
3. Artificial Intelligence (AI) and Machine Learning
- Principle: AI-powered inspection systems use machine learning algorithms to analyze vast datasets of images and recognize patterns indicative of defects.
- Functionality: These systems continuously improve their defect detection capabilities by learning from labeled data and adapting to changing printing conditions.
- Applications: AI and machine learning are increasingly used in surface inspection to enhance defect detection accuracy, reduce false positives, and improve overall inspection efficiency.
4. Real-time Monitoring and Control
- Principle: Integrated inspection systems provide real-time feedback during the printing process, allowing operators to identify and address defects as they occur.
- Functionality: These systems enable proactive quality control measures, minimizing the risk of producing substandard materials and reducing production downtime.
- Applications: Real-time monitoring and control systems optimize production efficiency by detecting and correcting defects on the fly, ensuring that printed materials meet quality standards consistently.
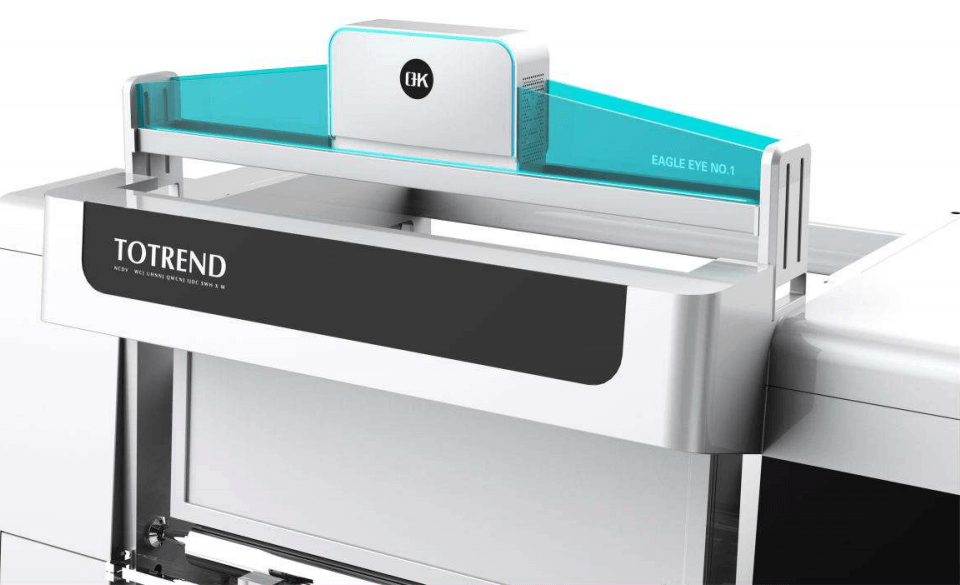
Key Applications of Surface Inspection in Printed Materials
1. Packaging Industry
- Quality Control: Surface inspection ensures the integrity and appearance of printed packaging materials such as cartons, boxes, and wrappers. It detects defects like misprints, color variations, and registration errors, ensuring that packaging meets brand standards and regulatory requirements.
- Barcodes and Labels: Surface inspection verifies the accuracy and readability of printed barcodes, labels, and product identification codes. It ensures that information is legible and compliant with industry standards, facilitating product identification and traceability.
2. Labeling and Branding
- Brand Consistency: Surface inspection maintains consistency in branding elements such as logos, colors, and typography across different printed materials. It ensures that brand identity is preserved and reinforced, enhancing brand recognition and consumer trust.
- Security Features: Surface inspection verifies the presence and integrity of security features such as holograms, watermarks, and microtext. It helps prevent counterfeiting and tampering, safeguarding the authenticity of branded products and documents.
3. Publishing and Printing
- Print Quality: Surface inspection ensures the visual appeal and readability of printed materials such as books, magazines, and newspapers. It detects defects like ink smudges, streaks, and misregistration, maintaining print quality and readability for consumers.
- Color Consistency: Surface inspection verifies color accuracy and consistency across different pages and print runs. It ensures that colors match predefined standards and maintain consistency throughout the publication, enhancing visual appeal and reader experience.
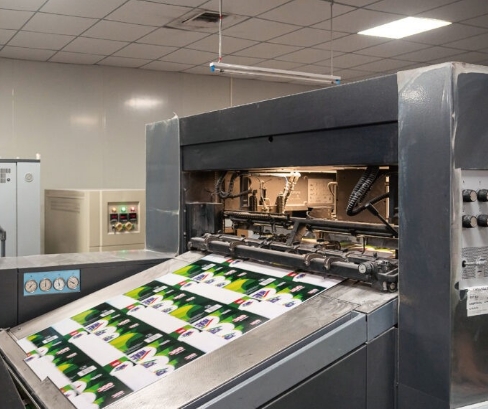
4. Commercial Printing
- Marketing Collaterals: Surface inspection ensures the quality and accuracy of marketing collaterals such as brochures, flyers, and posters. It detects defects like print artifacts, blurs, and color deviations, ensuring that marketing materials effectively communicate the intended message to the target audience.
- Proofing and Prototyping: Surface inspection helps validate proofs and prototypes before mass production, ensuring that designs are executed accurately and meet client expectations. It enables timely adjustments and corrections, reducing the risk of costly reprints and client dissatisfaction.
5. Security Printing
- Currency and Identification Documents: Surface inspection ensures the authenticity and integrity of security features in printed currency, passports, ID cards, and other sensitive documents. It detects defects or anomalies that may indicate counterfeiting or tampering, safeguarding the security and integrity of printed materials.
- Secure Labels and Packaging: Surface inspection verifies the presence and quality of security features in labels, packaging, and authentication labels. It helps protect products from counterfeiting and diversion, ensuring consumer confidence and brand protection.
Conclusion
Surface inspection of printed materials is a fundamental aspect of quality control in the printing industry. Advancements in inspection technologies, have significantly enhanced the efficiency and accuracy of surface inspection systems. By detecting and addressing defects early in the production process, these systems help minimize waste, improve productivity, and maintain customer satisfaction.