What are the Trends in the Manufacturing of Web Guide Systems
Web guide systems are created in order to make sure it is guaranteed that they ensure that the “web” remains aligned as it progresses through the various stages of production. In the current fast-paced globalized and interconnected world, web guiding system manufacturers have developed rapidly to meet the needs of more advanced as well as automated manufacturing environments.
Table of Contents
What is a Web Guide System
Web guide systems are composed of controllers, sensors, actuators, and mechanical parts that are used to regulate the lateral movement of a moving web material as it is processed. The aim of this system is to keep the proper alignment of the material throughout the different stages of production, keeping it from drifting off course and making sure it’s properly aligned for the next stage of processing, such as coating, printing or cutting.

There are two kinds of web guide systems:
- Edge Web Guiding Systems: These systems track and adjust the position of the web’s edge.
- Center Web Guiding Systems: These systems manage the web in the middle of the line.
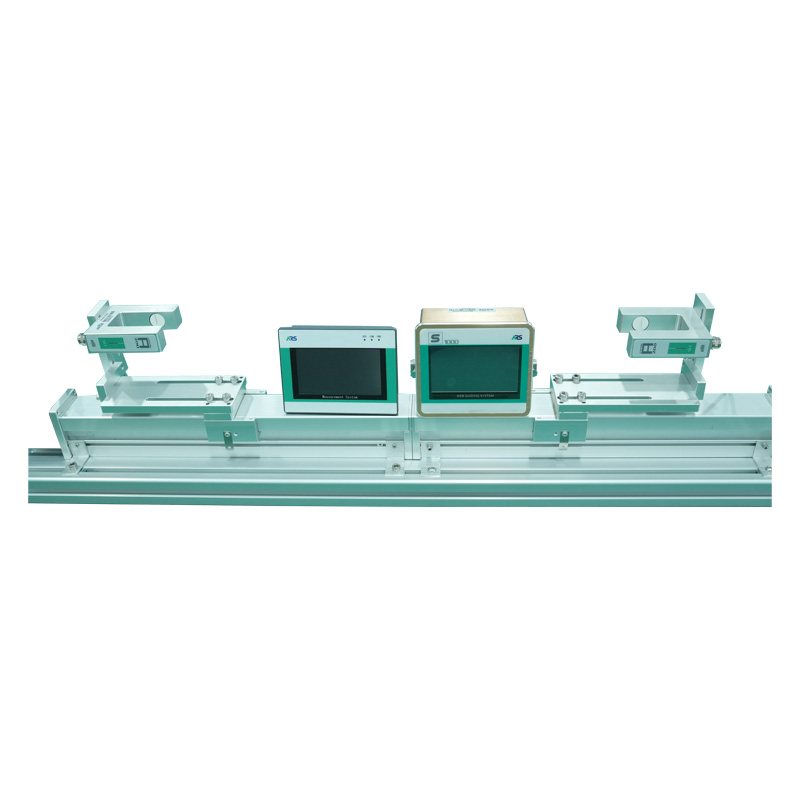
The Manufacturing Process of Web Guide Systems
Here’s a simple chart that outlines the manufacturing process for web guide systems.
Step | Description |
1. Design & Engineering | System requirements are determined according to the application (e.g. edge guidance or center guide). Engineers plan the design of sensors and actuators, controllers, and housings. |
2. Component Selection | Selection of key parts such as ultrasonic/infrared/CCD sensors, microprocessors, and touch panel interfaces. |
3. Prototyping & Testing | Initial prototypes are constructed and tested for accuracy as well as responsiveness and durability in industrial environments. |
4. Mechanical Fabrication | Housings as well as brackets and mechanical frames are manufactured using CNC machine and metal stamping or casting. |
5. Electronics Assembly | Controller circuit boards are constructed and programmed. sensors and actuators are connected and wired. |
6. System Integration | All electronic and mechanical components are merged to form a complete web guide unit. Software and firmware are loaded. |
7. Quality Assurance Testing | The complete system goes through precision alignment as well as vibration resistance and testing for environmental conditions (e.g., dust or heat). |
8. Calibration | Axioms and sensors can be calibrated to particular material widths and speeds as well as specific sensitivity requirements. |
9. Packaging | Systems are packed with protective material and documentation ready for shipping. |
10. Shipping & Installation | The final products are delivered. The option of installation on-site as well as customer instruction is offered. |
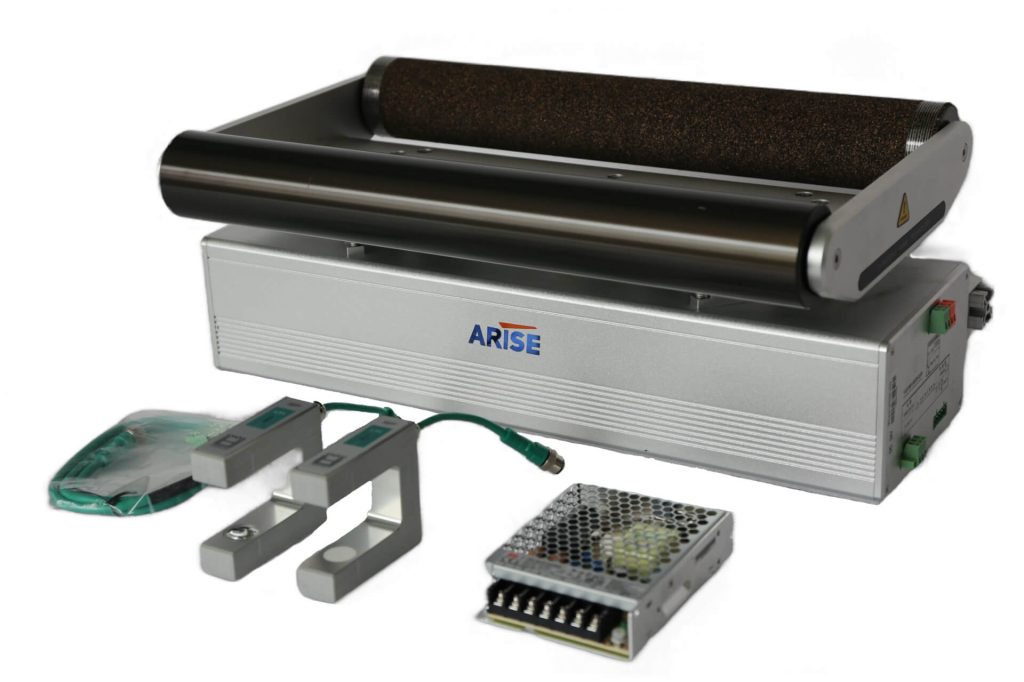
Global Trends Shaping the Manufacturing of Web Guide Systems
1. Integration with Industry 4.0
One of the most important worldwide trends in the manufacture of web guide systems involves their integration into Industry 4.0 technology. The sector is witnessing the growth of intelligent manufacturing solutions, which connect production and equipment lines to central control systems. Web guide systems aren’t an exception. Web guide systems of the present come with sensors that can collect data, as well as IoT (Internet of Things) capabilities that permit live monitoring as well as remote diagnosis.
Manufacturers are focused on creating systems that integrate seamlessly into automated environments, providing options like automated maintenance and remote problem-solving and data-driven optimization of performance. These innovations help decrease the amount of downtime and increase the overall efficiency of operations.
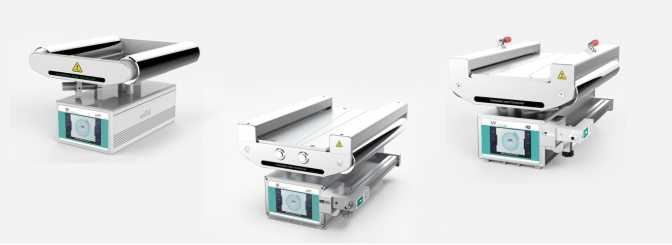
2. Enhanced Accuracy and Precision
Precision has always been the foundation in web guides, however recent advances have elevated precision to a new level. The increasing demand for top-quality production outputs across different industries, including high-resolution printing and thin film processing, packaging and more — has driven manufacturers to further innovate.
Web guide system manufacturers have been incorporating sophisticated sensors, such as lasers and CCD (charge-coupled device) cameras, as well as infrared technology. These sensors can provide better precision of alignment, which ensures that the website is always center, even in high-volume, high-speed operations. This level of accuracy can help to minimize mistakes, cut down on waste of materials, and enhance the process of handling materials.
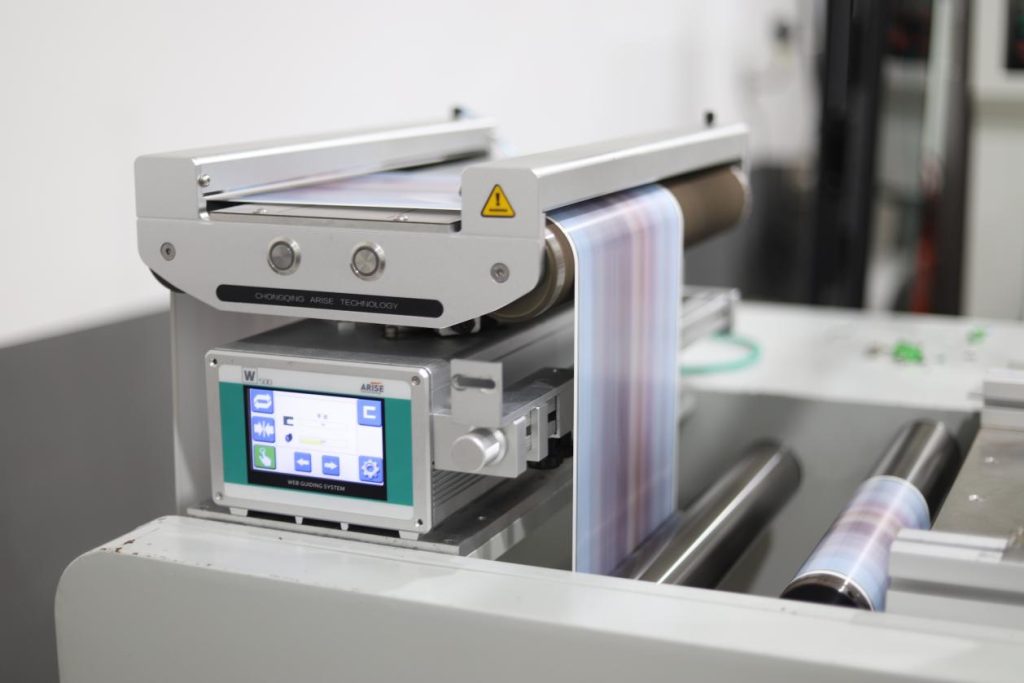
3. Demand for Customization and Flexibility
Each production environment is different and this has resulted in the demand for more customized web guides. Manufacturers have now developed customized web guiding solutions to meet the particular demands of various industries. It doesn’t matter if it’s a different material type, speed of production or a guiding device (edge or central guiding) Web guide system manufacturers are more and more capable of designing products that are tailored to the needs of specific customers.
This trend is most prevalent in industries that require special manufacturing processes, including production of electronics (where delicate materials such as film and substrates are employed) and textile production and manufacturing of batteries. Manufacturers are now focusing on developing modular systems which can be easily modified or upgraded to give customers the ability to grow and change to meet their changing needs.
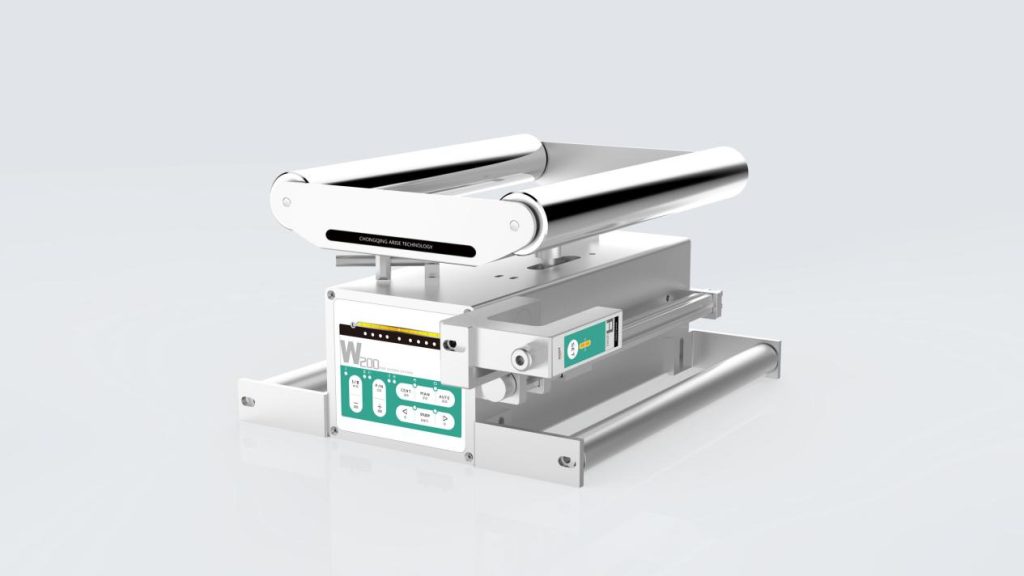
4. Automation and Increased Production Speed
The manufacturing industry in the world is pushing for increased production speeds, which has directly impacted guides for web sites. In the end, there is a growing need for automated systems that operate at greater speeds, without compromising the accuracy or reliability.
Web guide systems are now equipped with high-speed web guiding controllers and actuators which can make adjustments in real-time to the alignment of materials, even at the highest operating speeds. These advances enable manufacturers to respond to the ever-growing needs of the fast-paced industries such as printing, packaging and automotive where speed and precision are vital.
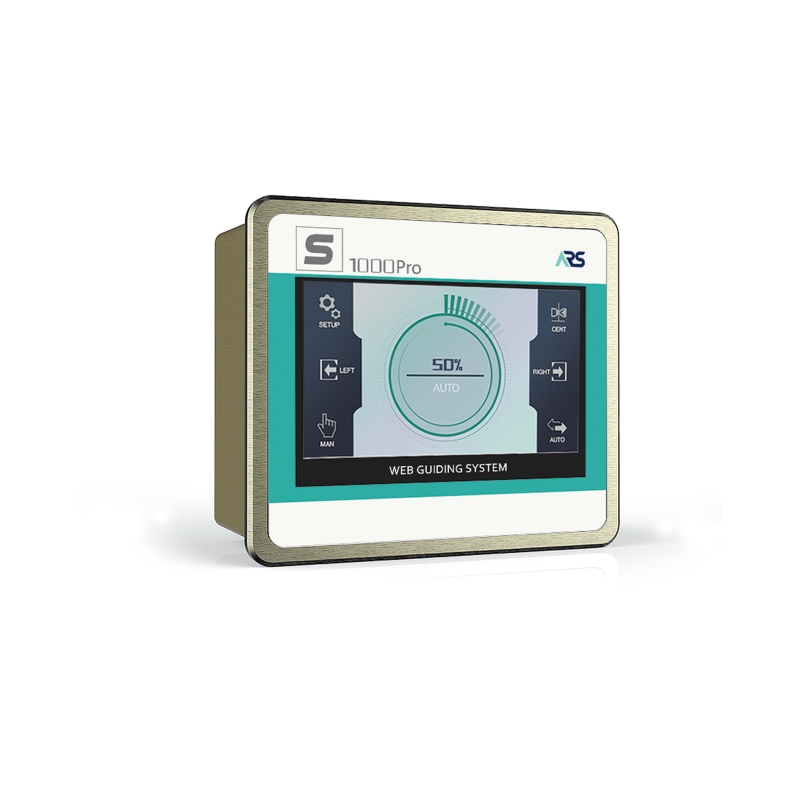
5. Energy Efficiency and Sustainability
As businesses across the world are moving towards sustainable practices, there’s increasing emphasis on the development of eco-friendly and energy-efficient web guide systems. The systems aim to cut down on the use of energy and reduce materials waste as well as to reduce waste. Both are vital to sustainable manufacturing.
Manufacturers are working on developing environmentally friendly and low-power components for web guide systems. For example, energy efficient actuators and sensors can help to reduce the power consumption of the systems. In addition, precision alignment helps reduce the amount of waste that is generated, which increases productivity but also minimizes impacts on the environment of production processes.
6. Globalization and Regional Adaptation
As supply chains around the world are becoming more interconnected, web guide system makers are expanding their operations across various regions. The demand of localized service, quick service and installation assistance has prompted the establishment of distribution centers and service networks around the world.
Manufacturers are also tailoring their solutions to meet requirements of regulatory and operational compliance for diverse regions. For instance, the systems that are sold within North America or Europe may be designed to conform to different standards for safety and environmental regulations than the ones offered to customers in Asia as well as those in Asia or the Middle East. This trend of adapting regionally guarantees that web guides are able to be effectively implemented across various production environments, and are in line with local regulations.
7. Advancements in User Interface and Control Systems
Another major development in web guide manufacturing is the development in user interfaces (UIs) as well as control and monitoring systems. As processes in manufacturing become more complicated and automated, the operators require user-friendly and intuitive control interfaces in order to operate the system efficiently.
Manufacturers are now incorporating touchscreen panels and mobile device compatibility and cloud-based control into their online guide systems. The new features allow users to check performance, alter settings, and get alerts via their mobile devices or computers giving them more control and ease of use. In addition, companies are using AI-based predictive algorithms to aid in decision-making and to further streamline operations.
8. Adoption of Advanced Materials
The materials used in the creation of web guide systems is developing. Manufacturers are currently exploring new composite materials and alloys with lightweight properties that offer better durability, corrosion resistance and lighter weight, without the loss of performance.
These advances are crucial for businesses operating in extreme environments, like paper and textile production where the systems are subjected to chemicals, moisture and extreme temperature. Utilizing these materials will ensure longer system longevity and lowers the frequency of maintenance or replacements.
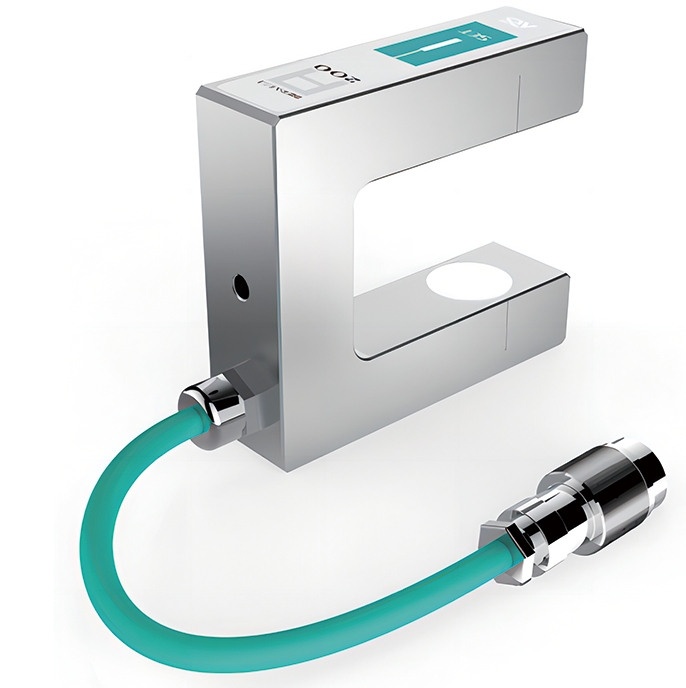
Final Thoughts
The manufacturing of web guide systems is going through rapid changes as industries seek more advanced, faster as well as more effective solutions. From the integration of the latest Industry 4.0 technological advancements to the drive towards energy efficiency and sustainable practices, web guiding system manufacturers are constantly advancing to meet the changing demands of the global market. Since automation is continuing to be the driving force behind the evolution of production lines, the significance of web guiding control systems in the pursuit of alignment, quality and efficiency will become increasingly important across a variety of sectors.