The Vital Role of Tension Control Systems in Labeling and Packaging Machinery
Tension control systems play a pivotal role in ensuring the smooth and consistent movement of materials such as labels, films, foils, and webs through labeling and packaging machinery. These systems are indispensable for maintaining uniformity, preventing damage, and optimizing the overall quality of packaged goods.
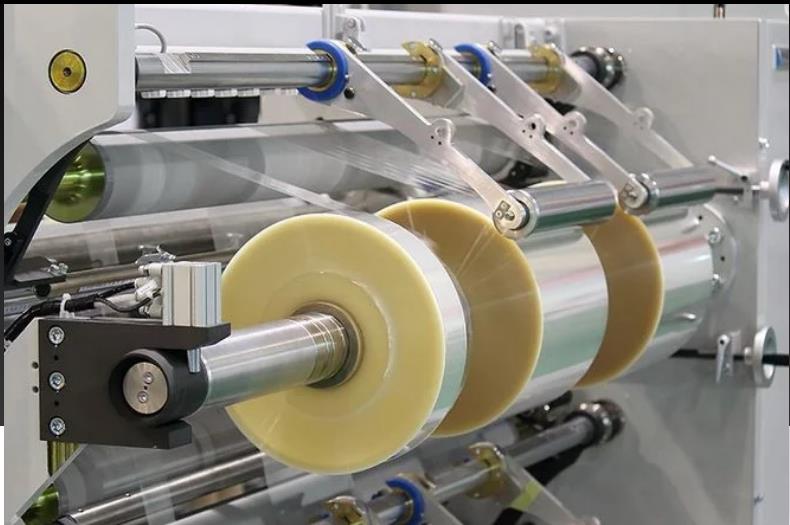
Understanding Tension Control Systems
Tension control systems are mechanisms designed to regulate the tension applied to materials during the packaging process. They operate by precisely controlling the speed and torque of various components involved in material handling, including rollers, brakes, clutches, and motors.
The primary objective of tension control systems is to maintain consistent tension levels throughout the packaging process, regardless of variations in material thickness, speed, or environmental conditions. By achieving this consistency, manufacturers can avoid issues such as wrinkling, tearing, or misalignment of labels and packaging materials, ultimately enhancing product quality and brand reputation.
Key Components of Functions of Tension Control Systems
Component | Function |
Tension Sensor | Measures tension levels in materials such as labels, films, foils, or webs. |
Tension Controller | Regulates the speed and torque of machinery components based on sensor readings. |
Rollers | Guide materials through the machinery, applying controlled tension. |
Brakes/Clutches | Adjust friction or engage/disengage to control material tension. |
Motors | Drive machinery components such as rollers, providing precise tension control. |
Feedback Mechanism | Provides real-time feedback to the controller for continuous adjustment. |
Software Algorithms | Employed for precise calculation and adjustment of tension levels. |
Display/Interface | Allows operators to monitor tension levels and adjust settings as needed. |
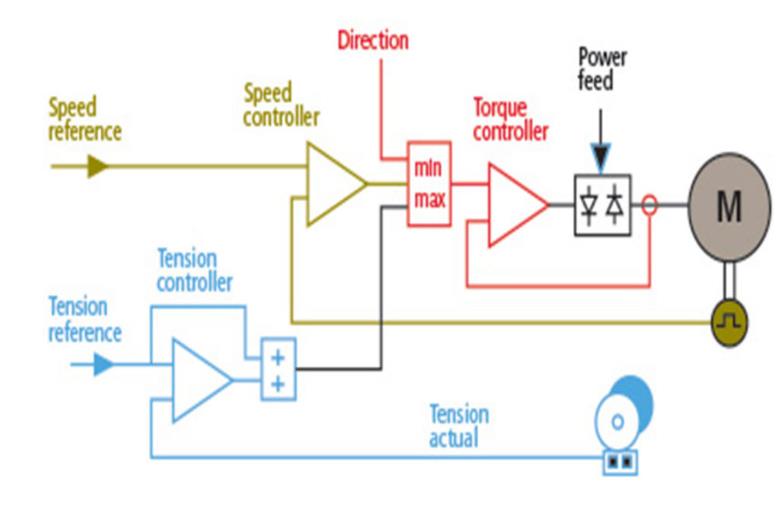
Importance of Tension Control Systems in Labeling Machinery
Tension control systems play a pivotal role in ensuring the quality, accuracy, and efficiency of the labeling process.
1. Precision Label Placement
Tension control systems ensure that labels are fed at the correct speed and tension, allowing for precise placement on products or packaging surfaces. This accuracy is crucial for maintaining brand consistency and conveying essential information effectively.
2. Prevention of Label Damage
By controlling tension levels, these systems prevent labels from stretching or distorting during application. This helps to preserve the integrity of the labels and ensures they adhere smoothly without wrinkles or creases, enhancing the overall appearance of the product.
3. Minimization of Production Waste
Consistent tension control minimizes material waste by preventing misaligned or damaged labels. This reduces the need for rework and lowers production costs associated with discarded materials, contributing to overall efficiency and profitability.
4. Optimized Production Efficiency
With precise tension control, labeling machinery can operate at optimal speeds without compromising label quality. This maximizes throughput and ensures a steady production flow, ultimately increasing overall efficiency and output.
5. Compliance and Regulatory Requirements
Tension control systems help ensure that labels are applied in accordance with regulatory standards and industry requirements. This is essential for compliance with labeling laws and regulations governing product information, safety warnings, and other mandatory labeling elements.
6. Enhanced Brand Image
Consistently well-applied labels contribute to a positive brand image and customer perception. Tension control systems help maintain label consistency and quality, reinforcing brand trust and loyalty among consumers.
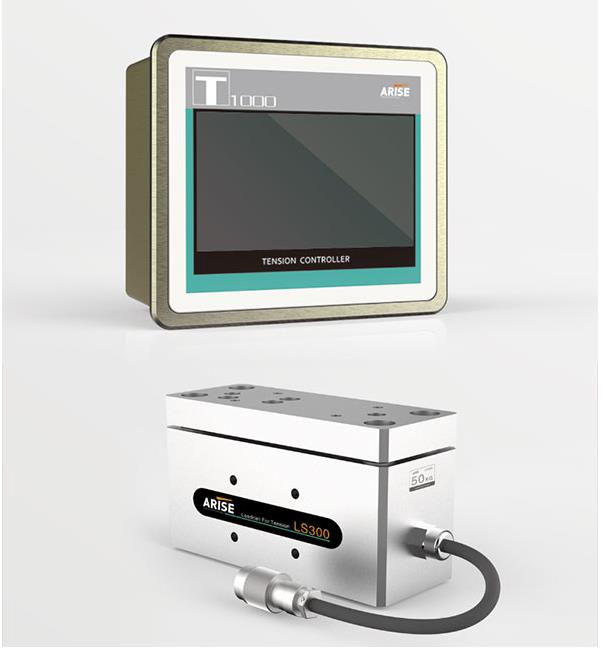
Applications of Tension Control Systems in Packaging Machinery
Tension control systems in packaging machinery serve a variety of crucial functions, contributing to the efficiency, quality, and reliability of the packaging process.
1. Web Handling
Tension control systems are essential for guiding and controlling the movement of flexible materials (referred to as webs) through the packaging machinery. Whether it’s films, foils, or laminates, maintaining consistent tension ensures smooth and uniform material feeding, reducing the risk of wrinkles, tears, or misalignment.
2. Bagging and Pouching
In bagging and pouching applications, tension control systems regulate the tension of packaging materials as they are formed, filled, and sealed. Proper tension control is critical for achieving tight seals and preventing product spillage or contamination.
3. Wrapping and Sealing
Tension control systems play a vital role in wrapping machines, ensuring that materials such as shrink films or stretch films are applied evenly and securely around products. This helps maintain product integrity and prevents damage during transportation and storage.
4. Cartoning
Tension control systems are employed in cartoning machines to manage the tension of carton blanks or packaging materials as they are folded, glued, and sealed. Consistent tension control is essential for producing neatly folded and securely sealed cartons.
5. Case Packing and Palletizing
In case packing and palletizing operations, tension control systems help ensure that packaging materials such as corrugated cardboard or shrink wrap are applied with the right amount of tension to maintain product stability and integrity during transportation and storage.
6. Converting Processes
Tension control systems are used in various converting processes, such as slitting, cutting, and laminating, to ensure precise control over material tension levels. This is essential for achieving accurate cuts, preventing material waste, and maintaining product quality.
Innovations in Tension Control Systems Applied in Labeling and Packaging Machinery
1. Advanced Sensor Technology
Modern tension control systems incorporate advanced sensors that provide real-time feedback on tension levels. These sensors are more accurate and sensitive, allowing for finer adjustments and greater control over the packaging process. Additionally, some systems utilize non-contact sensors, such as ultrasonic or laser sensors, which eliminate the need for physical contact with the material, reducing the risk of damage or contamination.
2. Integrated Servo Drives
Integrated servo drives have revolutionized tension control by offering precise control over motor speed and torque. These drives allow for seamless integration with other machinery components, such as rollers and brakes, enabling synchronized operation and optimal tension management. Additionally, servo drives offer programmable features and customizable profiles, allowing operators to fine-tune tension settings for different materials and packaging requirements.
3. Intelligent Control Algorithms
Tension control systems now utilize sophisticated control algorithms that optimize tension levels based on various factors, such as material properties, machine speed, and environmental conditions. These algorithms employ predictive modeling and adaptive control techniques to anticipate changes in tension requirements and adjust parameters proactively, minimizing errors and maximizing efficiency.
4. Web Guiding Systems
Web guiding systems are an innovative addition to tension control systems, especially in applications involving continuous webs of material. These systems utilize sensors and actuators to detect and correct deviations in web alignment, ensuring that the material remains centered and properly tensioned as it moves through the machinery. By maintaining precise web alignment, web guiding systems prevent edge damage, wrinkles, and misalignment, leading to higher-quality finished products.
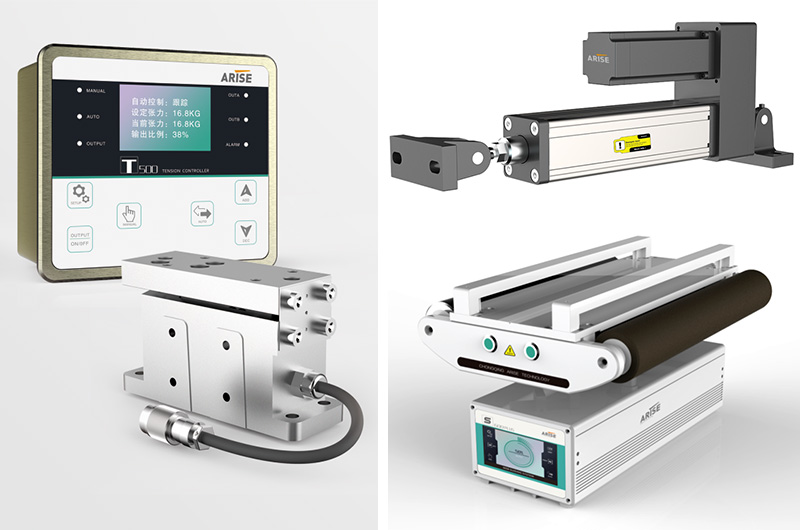
5. Cloud-Based Connectivity and Data Analytics
Some advanced tension control systems offer cloud-based connectivity and data analytics capabilities, allowing operators to monitor and analyze tension data remotely in real-time. This enables proactive maintenance, predictive analytics, and performance optimization, as well as providing insights into production trends and efficiency metrics. By leveraging cloud-based connectivity and data analytics, manufacturers can improve overall equipment effectiveness (OEE) and reduce downtime, ultimately increasing productivity and profitability.
6. User-Friendly Interfaces
Modern tension control systems feature user-friendly interfaces with intuitive controls and graphical displays. These interfaces allow operators to easily monitor tension levels, adjust settings, and troubleshoot issues, reducing the need for specialized training and improving operational efficiency. Some systems also offer touchscreen interfaces and customizable dashboards, allowing operators to configure the display to their preferences and access relevant information quickly.
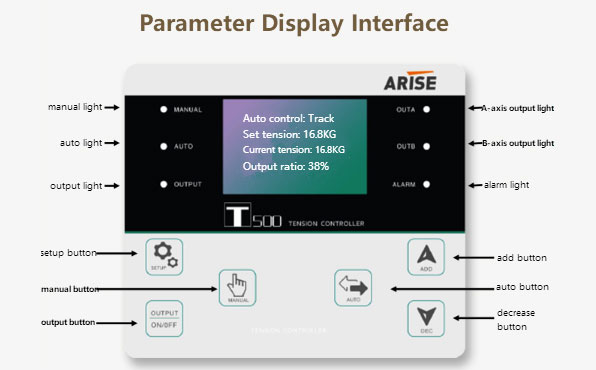
Conclusion
Tension control systems are essential in the labeling and packaging industry, ensuring precision, efficiency, and reliability in every step of the packaging process. As manufacturers strive to meet the demands of an ever-changing market landscape, investing in advanced tension control technologies becomes increasingly essential. By embracing innovation and leveraging the capabilities of advanced tension control systems, manufacturers can position themselves for success in an increasingly competitive industry.