How to Detect and Categorize Defects in Printed Materials
Whether producing packaging, labels, newspapers, or industrial components, defects can undermine the aesthetics, functionality, and even safety of the final product. Detecting and categorizing defects in printed materials is therefore a critical aspect of quality control, and modern technology offers a range of sophisticated solutions to address this challenge.
The Importance of Quality Assurance of Printed Materials
In industries where printed materials are central to product presentation or functionality, even minor defects can have significant consequences. A smudge on a label may render a product unsellable, a misprinted circuit may compromise electronic devices, and a torn page in a book may diminish its value. As such, comprehensive quality assurance processes are essential to identify and rectify defects in printing industry.
Common Detection Techniques Used to Identify Defects in Printed Materials
1. Visual Inspection
Human Visual Inspection: Trained operators visually inspect printed materials for defects such as misprints, smudges, streaks, color inconsistencies, and registration errors. This method relies on human perception and judgment and is suitable for identifying visible defects.
2. Automated Optical Inspection (AOI)
- High-Resolution Cameras: AOI systems utilize high-resolution cameras to capture detailed images of printed materials.
- Advanced Image Processing Algorithms: Sophisticated algorithms analyze the captured images to detect defects automatically. These algorithms can identify defects based on variations in color, texture, shape, and size.
- Speed and Efficiency: Automated print inspection systems offer rapid defect detection capabilities, enabling high-throughput inspection of printed materials.
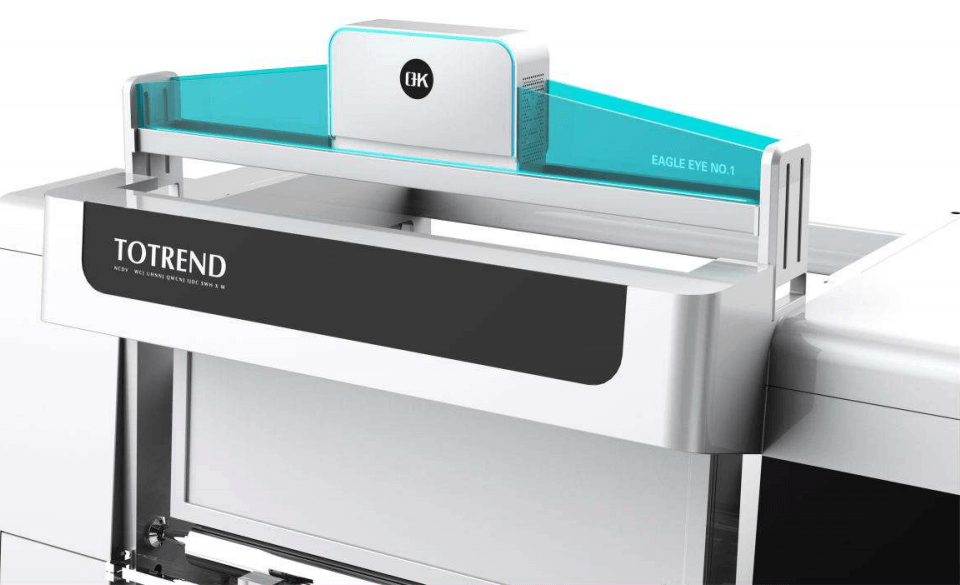
3. Machine Vision Systems
- Cameras and Sensors: Machine vision systems are equipped with cameras and sensors to capture images and collect data on printed materials.
- Image Analysis Software: Image analysis software processes captured images and identifies defects based on predefined criteria. These systems can detect defects such as misprints, color variations, scratches, and missing or incomplete printing.
- Customizable Parameters: Parameters in machine printing inspection vision systems can be customized to detect specific types of defects and adjust sensitivity levels to minimize false positives and negatives.
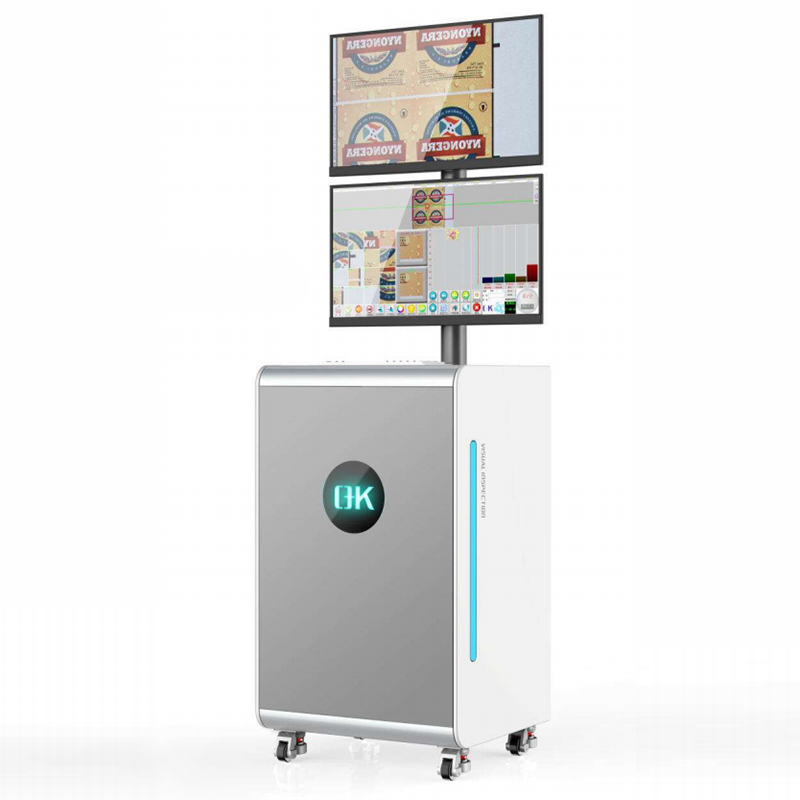
4. UV Inspection
- Ultraviolet (UV) Lighting: UV inspection involves illuminating printed materials with ultraviolet light to reveal defects that may not be visible under normal lighting conditions.
- Fluorescence Detection: Certain defects, such as ink smudges or contaminants, fluoresce under UV light, making them easier to detect. UV inspection can identify defects such as ink splatters, stains, and contamination.
5. Spectrophotometry
- Color Measurement Devices: Spectrophotometers measure the color properties of printed materials, including hue, saturation, and brightness.
- Color Matching: Spectrophotometry is used to ensure color consistency across printed materials and verify that printed colors match specified color standards.
- Detecting Color Inconsistencies: Spectrophotometers can detect color inconsistencies, variations, or mismatches that may indicate printing defects or deviations from quality standards.
6. Dimensional Measurement
- Calipers and Micrometers: Dimensional measurement tools such as calipers and micrometers are used to measure the dimensions of printed materials, including thickness, width, and length.
- Ensuring Accuracy: Dimensional measurement ensures that printed materials meet specified dimensional tolerances and quality requirements.
7. Barcodes and QR Codes Inspection
- Barcode Scanners: Barcode scanners are used to verify the accuracy and readability of barcodes and QR codes printed on packaging, labels, and other materials.
- Verification of Data: Barcode inspection ensures that printed codes contain accurate and legible data, preventing errors in product identification, tracking, and inventory management.
8. Surface Inspection Technologies
- Microscopy: High-resolution microscopy techniques such as optical microscopy, scanning electron microscopy (SEM), and atomic force microscopy (AFM) are used to inspect printed materials at the microscopic level.
- Identifying Surface Defects: Surface inspection technologies can identify defects such as scratches, abrasions, surface roughness, and printing artifacts that may affect the appearance or functionality of printed materials.
Common Categorization Methods used for Printed Materials
1. Defect Type
- Misprints: Errors in printed text, graphics, or images.
- Smudges and Streaks: Ink or toner marks resulting from improper application or substrate contamination.
- Registration Errors: Misalignment of colors or printed elements.
- Color Inconsistencies: Variations in color intensity, hue, or saturation.
- Missing or Incomplete Printing: Portions of the design or text that are missing or improperly reproduced.
- Physical Damage: Tears, creases, wrinkles, or folds in printed materials.
- Surface Imperfections: Blemishes, scratches, or irregularities on the surface of printed materials.
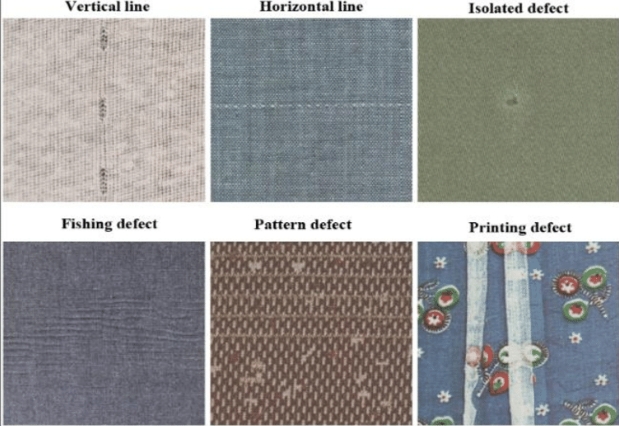
2. Severity Level
- Critical Defects: Defects that significantly impact the usability or functionality of the printed materials.
- Major Defects: Defects that are noticeable and may affect the appearance or quality of the printed materials.
- Minor Defects: Defects that are minor or cosmetic in nature and have minimal impact on the overall quality of the printed materials.
3. Location
- Edge Defects: Defects occurring along the edges of printed materials.
- Center Defects: Defects occurring in the central area of printed materials.
- Border Defects: Defects occurring in specific border areas of printed materials.
- Full-Sheet Defects: Defects affecting the entire surface of printed materials.
4. Frequency
- Isolated Defects: Defects occurring sporadically or in isolated instances.
- Clustered Defects: Defects occurring in clusters or groups within a defined area.
- Widespread Defects: Defects occurring consistently across multiple printed materials or production batches.
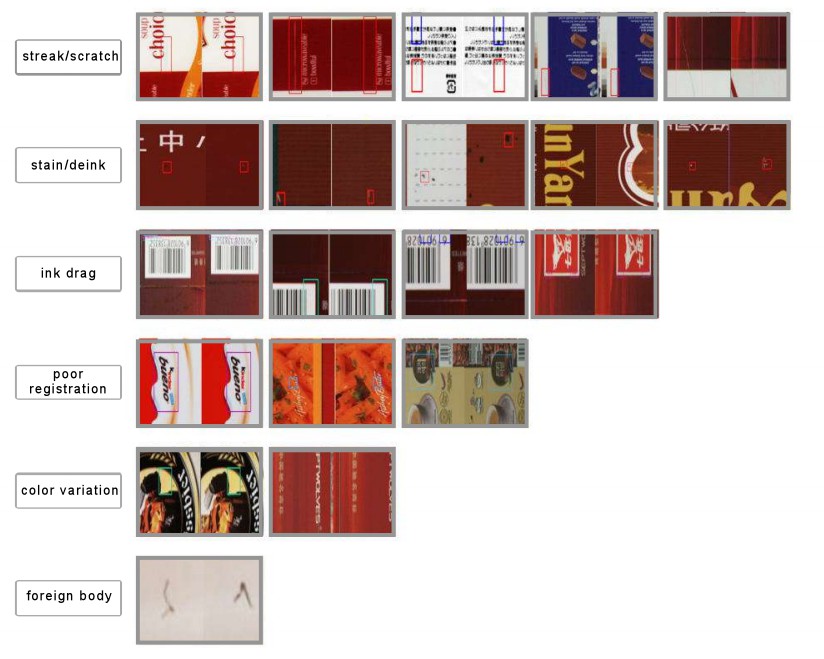
5. Root Cause
- Printing Process Issues: Defects caused by issues with the printing process, such as equipment malfunction, improper settings, or inadequate maintenance.
- Material Defects: Defects caused by defects in the printing substrate, ink, toner, or other materials used in the printing process.
- Handling and Storage Issues: Defects caused by mishandling, improper storage, or transportation damage.
6. Impact on Functionality
- Aesthetic Defects: Defects that primarily affect the appearance or visual appeal of the printed materials.
- Functional Defects: Defects that impact the functionality, readability, or usability of the printed materials.
- Safety Defects: Defects that pose safety hazards or compliance risks.
7. Customer Impact
- Internal Defects: Defects identified during internal quality control processes before the products are shipped to customers.
- External Defects: Defects identified by customers after receiving the printed materials, leading to complaints or returns.
8. Corrective Action Required
- Immediate Action: Defects requiring immediate corrective action to prevent further production of defective materials.
- Rework: Defects that can be corrected through rework or repair processes without scrapping the entire batch of printed materials.
- Process Improvement: Defects that indicate underlying issues with the printing process and require process improvements or adjustments to prevent recurrence.
Technological Advancements in Detecting and Categorizing Defects of Printed Materials
Technological advancements have revolutionized the process of detecting and categorizing defects in printed materials, enhancing accuracy, efficiency, and reliability.

1. Real-Time Monitoring and Feedback Systems
- Continuous Monitoring: Real-time monitoring systems continuously monitor the printing process and detect defects as they occur.
- Immediate Feedback: Detected defects trigger immediate feedback mechanisms, such as alarms or alerts, prompting operators to take corrective actions promptly.
- Data Analytics: Data collected from real-time monitoring systems are analyzed to identify trends, patterns, and root causes of defects, enabling proactive quality management and process optimization.
2. Artificial Intelligence (AI) and Machine Learning
- Advanced Algorithms: AI and machine learning algorithms analyze large datasets of defect images to learn and identify patterns associated with different types of defects.
- Automated Categorization: AI-powered systems automatically categorize defects based on their characteristics, severity, and impact on quality.
- Continuous Improvement: AI algorithms continuously improve over time as they are exposed to more data, leading to enhanced accuracy and efficiency in defect detection and categorization.
3. Remote Inspection Technologies
- Remote Monitoring: Remote inspection technologies enable real-time monitoring of printing processes from remote locations.
- Cloud-Based Solutions: Cloud-based inspection systems store and analyze data remotely, providing accessibility and flexibility for operators and managers.
- Collaborative Tools: Remote inspection technologies facilitate collaboration among team members, allowing for real-time communication and decision-making.
4. Integration with Industry 4.0 and IoT
- Connectivity: Integration with Industry 4.0 and Internet of Things (IoT) technologies enables seamless connectivity between different components of the printing process.
- Data Exchange: IoT-enabled devices exchange data in real-time, providing insights into the printing process and facilitating predictive maintenance and optimization.
- Smart Manufacturing: Industry 4.0 technologies enable smart manufacturing practices, including automated defect detection, predictive analytics, and adaptive control, leading to improved efficiency and quality in printing operations.
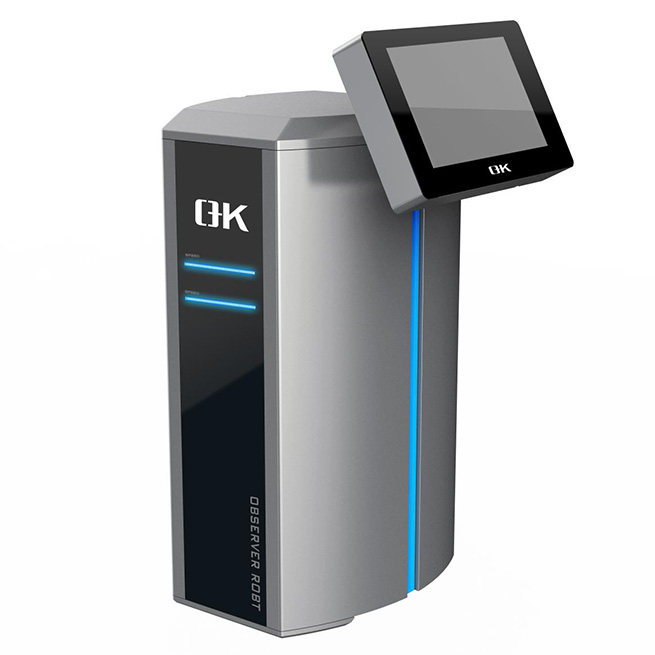
Conclusion
Detecting and categorizing defects in printed materials is a critical aspect of quality assurance in printing processes. By leveraging advanced inspection technologies and automated systems, printers can ensure that their products meet stringent quality standards, minimize waste, and maintain customer satisfaction. Continuous improvement supported by technology advancements, and collaboration, further enhance the effectiveness of defect detection and categorization processes, ultimately contributing to the success of printing operations.