How to Troubleshoot Common Issues in A Web Guide System
A web guide system is an important component in many industries because it ensures perfect alignment and management of webs throughout manufacturing processes. However, as with any complicated system, they may encounter challenges that impair operations on occasion. This article provides a complete guide on troubleshooting common issues in a web guide system to assist organizations in maintaining maximum performance. By understanding these challenges and implementing the appropriate troubleshooting methods, companies can minimize downtime, improve productivity, and ensure smooth operation.
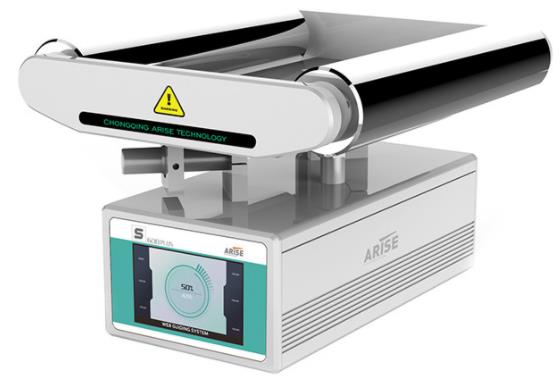
Troubleshooting Methods for Misalignment and Drift in A Web Guide System
Misalignment and drift are common problems in a web guiding system, which occur when the web deviates from its planned course. Follow these steps to successfully troubleshoot these issues:
Check Sensor Calibration: Begin by checking the sensors’ calibration. Ascertain that they are correctly aligned and calibrated in accordance with the manufacturer’s instructions. Recalibrate the sensors as needed to guarantee accurate detection and measurement of the web’s position.
Check Roller Alignment: Poor roller alignment can lead to misalignment and drift. If the rollers are not properly aligned, inspect them and change their places. Align the rollers parallel to one another and perpendicular to the route of the web.
Inspect Mechanical Components: Examine the mechanical components of the web guiding system, including rollers, bearings, and guides. Look for signs of damage, wear, or contamination. Replace any worn-out or damaged components and clean any debris or contaminants that may interfere with the web’s movement.
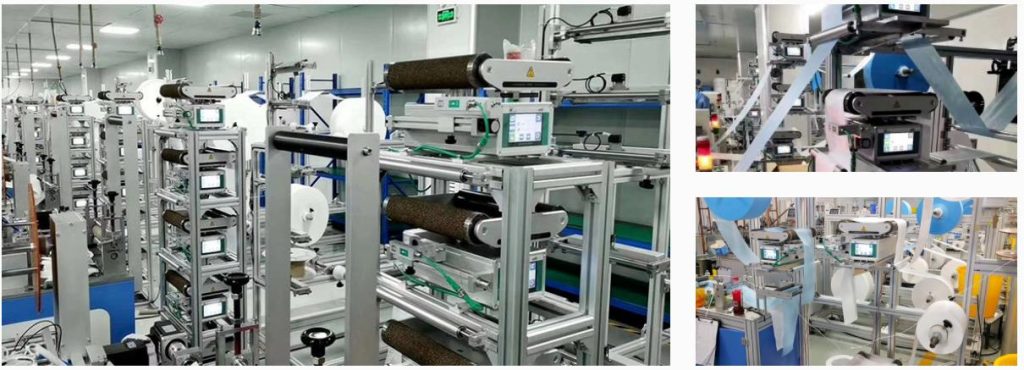
Troubleshooting Methods for Tension Variations in A Web Guide System
Variations in web tension can cause wrinkling, straining, or ripping of the web. Consider the following steps to troubleshoot tension issues:
Check Roller Tensioning: A typical source of tension differences is improper roller tensioning. Ascertain that the tensioning mechanisms are correctly adjusted in accordance with the prescribed tension settings for the specific web material. For the proper tensioning guidelines, consult the system’s documentation.
Maintain Consistent Material Feed: Variations in tension might be caused by inconsistent material feed. Check that the material is being fed through the guiding system consistently and smoothly. Examine the material path for any blockages or irregularities and, if necessary, eliminate them.
Inspect Roller Surfaces: Examine the roller surfaces for any abnormalities or damage that could influence web tension. Check to see if the rollers are clean and free of debris or glue accumulation. To maintain correct tension management, replace any broken or worn-out rollers.
Install Automatic Tension Control Systems: Consider installing an automatic web tension controller that monitors and adjusts tension in real time. These systems use feedback sensors and control algorithms to keep tension constant throughout the manufacturing process.
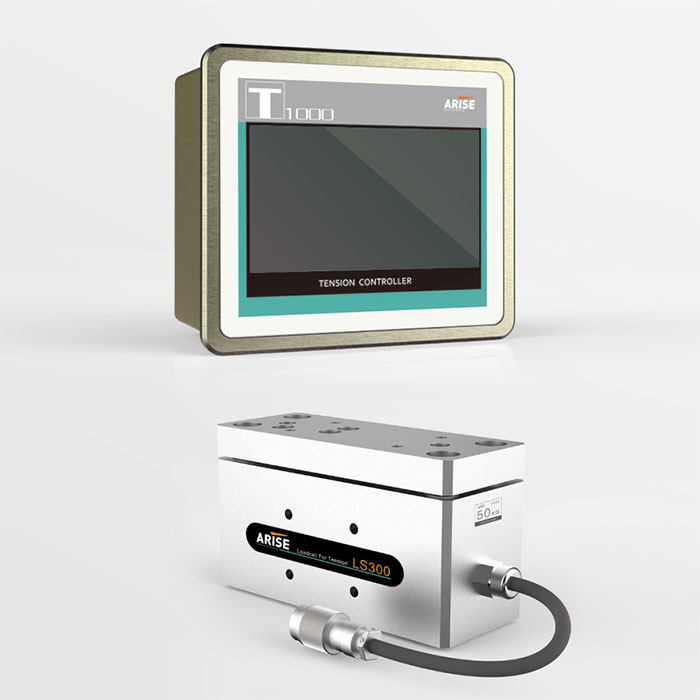
Troubleshooting Methods for Sensor Malfunctions in A Web Guide System
Web guide sensors are required for precise web detection and alignment. When sensors fail, incorrect readings or failure to detect the web can occur. Follow these procedures to troubleshoot sensor issues:
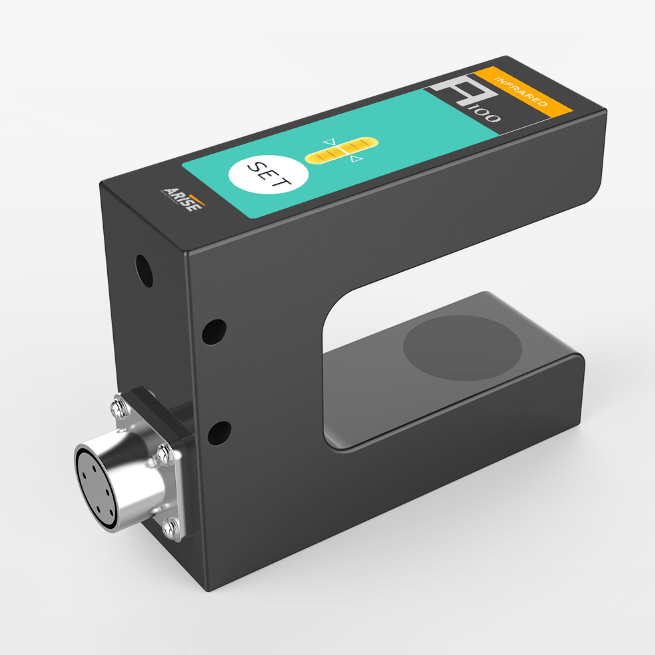
Clean the Sensors: Sensors can acquire dirt, dust, or debris over time, resulting in false readings. Use proper cleaning solutions and lint-free materials to clean the sensors. During the cleaning procedure, take care not to damage or misalign the sensors.
Check Sensor Alignment: Make sure the sensors are properly aligned with the web path. Check that the sensors’ placements are perpendicular to the direction of the web and parallel to one another. Make any necessary modifications to correctly position the sensors.
Verify Electrical Connections: Examine the connections between the sensors and the control system. Check that the connections are secure and free of corrosion or dangling wires. Test the sensor signals to confirm they are properly transmitted to the control system.
Perform Sensor Calibration: Follow the manufacturer’s instructions to calibrate the sensors. Calibration helps establish accurate detection thresholds and ensures consistent performance. Regularly scheduled sensor calibration is essential for reliable and precise web guiding.
Troubleshooting Methods for Control System Errors in A Web Guide System
Software flaws, electrical disruptions, or erroneous settings can all cause control system errors. These issues might cause inconsistent web movement, system response delays, or improper adjustments. Consider the following steps to troubleshoot control system errors:
Verify Software setups: Examine the control system’s software setups and settings. Ascertain that the parameters and thresholds are properly established in accordance with the unique needs of the manufacturing process. For assistance with correct configuration, consult the system’s documentation or contact technical support.
Check Electrical Connections: Examine the electrical connections between control system components such as sensors, actuators, and power supplies. Control system faults can be caused by loose or faulty connections. Repair or replace any broken wiring or connectors and secure any loose connections.
Update Software: If your web guiding system has firmware or software, check for available updates from the manufacturer. Outdated software versions may contain bugs or compatibility issues. Regularly updating the software can improve system stability and performance.
Consult System Documentation and Technical Support: If control system errors persist, refer to the system documentation or contact technical support for assistance. Give specifics about the issues you saw, the system configurations you used, and any troubleshooting measures you took. Technical assistance can make customized advice based on the model and configuration of your equipment.
Troubleshooting Methods for Inadequate Operator Training of A Web Guide System
Inadequate operator training can cause a variety of problems with web guiding systems. Operators may lack the knowledge required to comprehend system parameters, read error warnings, or carry out basic maintenance activities. Consider the following methods to address this issue:
Comprehensive Training Programs: Implement comprehensive training programs that encompass web guidance system operation, maintenance, and troubleshooting. An overview of web guide system components, parameter modification, error interpretation, and routine maintenance procedures should all be covered in training.
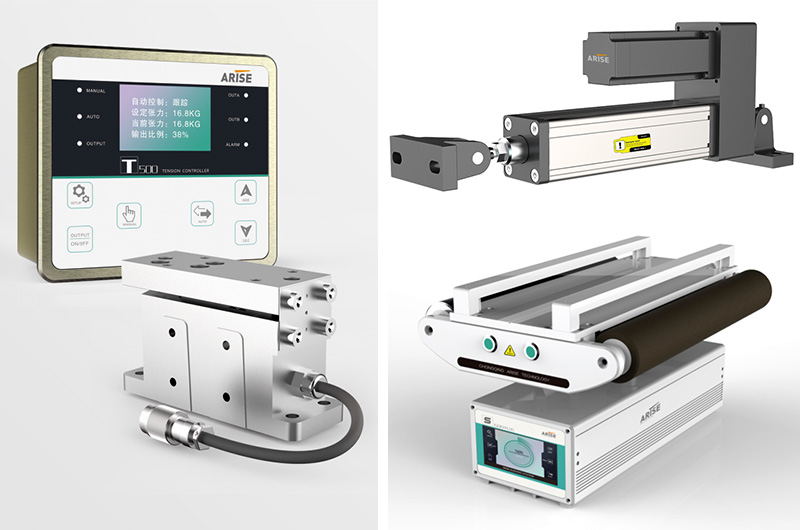
Ongoing Training and Refresher Courses: Provide continuous training and refresher courses to keep operators up to date on system improvements and best practices. Educating operators on system upgrades, new features, and troubleshooting strategies is part of this. Regular training sessions can improve operator knowledge and confidence in efficiently administering the web guide control system.
Summary
How to troubleshoot common issues in a web guide system is critical for maintaining optimal performance and minimizing production interruptions. Businesses can leverage the potential of their web guiding systems by using proactive troubleshooting methods, which improve productivity, reduce downtime, and improve overall operational efficiency.