The Power of Multi-Sensor Web Inspection Systems: Revolutionizing Quality Control in Manufacturing
In the fast-paced world of manufacturing, maintaining high-quality standards is paramount. To achieve this, companies are increasingly turning to advanced technologies that can provide precise, real-time monitoring and analysis of their production processes. Multi-sensor web inspection systems have emerged as powerful tools that leverage various sensor technologies to monitor and enhance the quality of materials continuously processed in manufacturing.
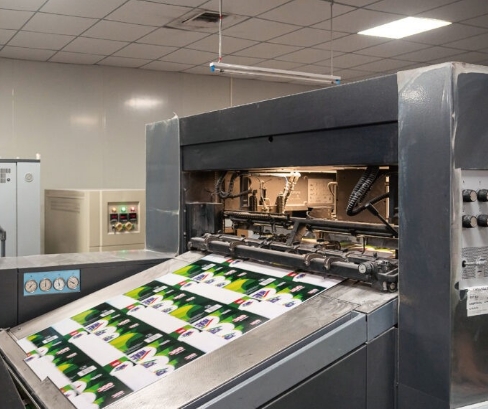
Understanding Multi-Sensor Web Inspection Systems
A multi-sensor web inspection system is an integrated technology that employs various types of sensors to monitor and evaluate the quality of continuous materials, or webs, such as paper, plastic, metals, textiles, and nonwovens, during the manufacturing process. These web inspection systems are designed to detect defects, inconsistencies, and other issues that could compromise the final product’s quality.
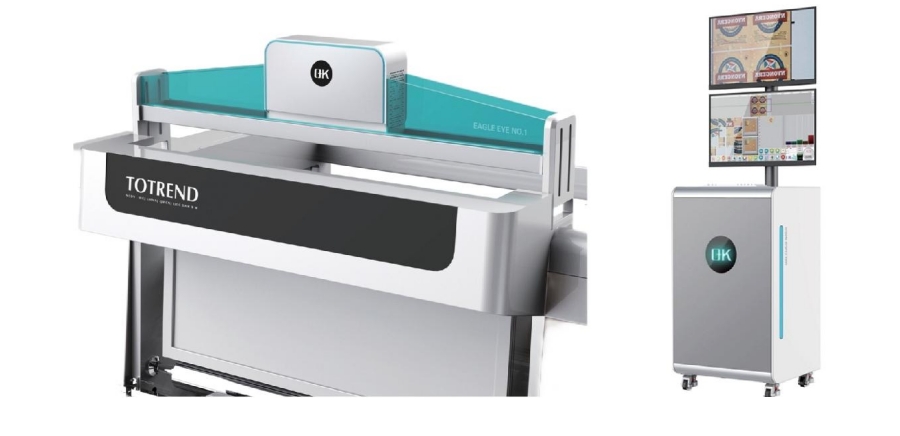
Key Components of Multi-Sensor Web Inspection Systems
1. Optical Sensors
Optical sensors are fundamental for capturing high-resolution images and detecting surface defects on the material.
- High-Resolution Cameras: These cameras are capable of capturing detailed images of the web surface. They can detect a wide range of surface defects, including scratches, holes, stains, and discolorations. Both monochrome and color cameras can be used depending on the specific inspection needs.
- Laser Scanners: Laser scanners use laser beams to scan the surface of the material. They provide precise measurements and can detect minute surface irregularities, such as fine cracks and texture variations.
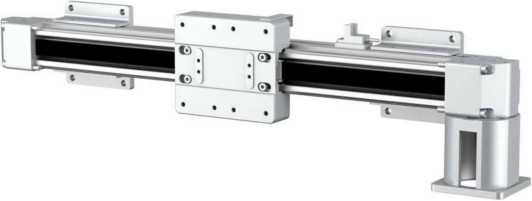
2. Thermal Sensors
Thermal sensors monitor temperature variations across the web, which can indicate underlying issues.
- Infrared (IR) Cameras: IR cameras detect infrared radiation emitted by the web, creating thermal images that show temperature variations. This is useful for identifying problems such as overheating, improper curing, or other thermal inconsistencies.
3. Ultrasonic Sensors
Ultrasonic sensors use sound waves to inspect the internal structure and thickness of the material.
- Ultrasonic Transducers: These devices emit high-frequency sound waves that penetrate the material. By analyzing the reflected waves, ultrasonic sensors can detect internal defects such as voids, delaminations, and thickness variations, providing a non-destructive testing method.
4. X-ray Sensors
X-ray sensors are essential for internal inspection, detecting hidden defects that are not visible on the surface.
X-ray Cameras: These cameras capture images based on the differential absorption of X-rays by the material. They are ideal for identifying internal inconsistencies, such as cracks, inclusions, and density variations, especially in high-precision applications like aerospace and electronics.
5. Magnetic and Eddy Current Sensors
These sensors are used to inspect conductive materials, identifying both surface and sub-surface defects.
- Magnetic Flux Leakage (MFL) Sensors: MFL sensors detect defects in ferromagnetic materials by measuring disruptions in magnetic fields caused by flaws such as cracks or corrosion.
- Eddy Current Sensors: These sensors induce eddy currents in conductive materials and measure the resulting electromagnetic field. Variations in this field can indicate the presence of defects like cracks, inclusions, and other discontinuities.
6. Lighting Systems
Proper lighting is crucial for enhancing the capabilities of optical sensors.
- LED Lighting: LED lights provide consistent, bright illumination, essential for capturing high-quality images. Different configurations (e.g., backlighting, front lighting, and structured lighting) can be tailored to specific inspection requirements.
- Laser Light Sources: Lasers offer concentrated beams of light, highlighting fine surface details and improving the detection capabilities of optical sensors.
7. Image Processing and Analysis Software
Processing and analyzing the data collected by the sensors is critical for defect detection and quality control.
- Image Processing Algorithms: Advanced algorithms process the raw data from sensors, enhancing images and extracting relevant features for defect detection. These algorithms can be customized to identify specific types of defects relevant to the material and application.
- Machine Learning Models: Machine learning models can analyze large datasets to recognize patterns and predict defects with high accuracy. These models continuously improve as they are exposed to more data, enhancing their ability to detect subtle defects and anomalies.
8. Data Management Systems
Efficient data management is necessary for handling the large volumes of data generated by the inspection system.
- Data Storage Solutions: High-capacity storage systems are required to store vast amounts of image and sensor data. Cloud-based storage solutions offer scalability and easy accessibility.
- Data Analytics Tools: These tools analyze stored data, providing insights into the manufacturing process and helping to identify trends and recurring issues. This information is valuable for continuous process improvement and optimization.
9. User Interface and Control Systems
A user-friendly interface and robust control systems enable operators to interact with the inspection system effectively.
- Graphical User Interfaces (GUIs): GUIs provide real-time visual feedback and control over the inspection process, allowing operators to monitor the system’s performance and make necessary adjustments.
- Automated Control Systems: These systems can automatically adjust inspection parameters based on real-time data, optimizing the inspection process and ensuring consistent quality.
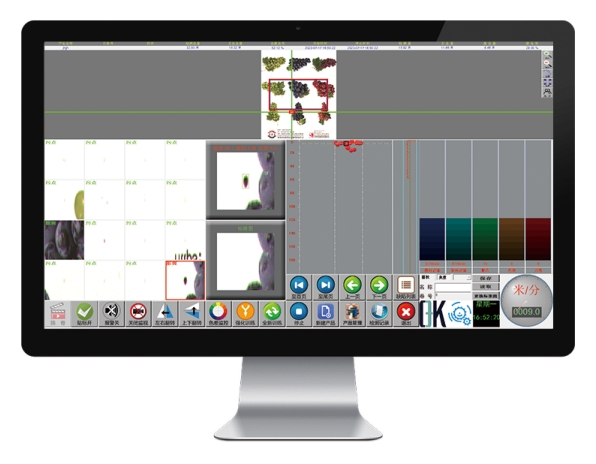
Advantages of Multi-Sensor Web Inspection Systems
Advantage | Description |
Enhanced Accuracy | Combines data from multiple sensors to provide a more comprehensive and precise inspection. |
Real-Time Monitoring | Continuous, real-time inspection allows immediate detection and correction of defects. |
Versatility | Suitable for a wide range of materials and industries, including automotive, textiles, packaging, and electronics. |
Cost-Effectiveness | Reduces costs associated with rework, scrap, and product recalls by identifying defects early. |
Data-Driven Insights | Collects and analyzes data to provide valuable insights for continuous process improvement and optimization. |
Increased Efficiency | Automates quality control processes, leading to faster production rates and reduced downtime. |
Improved Product Quality | Ensures high-quality output by detecting and addressing defects throughout the manufacturing process. |
Scalability | Can be adapted to various production scales, from small batches to large-scale manufacturing. |
Compliance and Standards | Helps ensure compliance with industry standards and regulations by maintaining consistent quality. |
Enhanced Decision Making | Provides detailed, actionable data that supports better decision-making and process adjustments. |
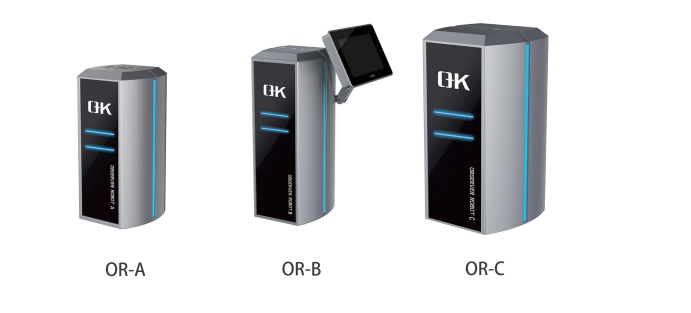
Industrial Applications of Multi-Sensor Web Inspection Systems
1. Automotive Industry
Application: Inspection of metal sheets, coatings, and composite materials.
Benefits
- Surface Defect Detection: Identifies scratches, dents, and other surface imperfections in metal sheets used for car bodies.
- Thickness Measurement: Ensures consistent thickness of coatings and composite layers, which is critical for vehicle safety and performance.
- Weld Inspection: Detects weld defects in automotive parts, ensuring the structural integrity of the vehicle.
2. Textile Industry
Application: Inspection of fabrics, nonwovens, and other textile materials.
Benefits
- Fabric Quality Control: Detects defects such as holes, stains, and uneven dyeing, ensuring high-quality finished products.
- Pattern Verification: Ensures that printed patterns on fabrics are consistent and defect-free.
- Tensile Strength Monitoring: Assesses the tensile strength of textile materials, ensuring they meet industry standards.
3. Packaging Industry
Application: Inspection of plastic films, paperboard, and other packaging materials.
Benefits
- Surface Inspection: Identifies defects such as scratches, tears, and contamination in plastic films and paperboard.
- Dimensional Accuracy: Ensures that packaging materials meet precise dimensional specifications, which is critical for automated packaging processes.
- Seal Integrity: Verifies the integrity of seals in flexible packaging, ensuring product safety and shelf life.
4. Electronics Industry
Application: Inspection of printed circuit boards (PCBs) and electronic components.
Benefits
Component Placement Verification: Ensures that all components are correctly placed and soldered on PCBs.
- Solder Joint Inspection: Detects soldering defects, such as cold joints and bridging, which can affect the performance of electronic devices.
- Trace Inspection: Checks the integrity of conductive traces on PCBs, preventing electrical failures.
5. Paper and Pulp Industry
Application: Inspection of paper and pulp during production.
Benefits
- Surface Quality: Detects surface defects such as wrinkles, tears, and spots, ensuring high-quality paper products.
- Grammage Measurement: Monitors the weight and thickness of paper, ensuring consistency and meeting industry standards.
- Moisture Content: Measures the moisture content of paper, which affects its strength and usability.
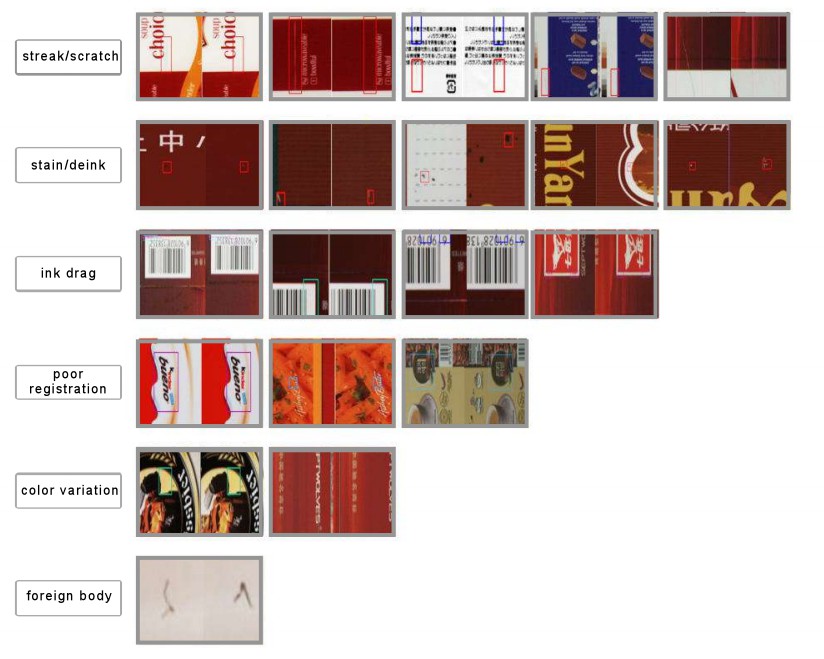
6. Metallurgical Industry
Application: Inspection of rolled metal products, such as steel and aluminum sheets.
Benefits
- Surface Defects: Identifies surface defects like scratches, scales, and pits, which can affect the metal’s properties and usability.
- Dimensional Accuracy: Ensures that metal sheets have consistent thickness and dimensions, critical for further processing and end-use applications.
- Coating Quality: Inspects the quality of coatings applied to metals, ensuring they meet corrosion resistance and aesthetic requirements.
7. Pharmaceutical Industry
Application: Inspection of blister packs, labels, and other packaging materials.
Benefits
- Label Verification: Ensures that labels are correctly printed and positioned, with all necessary information visible and legible.
- Blister Pack Integrity: Detects defects in blister packs, such as incomplete sealing and missing tablets, ensuring product safety and compliance.
- Foreign Object Detection: Identifies foreign objects in packaging, maintaining product purity and safety.
8. Food and Beverage Industry
Application: Inspection of packaging materials and processed food products.
Benefits
- Packaging Inspection: Detects defects in packaging materials, such as plastic films and cartons, ensuring product safety and shelf life.
- Product Uniformity: Ensures uniformity in food products, such as baked goods and processed items, maintaining consistent quality.
- Contaminant Detection: Identifies contaminants in food products, ensuring they meet safety standards.
Challenges and Future Solutions in Multi-Sensor Web Inspection Systems
Multi-sensor web inspection systems offer comprehensive quality control by integrating various sensor technologies. However, their implementation and operation come with significant challenges. Addressing these challenges through innovative solutions is crucial for enhancing the efficiency and effectiveness of these systems.

1. Integration Complexity
- Challenge: Coordinating different types of sensors and ensuring seamless data integration is complex. Each sensor type (optical, thermal, ultrasonic, X-ray, etc.) has unique hardware and software requirements.
- Future Solution: Development of standardized interfaces and protocols for sensor integration. Middleware software can act as a bridge, facilitating seamless communication and data fusion among diverse sensors.
2. Data Management
- Challenge: The sheer volume of data generated by multi-sensor systems can be overwhelming. Efficiently storing, processing, and analyzing this data requires significant computational resources.
- Future Solution: Implementation of edge computing to process data closer to the source, reducing the data load on central servers. Advanced data compression techniques and cloud-based solutions can also help manage large datasets effectively.
3. Cost Considerations
- Challenge: High initial investment and ongoing maintenance costs can be prohibitive, particularly for small and medium-sized enterprises (SMEs).
- Future Solution: Development of modular and scalable systems that allow manufacturers to start with a basic setup and add more sensors as needed. Leasing models and shared service platforms can also make these systems more affordable.
4. System Calibration and Maintenance
- Challenge: Regular calibration and maintenance of multiple sensors are essential for accurate performance, but these processes can be time-consuming and require specialized skills.
- Future Solution: Automated calibration tools and self-diagnostic features can simplify maintenance. Predictive maintenance using AI can anticipate issues before they affect system performance, reducing downtime.
5. Environmental Sensitivity
- Challenge: Sensors, especially optical and thermal, can be sensitive to environmental conditions like dust, temperature fluctuations, and humidity.
- Future Solution: Development of robust sensor housings and environmental control systems within the inspection setup. Advanced algorithms can also compensate for environmental variations during data analysis.
6. User Training and Expertise
- Challenge: Operating and interpreting data from multi-sensor inspection systems require specialized training.
- Future Solution: Enhanced training programs using virtual reality (VR) and augmented reality (AR) to provide immersive and hands-on learning experiences. User-friendly interfaces and AI-driven decision support systems can also assist less experienced operators.
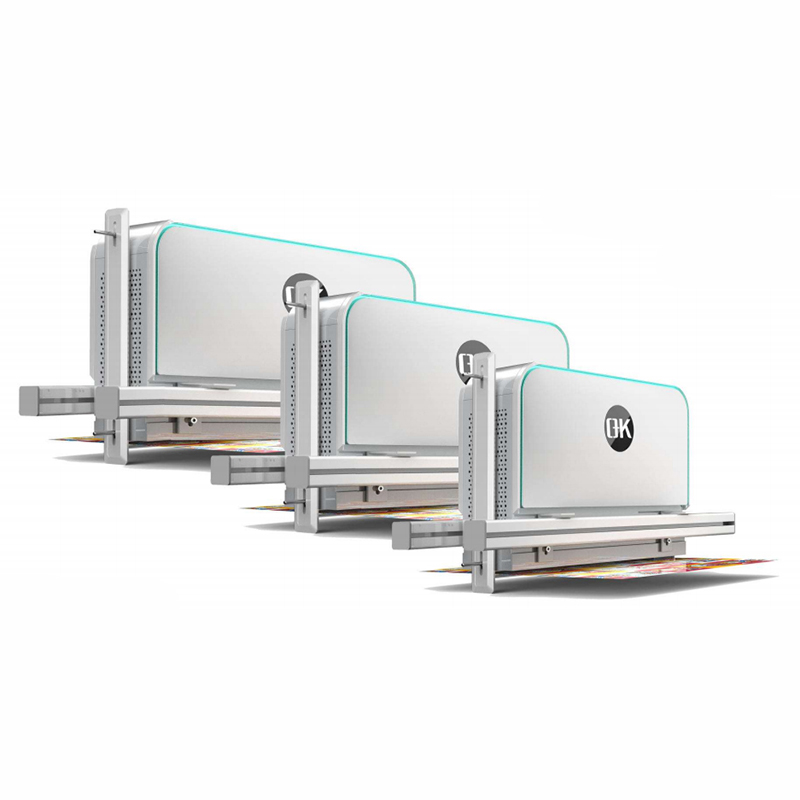
Conclusion
Multi-sensor web inspection systems are revolutionizing quality control in manufacturing. Through the strengths of various sensor technologies, these systems provide comprehensive, real-time monitoring and analysis, helping manufacturers ensure the highest quality standards. The future of manufacturing is poised to be smarter and more efficient, with multi-sensor web inspection systems playing a pivotal role in this transformation.