Print Inspection for Digital vs. Offset Printing
Whether the output is produced through digital or offset printing, print inspection processes are essential in ensuring that the final product meets design specifications, color accuracy and consistency standards. Although both printing inspection methods share the common goal of delivering high-quality prints, the approach to print inspection can vary significantly based on the technology used.
Table of Contents
Understanding Digital and Offset Printing
Digital printing and offset printing are two widely used techniques in the printing industry, each suited to different production needs. Digital printing involves transferring digital files directly to the printer, making it ideal for short runs, fast turnaround, and variable data printing such as personalized materials.
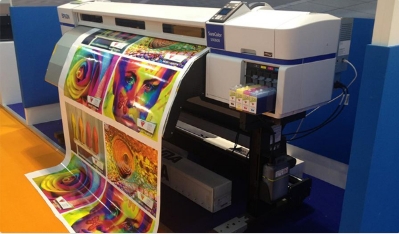
Offset printing, on the other hand, uses plates to transfer ink onto paper and is best suited for high-volume jobs due to its consistent quality and cost-effectiveness over large print runs. Understanding the differences between these methods helps in selecting the right approach for specific printing applications.
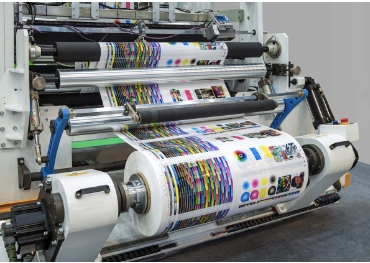
Print Inspection Methods in Digital Printing
This streamlined process of digital printing reduces preparation time but introduces new print inspection challenges that require specialized methods to ensure consistent print quality.
1. Automated Vision Systems for On-the-Fly Monitoring
One of the most effective inspection tools in digital printing is the use of automated vision systems. These web inspection vision systems for printing quality, employ high-resolution cameras that monitor every sheet in real-time during the print run. They detect defects such as:
- Banding or streaking due to printhead issues
- Color deviations from the expected standard
- Pixelation or missing content caused by data corruption
- Artifacts from substrate irregularities
Unlike manual checks, automated systems can inspect 100% of the output, providing higher accuracy and faster error detection. These systems are often integrated into the printer itself or positioned along the output path.
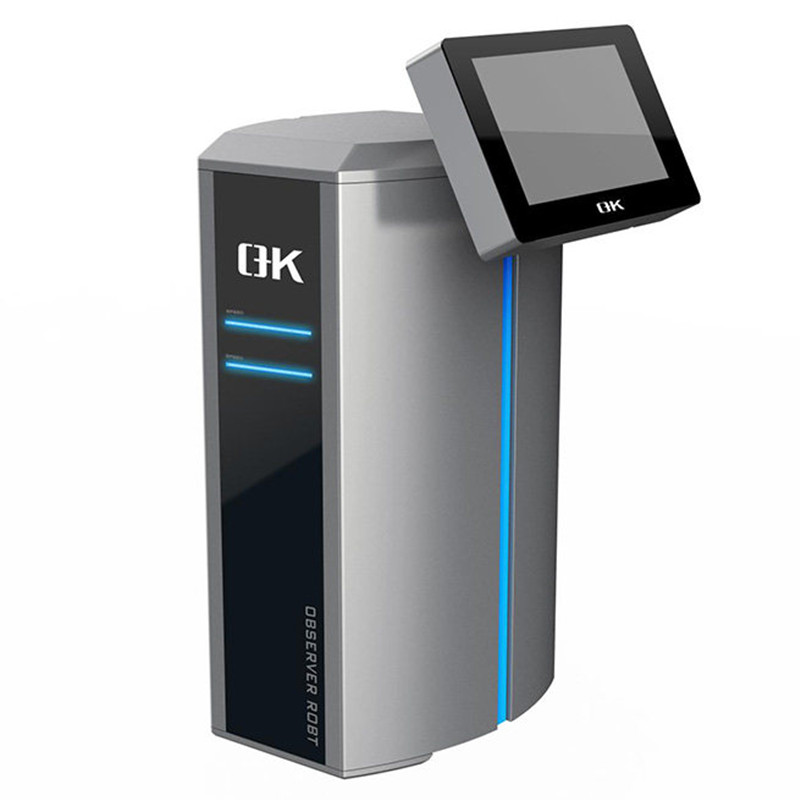
2. Color Calibration and Profiling Tools
Color consistency is a critical concern in digital printing, especially when matching brand standards or reproducing high-end images. Spectrophotometers and colorimeters are commonly used to calibrate printers and verify that colors remain within defined tolerances. Software tools help maintain consistent output across jobs and machines by generating and managing ICC profiles tailored to specific substrates and inks.
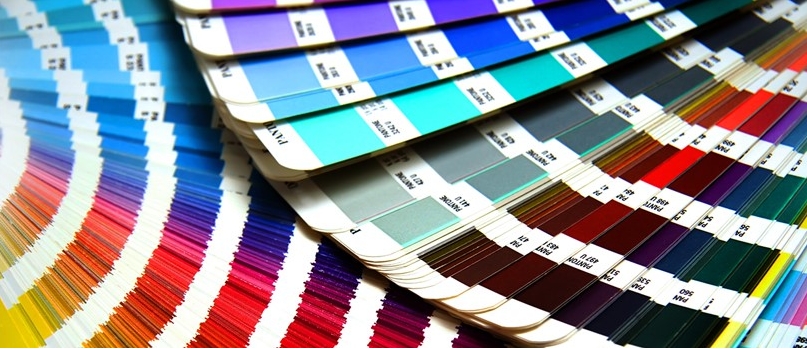
3. Digital Pre-Flight Inspection
Before printing begins, a digital “pre-flight” inspection ensures that the digital files are print-ready. This involves checking for font issues, image resolution problems, missing links, or improper color space definitions (e.g., RGB instead of CMYK). Pre-flight tools help avoid errors that could otherwise appear only after printing has started, saving time and materials.
4. Variable Data Verification
One of digital printing’s key strengths is its ability to handle variable data printing (VDP), where each printed piece can be unique (e.g., personalized mailers, packaging, or labels). Inspection systems equipped with OCR (Optical Character Recognition) or barcode readers verify that variable information is printed correctly and in the right sequence. This is especially vital in applications involving sensitive information or regulated industries like pharmaceuticals and finance.
5. Printhead and Nozzle Check Systems
Digital printing relies on precise inkjet or toner deposition, and any malfunction in printheads can lead to visible quality issues. Built-in nozzle check systems regularly test for clogged or misfiring nozzles. Some printers can automatically compensate for problematic nozzles by redirecting ink output or alerting the operator for cleaning or replacement.
6. Post-Print Inspection for Finishing Processes
After printing, post-process inspection checks are conducted to ensure that finishing processes like cutting, folding, or binding do not compromise the integrity of the printed product. Vision systems and manual sampling may be used to confirm accurate alignment and completeness of each printed unit, especially in high-value or precision-demanding projects.
7. Integration with Quality Management Software
Modern digital printers are often linked with quality management systems (QMS) that collect and analyze inspection data. These systems provide detailed reports and real-time dashboards, enabling operators to track trends and take proactive action. Integration with cloud platforms also allows remote monitoring and centralized control across multiple sites.
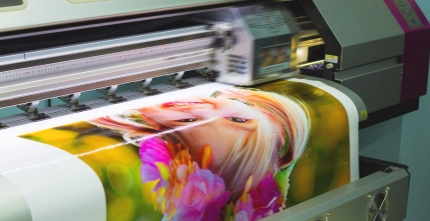
Print Inspection Methods in Offset Printing
Various methods are employed at different stages of the print inspection process for offset printing to maintain quality and minimize defects.
1. Pre-Press Quality Checks
Before any ink hits the paper, inspection begins with careful pre-press preparation. This stage involves verifying that printing plates are correctly imaged, aligned, and free of imperfections. Calibration of color profiles and ink distribution settings is also essential, as it sets the tone for the entire print job.
2. Manual Inspection by Skilled Operators
Press operators play a fundamental role in quality control. Through visual inspection, they monitor the first few sheets and periodically check output during the run. Their trained eyes can detect common defects such as ghosting, ink smudging, registration errors, and uneven inking—issues that may not always be caught by machines.
3. Inline Camera-Based Inspection Systems
Modern offset presses increasingly rely on high-speed cameras integrated into the production line. These inline inspection systems compare each sheet against a digital reference, scanning for defects such as:
- Color variation
- Misregistration between plates
- Missing print elements
- Streaks, blotches, or hickeys
When a defect is detected, the printing inspection system can alert the operator or even pause the press automatically, allowing for immediate correction.
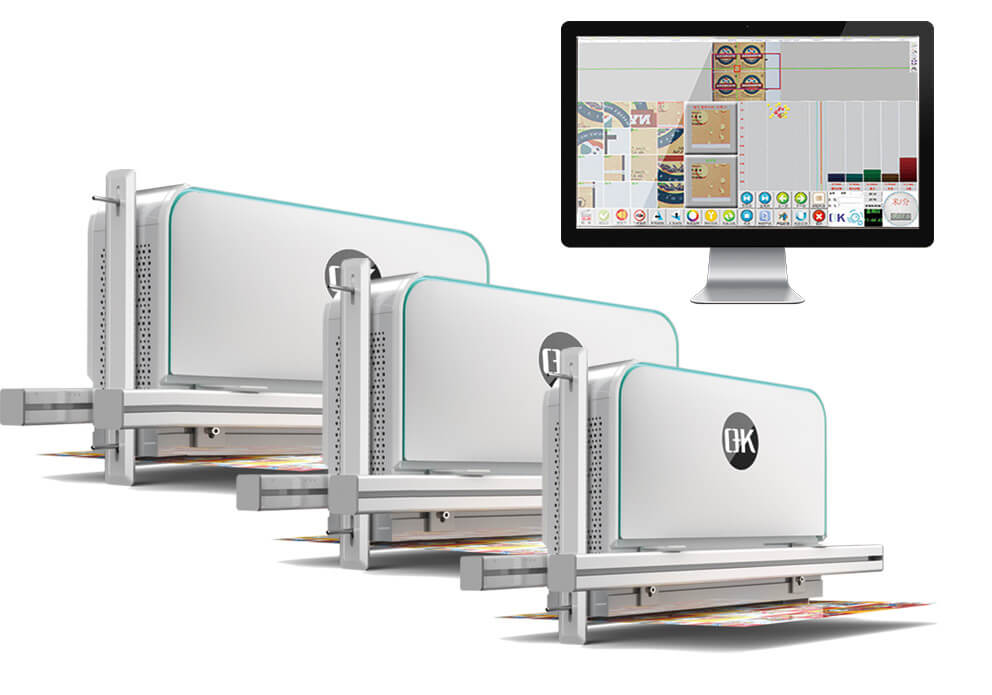
4. Color Monitoring with Spectrophotometers and Densitometers
Maintaining color consistency throughout a print run is critical. Spectrophotometers are used to measure the precise color values on printed sheets, ensuring they fall within specified tolerances. Densitometers, meanwhile, assess ink density levels, helping operators fine-tune ink distribution for uniform results.
5. Registration Control Systems
Since offset printing uses multiple plates for different colors, registration accuracy is crucial. Automated registration control systems continuously monitor alignment between the plates and make real-time adjustments. This ensures sharp and properly aligned images without color fringing or blurring.
6. Post-Press and Finishing Line Inspection
Quality control doesn’t stop once printing is complete. In the post-press phase—especially for packaging, security documents, or labels, inspection may include barcode verification, inspection of perforations, and lamination quality checks. Vision systems on finishing lines ensure the integrity of the final product before delivery.
7. Advances in Smart Inspection Technologies
With digital transformation influencing even traditional processes like offset printing, smart technologies are reshaping inspection workflows. AI-powered systems analyze patterns and trends in defects, improving predictive maintenance and overall quality control. Cloud-connected quality management software allows centralized oversight across multiple machines and facilities.
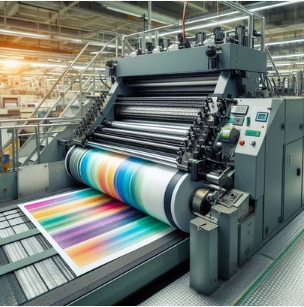
Comparing Print Inspection Methods Between Digital vs. Offset Printing
Aspect | Digital Printing | Offset Printing |
Inspection Focus | Real-time defect detection, variable data accuracy, printhead functionality | Color consistency, registration, plate alignment, defect detection |
Pre-Press Checks | Digital file pre-flight (fonts, resolution, color space) | Plate inspection, ink calibration, color separation checks |
Inline Inspection Tools | High-speed cameras, AI-assisted vision systems for every sheet | Vision systems for periodic sampling or full-sheet inspection |
Color Management | ICC profiling, spectrophotometry, automated color calibration | Densitometry, spectrophotometry, ink density adjustments |
Defect Types Detected | Banding, streaking, variable data errors, misprints | Ghosting, misregistration, hickeys, ink smudges |
Variable Data Handling | OCR, barcode verification, image/text match per item | Not commonly used; static image control |
Printhead Monitoring | Nozzle check systems, auto-cleaning routines | Not applicable (uses plates and rollers instead of inkjets) |
Post-Print Inspection | Finishing accuracy, personalized content validation | Final sheet checks for color alignment, cutting accuracy |
Human vs. Automated Inspection | Mostly automated, minimal human intervention | Combination of manual operator inspection and automated systems |
Data Integration | Cloud-based QMS, real-time alerts, detailed defect logs | Local data tracking, increasingly moving toward digital integration |
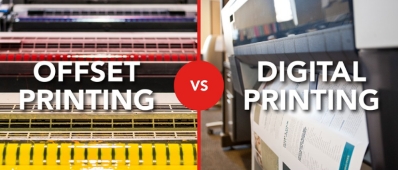
Choosing the Right Print Inspection Methods for Digital and Offset Printing
Whether operating a digital or offset press, the choice of inspection methods directly impacts production efficiency, defect detection, and customer satisfaction. However, the ideal approach varies between digital and offset environments due to their differing technologies and outputs. To choose the right print inspection method, several key factors must be carefully evaluated.
- Nature of the Printing Technology
The first major consideration is the fundamental difference between digital and offset printing. Digital printing operates through a data-driven process, where images are directly transferred from a computer to the substrate without physical plates. Offset printing, on the other hand, relies on plate-based image transfer and offers advantages for large-volume runs. This distinction affects the type of errors likely to occur—digital systems may experience issues like banding or variable data mismatches, whereas offset is prone to ink misregistration and plate defects.
- Type and Frequency of Defects
Understanding which defects are most prevalent in your printing process is crucial. In digital printing, nozzle clogging, inkjet banding, and issues with variable data are common. Therefore, high-speed vision systems and OCR tools are often necessary. In offset printing, problems such as ghosting, hickeys, and misregistration demand densitometers, manual checks, and periodic sampling methods to catch inconsistencies caused by mechanical wear or plate problems.
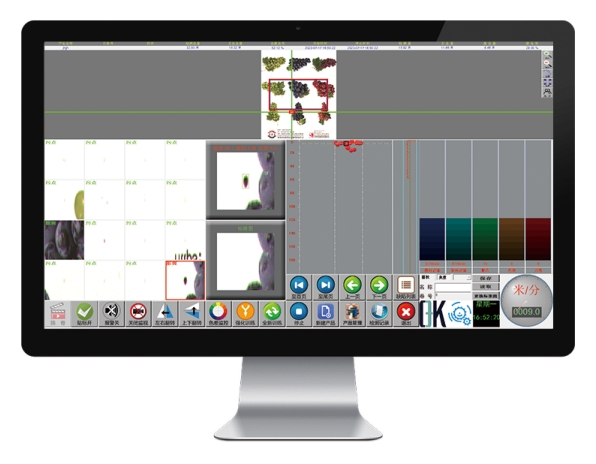
- Print Volume and Production Speed
The volume of prints and speed of production influence the level of automation needed in inspection. For high-speed digital operations producing personalized items, inline automated inspection with real-time error rejection becomes essential. Offset operations, while fast, are often optimized for long, uniform print runs, where periodic inspection using both manual and semi-automated tools might suffice, unless 100% printing quality control is required.
- Color Accuracy and Consistency Needs
Color consistency is a concern in both methods, but each requires different tools. Digital printers benefit from software-controlled ICC profiling and spectrophotometers to maintain output fidelity. Offset printing requires densitometers to measure ink density, along with manual or automated adjustments on the press. The level of control required by your application—such as brand color integrity—will guide the sophistication of the tools needed.
- Variable Data Requirements
If your print job involves variable data printing (e.g., unique QR codes or personalized text), digital inspection systems equipped with barcode scanners and text recognition software are non-negotiable. These ensure that each piece is accurate and in sequence. Offset printing is typically not used for variable data unless paired with digital overprinting, which introduces hybrid inspection needs.
- Budget and ROI Considerations
The cost of inspection technology must be weighed against the potential for waste reduction, customer satisfaction, and rework prevention. Digital inspection tools tend to be more expensive upfront but are necessary for avoiding costly errors in short runs or sensitive applications. Offset inspection solutions may be less costly, but ongoing maintenance and human oversight can add operational expenses over time.
- Integration with Workflow and Reporting Systems
A modern print environment often integrates 100% print inspection systems into a broader workflow and quality management system. Digital inspection systems with cloud integration, real-time defect reporting, and automated feedback loops can significantly enhance operational efficiency. Offset workflows benefit from centralized data logging and trend analysis to track press performance over time.
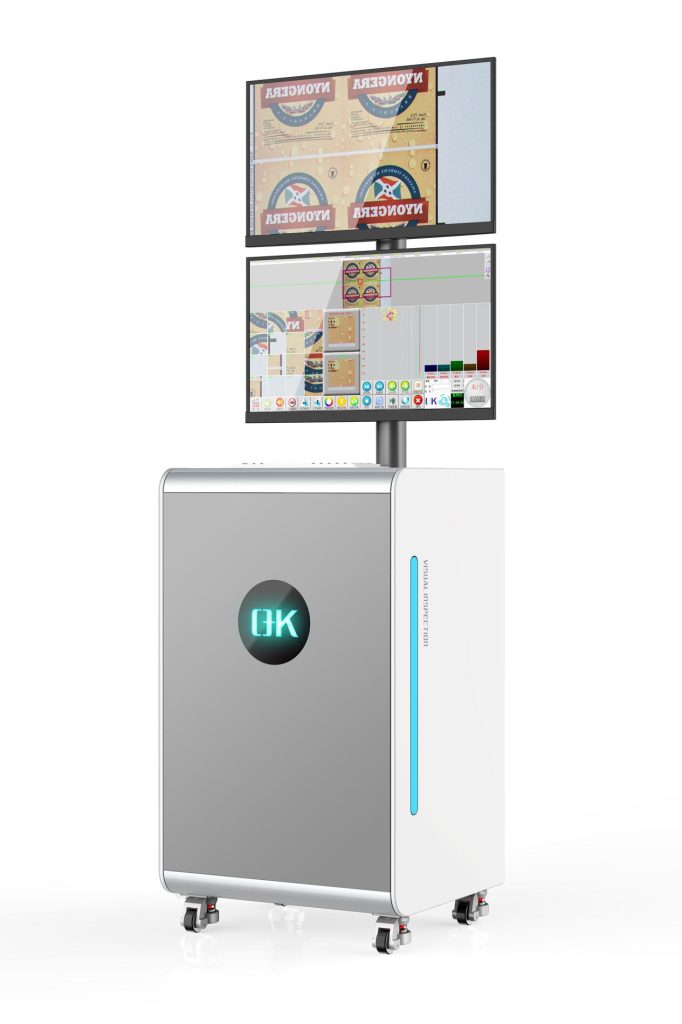
Final Thoughts
Whether in digital or offset printing, effective inspection is fundamental to delivering reliable, high-quality printed materials. Each method has unique print inspection priorities: offset printing values consistency and color accuracy over long runs, while digital printing demands flexibility and precision for variable data and rapid jobs. Understanding these differences is key to implementing the right printing inspection methods and maintaining customer satisfaction in an increasingly competitive print market.