Integration of Machine Learning for Defect Classification in Printing Inspection
In the high-speed, precision-driven printing industry, defect classification is essential to maintain the quality of products. Traditional Print inspection systems typically use rule-based algorithms, as well as manual oversight that can be limiting in terms of speed, accuracy, and scale. The introduction of technology known as machine learning into the printing inspection systems is changing the way we inspect print which allows for faster, more intelligent and more flexible detection of defects.
Table of Contents
The Challenge of Traditional Defect Detection in the Printing Industry
Challenge | Description | Impact on Inspection |
Human Error | The manual inspection process is subjective and susceptible to inconsistency and fatigue | Missed defects, false positives, variable quality |
Limited Speed | Manual checks can slow production, particularly at large volumes | Increased costs, reduced throughput |
Fixed Rule-Based Systems | Rely upon predefined thresholds and basic algorithms that can’t change. | The inability to detect complex or novel defect types |
Sensitivity to Environmental Factors | Modifications to the lighting, substrates or ink could alter the accuracy of detection | Rates of false alarms high or unnoticed flaws |
Difficulty in Detecting Subtle Defects | Tiny color shifts, small irregularities, or even faint marks are difficult to recognize. | Quality control gaps, inconsistent product quality |
Inflexibility and Scalability | Traditional methods call for manual reprogramming or retraining to accommodate new defect types. | A lot of maintenance, not scaleable |
Lack of Data-Driven Insights | It is not possible to evaluate defects or provide feedback on process improvement | Untapped opportunities to optimize printing processes |
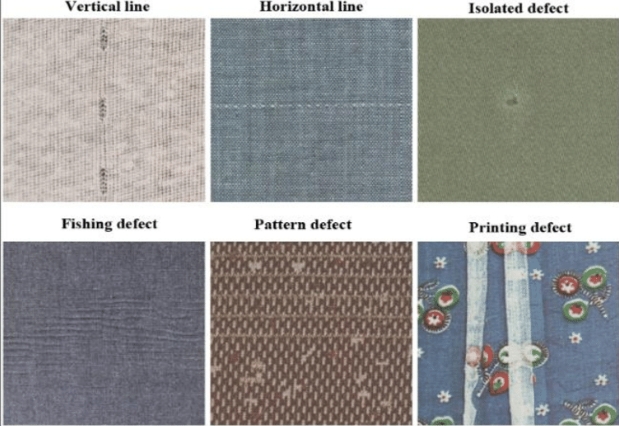
How Machine Learning Enhances Defect Classification for Printing Inspection
Machine learning offers a powerful alternative by enabling automated, accurate, and adaptive defect classification in printing inspection.
1. Learning from data, not Rules
Contrary to conventional methods that rely on a set of thresholds or hand-crafted elements, machine learning models learn directly from the data. By gaining experience from thousands of photos of printed material, both with and with no defects, machine-learning algorithms can identify intricate visual patterns that indicate imperfections. This ability to understand subtle differences make the machine learning system more tolerant to the effects of changes in light, substrate ink types, as well as printing conditions.
2. Handling Complex and Subtle Defects
Certain defects are not obvious or can appear in various appearances based on the print run or the material. Machine learning models, particularly ones based on deep learning, such as convolutional neural networks (CNNs) excel at detecting these difficult-to-find defects. They are able to distinguish between variations in machine-learning and real flaws that require more attention. This greatly reduces the number of false alarms and missed defects.
3. Real-Time and Scalable Inspection
With advances in computer hardware, machine learning-powered 100% printing inspection systems are able to analyze images in real-time, enabling high-speed printing. This flexibility allows manufacturers to ensure strict quality control without slowing production and raising labor costs.
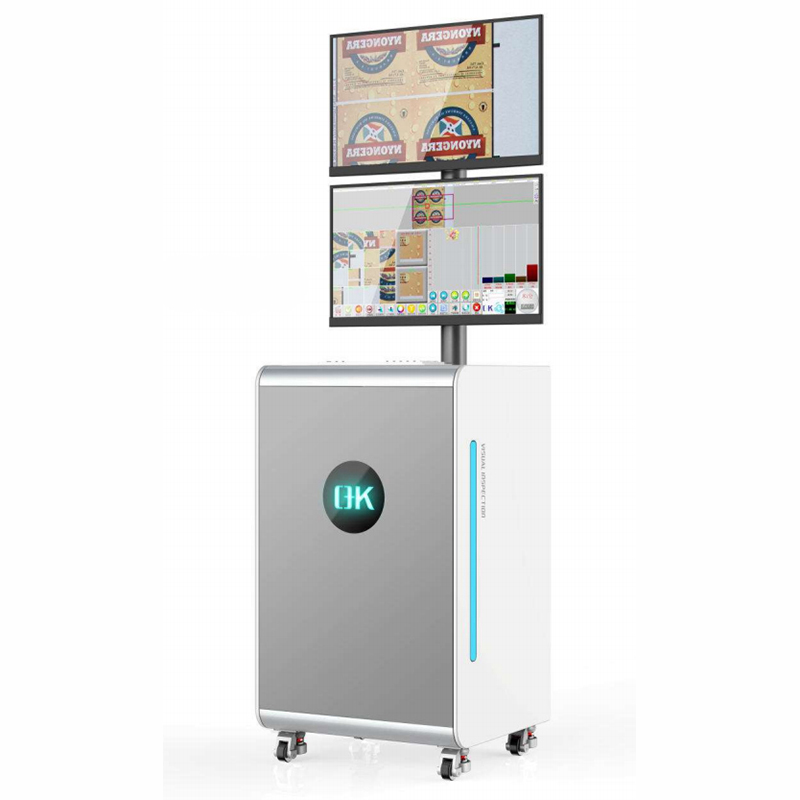
4. Continuous Improvement Over Time
Machine learning models are improved when they process more data. Through regular updating and retraining with new defects They are able to adapt to the changing processes of printing as well as new types of defects and changes in environmental conditions. Continuous learning assures long-term accuracy and resiliency.
5. Integration and Benefits
In conjunction with high-resolution cameras as well as automated sorting systems, machine learning used to classify defects improves overall effectiveness. It decreases the dependence on human inspectors, reduces the amount of waste produced, and guarantees consistency in quality. Additionally, the data gathered during inspections will provide valuable information to improve process efficiency as well as preventive maintenance.
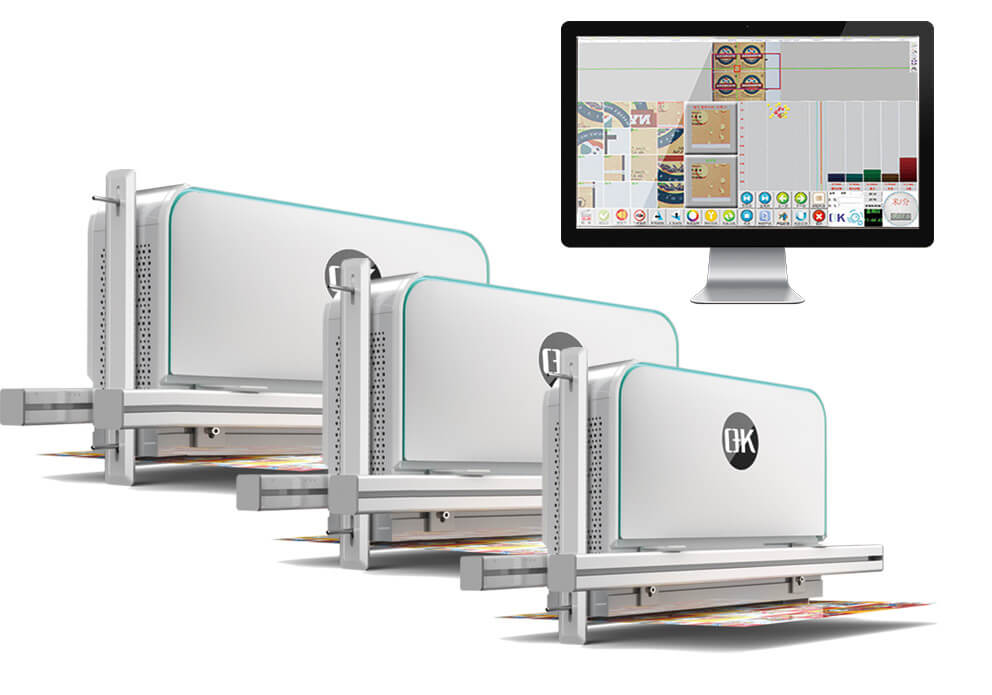
Common Printing Defects Can Be Easily Recognized by Machine Learning
Printing Defect | Description | How Machine Learning Helps |
Ink Bleed or Smudging | Ink that is spread beyond the intended regions | The system detects subtle differences and irregularities in patterns |
Color Inconsistency | Color distribution that is not even or correct | It can detect subtle color shifts that go beyond the thresholds that are fixed. |
Misregistration | Colors or images that aren’t aligned properly | Finds spatial shifts as well as complex alignment error |
Missing Text or Graphics | Images or textual elements are missing or insufficient | Finds incomplete or partial prints with precision |
Barcode or QR Code Errors | Machine-readable codes are affected by a number of bugs. | Classifies defects affecting code readability |
Surface Contaminations | Dust, foreign particles, or stains on prints | It differentiates print contaminations from the intended marks |
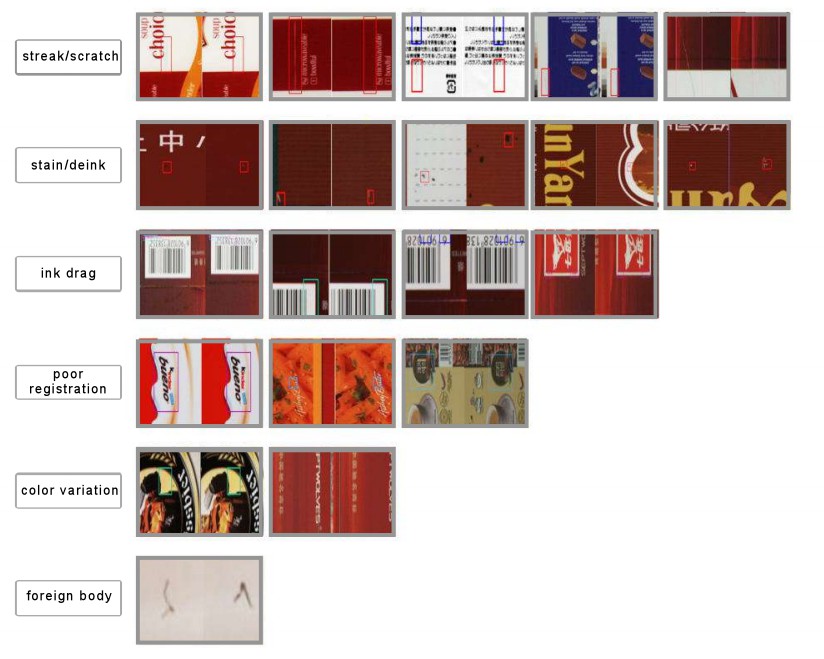
Practical Applications of Machine Learning Defect Classification in Printing Inspection
- Real-Time Quality Control During Printing: Machine learning allows for immediate detection and classification of any defects that occur when printing at high speed, allowing for rapid identification and correction, without stopping production.
- Automated Sorting and Defect Rejection: By correctly identifying imperfections, machine learning systems can automatize the process of sorting and separate bad prints from those that are acceptable and reduce the manual work.
- Process Optimization Through Defect Analysis: Information gathered from machines learning inspection systems can help determine patterns and reasons for defects and allows manufacturers to adjust printing parameters and decrease mistakes.
- Adaptive Inspection for Emerging Defect Types: Machine learning models are able to be retrained using new data to identify previously undiscovered types of defects while ensuring high quality inspection accuracy regardless of changes in the printing conditions.
- Compliance and Traceability Reporting: Machine learning-powered inspection tools create detailed defect logs and reports, helping to ensure compliance with regulations and providing an audit trail for quality assurance.
- Reducing Waste and Improving Sustainability: Accurate defect classification can reduce the chance of false positives as well as unnecessary printing, which reduces the amount of waste produced and promoting sustainable manufacturing methods.
- Enhancing Customer Satisfaction and Brand Reputation: The constant detection of any defects makes sure that only the highest-quality products are available to customers, thereby increasing brand credibility and gaining trust from customers.
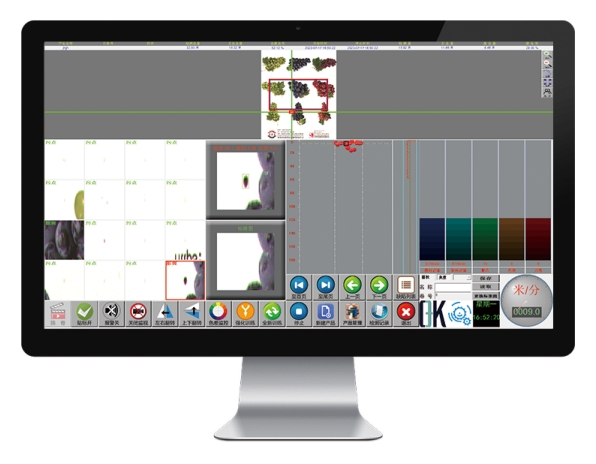
Key Considerations for the Successful Integration of Machine Learning in Printing Inspection
- High-Quality Data Acquisition: A precise defect classification process begins by the ability to capture clear, consistent images. The proper lighting cameras, high-resolution lighting, and solid imaging setups are vital to supply an algorithm for machine learning with high-quality data.
- Comprehensive and Diverse Training Data: The precision of a machine learning model is largely dependent upon the high-quality and variety of the training data. The data set should contain an array of defect types, printing substrate colours, as well as conditions for the environment to ensure that it is robust.
- Effective Model Selection and Training: Selecting the best machine learning algorithm – typically deep learning models, such as convolutional neural networks (CNNs)–is crucial. These models need to be properly tested, trained, and refined to ensure accuracy and sensitivity in the detection of defects.
- Real-Time Processing Capabilities: To keep pace with fast printing, the machine-learning web inspection system for printing must support the processing of images in real time and classification. This requires high-quality hardware and software that is optimized.
- Seamless Integration with Production Systems: Machine learning inspections is a must to be integrated into the existing control and production systems to enable automatic defect handling, reports and corrective actions without affecting processes.
- Continuous Learning and Adaptation: The conditions for printing and the types of defects change as time passes. A system that is successful should allow continuous model updates and training by using the latest inspection data to ensure efficiency.
- User-Friendly Interfaces and Monitoring Tools: Operators require intuitive dashboards that allow them to analyze the inspection results, alter parameters and intervene if required. A clear visualization and report aid in the ability to make decisions.
- Robustness to Environmental Variability: A machine-learning system needs to deal with changes in the lighting or texture of the substrate, as well as ink type, and other environmental variables to prevent false positives and negatives.
- Data Security and Privacy: Make sure that the data that is processed and stored during inspection conforms to the privacy and security standards for data particularly if cloud-based services are utilized.
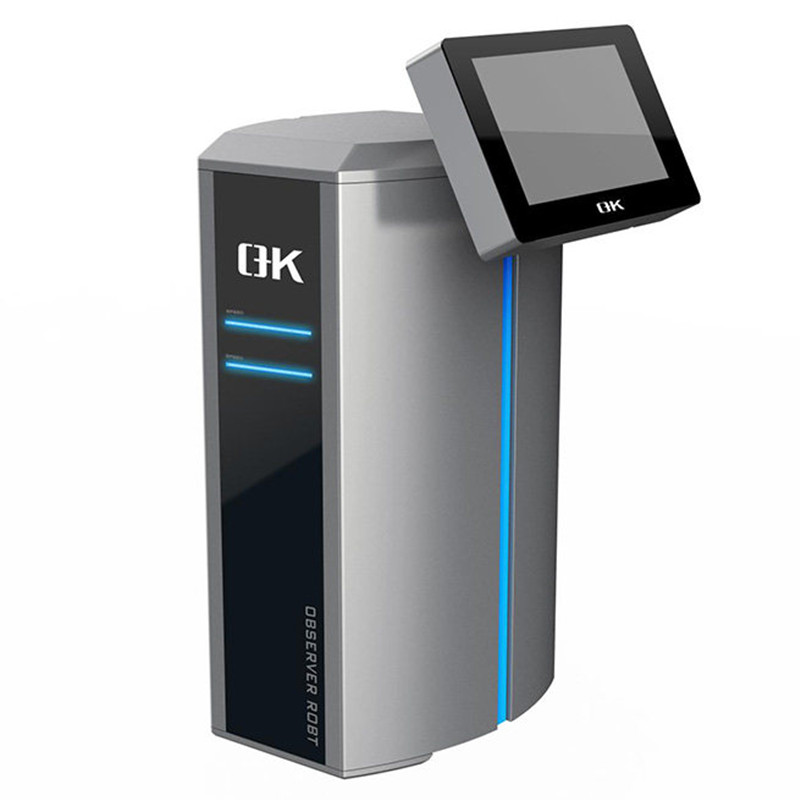
Summary
The integration of machine learning into printing inspection transforms the process of defect classification from a strict rule-based procedure into a flexible, intelligent system. It greatly improves the accuracy of defect detection and reduces operating costs, allowing for continuous print quality improvement.