The Crucial Role of In-Line Inspection Systems for Printing Quality
In printing manufacturing, where precision and perfection are paramount, the integration of advanced technologies has become a cornerstone of achieving and maintaining exceptional quality standards. The emergence of in-line inspection systems has revolutionized the landscape of printing quality assurance, offering a sophisticated solution to ensure flawless output while optimizing production efficiency. This article explores the pivotal role played by in-line inspection systems in ensuring superior printing quality, enhancing efficiency, and elevating customer satisfaction.
Why In-line Inspection Systems are Adopted for Printing Quality
The Significance of Printing Quality
Printing quality is the bedrock upon which the reputation and success of any printing endeavor are built. Whether it’s commercial printing, packaging, labels, or any other application, the end goal remains consistent – flawless prints that captivate the eye and convey the intended message with clarity and precision. However, achieving such perfection amidst the complexities of modern printing processes poses numerous challenges, ranging from color consistency and registration accuracy to defect detection and print uniformity.
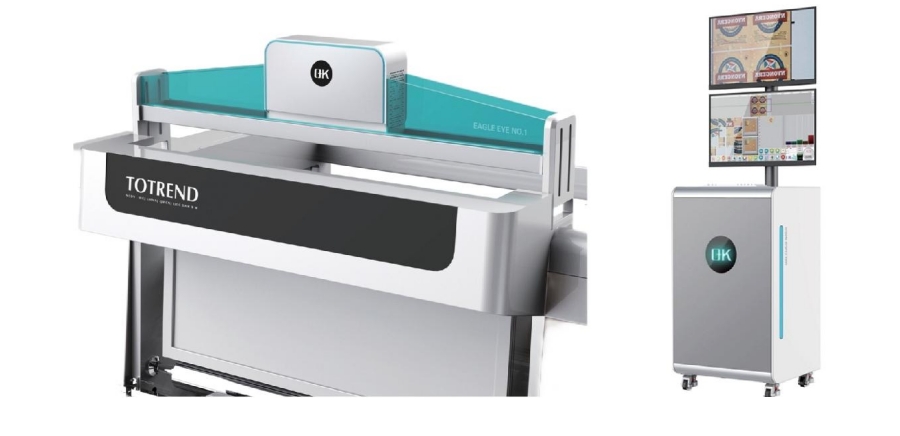
Understanding In-line Inspection Systems
In-line inspection systems are sophisticated technological solutions integrated directly into the printing press or finishing equipment. These systems utilize a combination of sensors, cameras, and advanced software algorithms to scrutinize every detail of the printed material in real-time as it traverses through the production process. Unlike traditional quality control methods reliant on manual inspection, in-line inspection systems offer an automated approach, capable of detecting defects with unparalleled accuracy and efficiency.
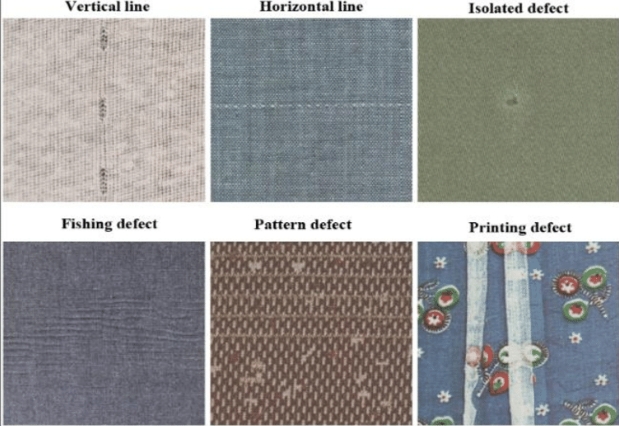
Key Functionality and Capabilities of In-Line Inspection Systems for Printing Quality
1. Defect Detection
- In-line inspection systems utilize high-resolution cameras and sensors to scan printed materials for defects such as ink smudges, streaks, misprints, and registration errors.
- Advanced algorithms analyze captured images to detect deviations from quality standards with unparalleled accuracy and efficiency.
- Real-time defect detection enables immediate corrective action, preventing substandard prints from reaching customers and minimizing the need for costly rework.
2. Color Management
- Consistent color reproduction is critical for maintaining brand identity and visual appeal across printed materials.
- In-line inspection systems monitor color accuracy throughout the production process, ensuring adherence to predefined color profiles and standards.
- By comparing printed colors to reference values, these systems detect and correct any deviations, ensuring uniformity and fidelity across the print run.
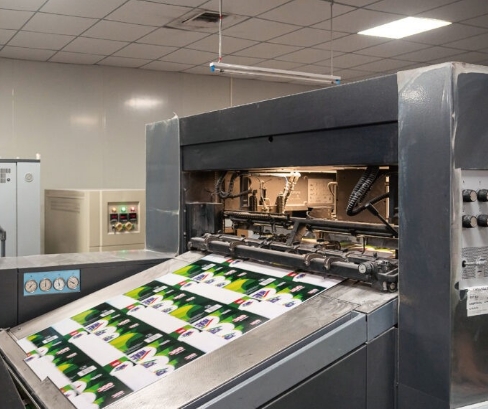
3. Print Registration
- Precise alignment of colors and graphics is essential for achieving professional-quality prints.
- In-line inspection systems verify print registration by comparing the actual position of elements with the intended design.
- By detecting and correcting misalignment errors in real-time, these systems ensure that prints maintain the desired visual integrity and consistency.
4. Print Uniformity
- Beyond individual defects, in-line inspection systems assess the overall uniformity of printed materials.
- Parameters such as density, coverage, and sharpness are analyzed to ensure consistent quality across multiple copies.
- By identifying variations in print quality, these systems enable operators to make adjustments and maintain uniformity throughout the production process.
5. Automated Inspection
- In-line printing inspection systems offer a fully automated approach to quality control, eliminating the need for manual inspection and intervention.
- Integration with printing presses or finishing equipment allows for continuous monitoring without disrupting workflow.
- Automation streamlines the inspection process, optimizing production throughput and minimizing downtime associated with manual intervention.
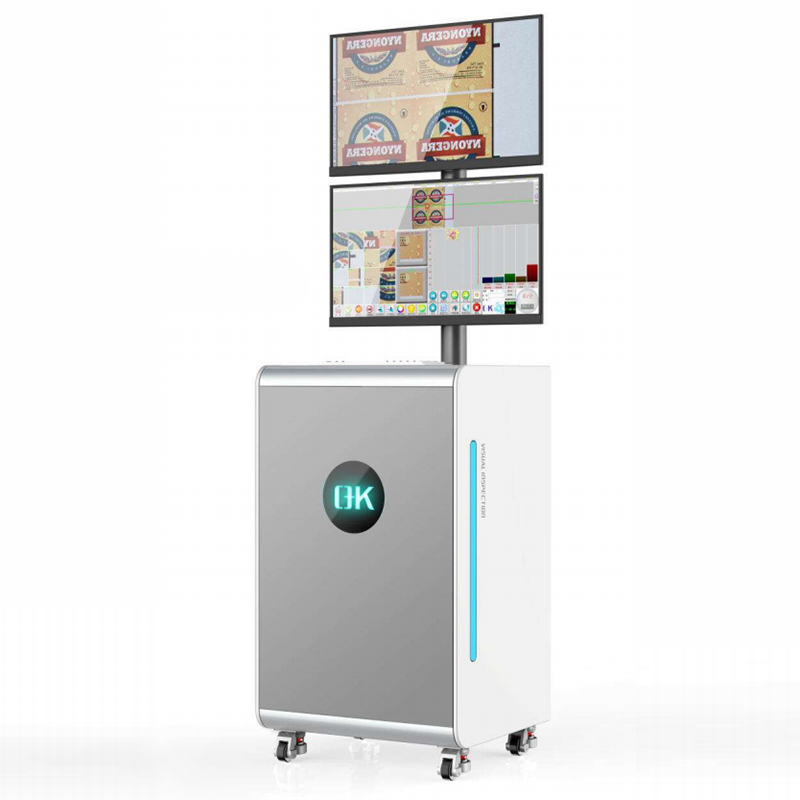
6. Data Analytics and Reporting
- In addition to real-time monitoring, in-line inspection systems generate comprehensive data reports and analytics.
- These reports provide valuable insights into production performance, defect trends, and process optimization opportunities.
- By leveraging data-driven insights, printing companies can implement continuous improvements and drive operational excellence.
Benefits and Impact of In-Line Inspection Systems for Printing Quality
1. Enhanced Quality Control
Real-time defect detection enables proactive intervention to rectify issues before they escalate, minimizing the production of substandard prints and ensuring that only top-quality output reaches the customer.
2. Increased Productivity
Automation streamlines the inspection process, eliminating the need for manual intervention and allowing for continuous monitoring without disrupting production flow. This results in optimized throughput and reduced downtime, ultimately boosting overall productivity.
3. Cost Savings
By preventing defects early in the production process, in-line inspection systems help minimize material waste and avoid costly reprints, leading to significant cost savings for printing operations.
4. Improved Customer Satisfaction
Consistent, high-quality prints instill confidence in customers and enhance their overall experience. By delivering reliable, error-free output, printing companies can strengthen customer relationships and build long-term loyalty.
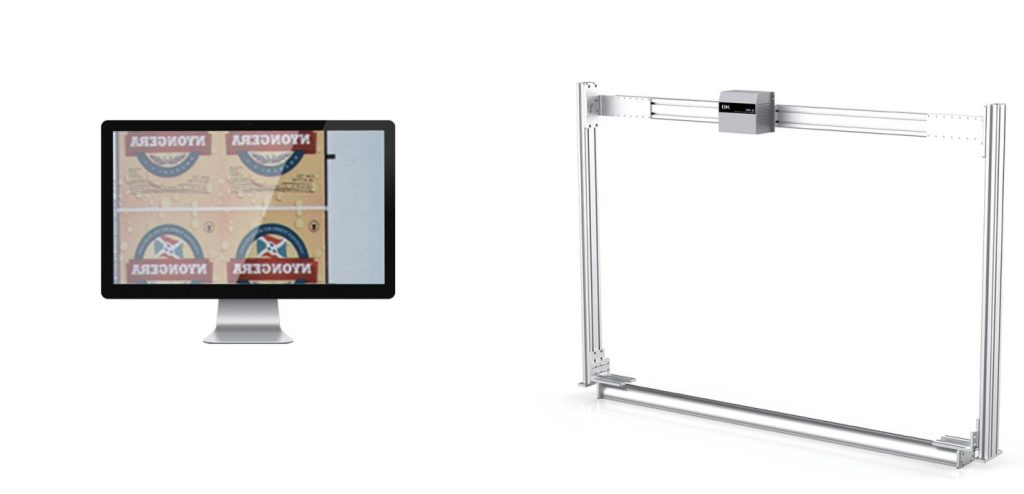
Challenges and Solutions in In-line Inspection Systems for Printing Quality
1. High-Speed Printing
- Challenge: One of the primary challenges is maintaining accuracy and reliability at high production speeds. As printing presses operate at increasingly faster speeds, in-line inspection systems must keep pace to ensure thorough and effective inspection without compromising accuracy.
- Solution: Implementing advanced sensor technology and high-speed image processing capabilities can help in-line inspection systems keep up with the speed of modern printing presses. Additionally, optimizing system configurations and algorithms for efficiency can enhance performance without sacrificing accuracy.
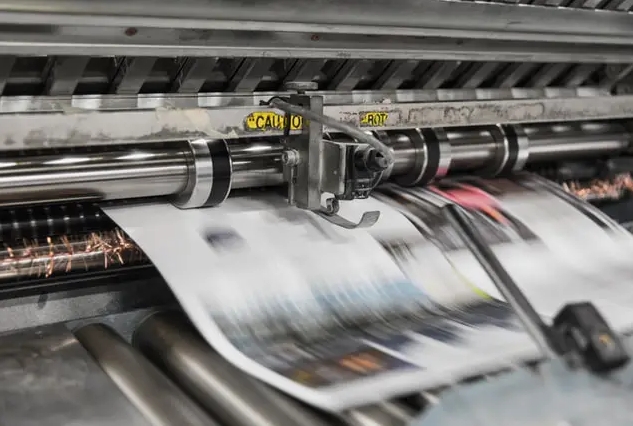
2. Variability in Print Substrates
- Challenge: Printing on different substrates (e.g., paper, cardboard, plastic) can introduce variability in print quality and surface characteristics, posing challenges for consistent inspection.
- Solution: In-line inspection systems should be equipped with versatile sensor technologies and adaptable algorithms capable of accommodating various print substrates. Calibration and fine-tuning of inspection parameters based on substrate characteristics can help ensure accurate and reliable inspection results across different materials.
3. Complex Print Designs
- Challenge: Intricate print designs, such as fine text, detailed graphics, or complex patterns, can present challenges for defect detection and color accuracy.
- Solution: Advanced image processing algorithms and machine learning techniques can enhance the ability of in-line inspection systems to detect subtle defects and ensure accurate color reproduction, even in complex print designs. Training algorithms on a diverse range of print samples can improve their ability to recognize and classify different types of defects.
4. Environmental Factors
- Challenge: Environmental factors such as ambient lighting, temperature variations, and dust particles in the air can affect the performance of in-line inspection systems.
- Solution: Implementing robust hardware designs with built-in environmental controls, such as lighting adjustments and dust protection measures, can help mitigate the impact of environmental factors on inspection accuracy. Regular maintenance and cleaning of inspection equipment are also essential to ensure optimal performance.
5. Integration Challenges
- Challenge:Integrating in-line inspection systems seamlessly into existing printing equipment and workflows can be complex, especially in retrofitting older machinery.
- Solution: Collaboration between printing equipment manufacturers and inspection system providers can facilitate seamless integration by designing compatible interfaces and communication protocols. Flexible mounting options and modular designs can simplify installation and retrofitting processes, minimizing disruption to production workflows.
6. Data Handling and Analysis
- Challenge:Managing and analyzing large volumes of inspection data generated by in-line inspection systems can be challenging, especially in real-time applications.
- Solution: Implementing robust data management systems and analytics platforms capable of processing and analyzing inspection data in real-time can streamline decision-making and enable proactive defect detection. Cloud-based solutions and remote monitoring capabilities can facilitate data storage, analysis, and accessibility.
Conclusion
In-line inspection systems have been powerful tools for printing quality assurance, offering a blend of precision, efficiency, and reliability unmatched by traditional inspection methods. Adopting cutting-edge technologies and automation, these systems not only detect defects but also drive continuous improvement, setting new benchmarks for excellence in printing quality.