How Printing Inspection Technologies Ensure the Compliance of Regulatory Printing Industry Standards
With increasingly stringent quality standards across industries such as pharmaceuticals, food and beverage, and electronics, companies are turning to advanced printing inspection technologies to ensure that every print output meets specified benchmarks. These technologies not only safeguard product quality but also enhance production efficiency and reduce waste.
Table of Contents
Understanding Regulatory Standards Governing the Printing Industry
This chart summarizes the key regulatory standards governing the printing industry and their specific requirements, depending on the sector.
Regulatory Standard | Description | Industries Affected | Key Requirements |
FDA Labeling Regulations (21 CFR Part 11) | Governs the labeling of drugs, medical devices, and food products, ensuring that printed labels are clear, accurate, and compliant with health regulations. | Pharmaceuticals, Medical Devices, Food & Beverage | Accurate ingredient lists, clear dosage instructions, expiration dates, and compliance with FDA approval processes. |
ISO 12647 | International standard for process control in the production of color prints. Focuses on color consistency and quality across various printing processes. | Commercial Printing, Packaging, Branding | Consistent color reproduction, proper print density, and alignment. |
Food Labeling Requirements (FDA/USDA) | Regulations that require printed labels to include nutritional information, ingredient lists, allergen warnings, and more. | Food & Beverage | Legible text, clear allergen and nutritional information, and readable barcodes. |
UL 969 | Standard for label materials used in product identification. It defines the durability of labels under various environmental conditions. | Electronics, Automotive, Appliances | Labels must withstand heat, moisture, abrasion, and other physical factors. |
GMP (Good Manufacturing Practice) Printing | Ensures that all printed materials used in the pharmaceutical and food industries are produced under strict hygienic and quality-controlled conditions. | Pharmaceuticals, Food & Beverage | Secure and traceable printing, with no cross-contamination or defects. |
REACH (Registration, Evaluation, Authorization, and Restriction of Chemicals) | European Union regulation that ensures labels and packaging do not contain hazardous substances. | Packaging, Cosmetics, Electronics | Labels must disclose material contents and confirm the absence of harmful chemicals. |
CE Marking | A mandatory conformity mark for products sold within the European Economic Area, ensuring compliance with European health, safety, and environmental protection standards. | Electronics, Medical Devices, Machinery | Printed labels must display the CE mark and product specifications. |
BSI Kitemark | A symbol of quality assurance and safety for products manufactured in compliance with British Standards. | Manufacturing, Packaging, Construction | Labels must confirm compliance with specific British Standards for safety and performance. |
REACH (UK) | UK-specific version of REACH, requiring similar compliance to ensure products sold in the UK are free of harmful substances. | Chemicals, Packaging, Textiles | Clear labeling of chemical components and confirmation of safe usage. |
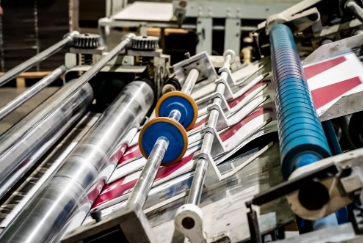
The Growing Need for Print Quality Compliance
Print quality standards vary depending on the industry, but they often include parameters such as color consistency, legibility, barcode readability, print registration, and absence of defects such as smudges, streaks, or misalignment. For sectors like pharmaceuticals, a single misprinted label could mean a compliance violation or even pose a risk to consumer health. Regulatory bodies such as the FDA (U.S. Food and Drug Administration) and ISO (International Organization for Standardization) set the groundwork for quality expectations, which manufacturers must consistently meet.
In this context, human visual inspection, long considered the default approach, is no longer sufficient. It is labor-intensive, prone to fatigue-based errors, and unable to detect subtle but critical defects. This has made printing inspection systems not only desirable but necessary.
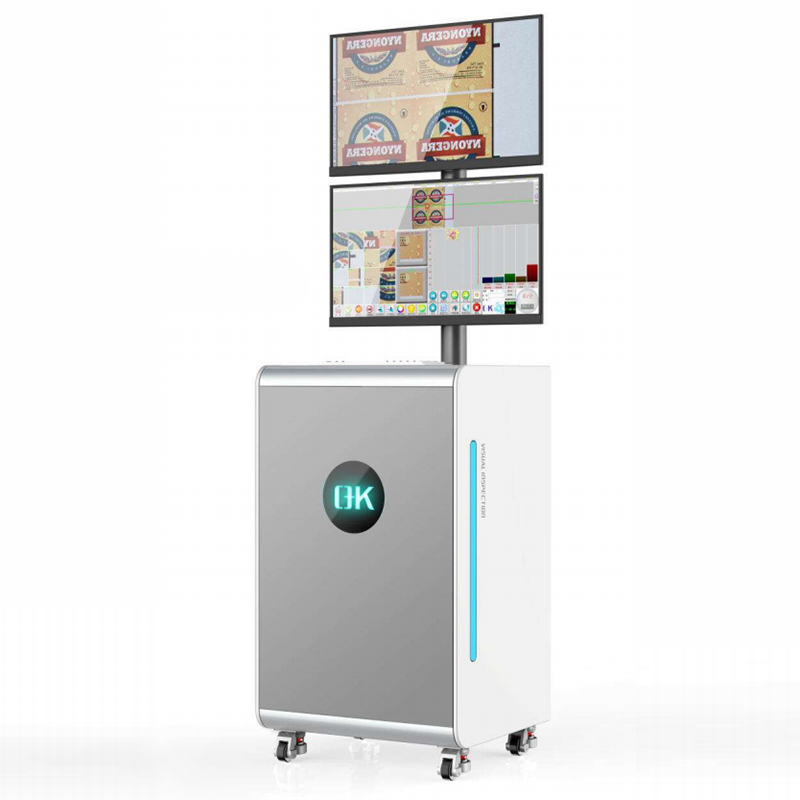
What are Printing Inspection Technologies
Printing inspection technologies are automated systems that use high-resolution cameras, sensors, and software algorithms to monitor, detect, and analyze print quality in real time. These print inspection systems are integrated into production lines—be it offset, flexographic, gravure, or digital printing—to inspect each printed sheet or package with consistency and precision.
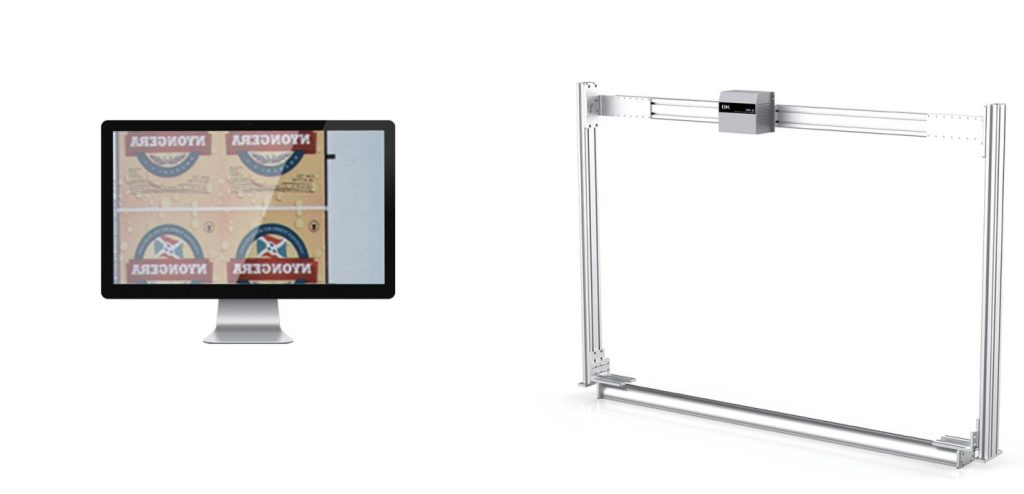
Key Components of Printing Inspection Technologies
Printing inspection technologies are designed to ensure that printed materials meet quality standards, improve production efficiency, and reduce errors. These technologies integrate various components that work together to monitor, detect, and analyze print quality during production.
Component | Description | Function in Inspection |
High-Resolution Cameras | Industrial-grade cameras with precise image capture capability | Capture fine details and detect defects like misprints or smudges |
Lighting System | Uniform LED or strobe lighting for consistent image acquisition | Enhances contrast and ensures defect visibility under all conditions |
Image Processing Software | Algorithms and AI-driven tools for real-time defect detection and pattern matching | Analyzes captured images, compares to references, flags irregularities |
Sensors & Encoders | Motion-tracking hardware that syncs imaging with product movement | Ensures inspection is correctly timed and spatially accurate |
User Interface (UI)/HMI | Touchscreen panels or PCs used to operate, monitor, and adjust the system | Allows operators to configure parameters, view results, and take action |
Data Storage & Reporting | Local or cloud-based storage for inspection data and audit trails | Maintains records for traceability, compliance reporting, and analysis |
Reject Mechanism | Actuator-based device (air jets, arms, diverters) to remove defective items from the line | Ensures only compliant products proceed downstream |
Connectivity Modules | Interfaces for integration with MES, ERP, or quality management systems | Enables data sharing and centralized quality control |
Calibration Tools | Reference targets and software for regular system accuracy checks | Maintains inspection precision over time |
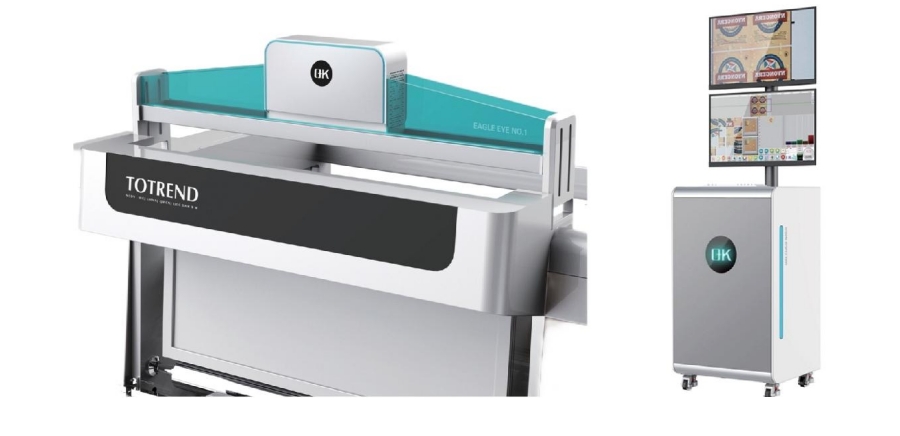
Types of Printing Inspection Technologies
1. Inline Inspection Systems
Inline inspection systems are integrated directly into the production line, allowing for continuous monitoring and real-time defect detection. These systems operate while the printing process is ongoing, providing immediate feedback and enabling quick corrective actions to minimize waste and errors. The primary advantage of inline systems is their ability to inspect prints without halting the production process, ensuring that any defects are detected and addressed as they occur.
The functionality of inline inspection systems is built around high-resolution cameras and advanced image processing software, which work together to capture detailed images of the printed material. As the print moves through the press, the system scans the surface for any deviations from the predefined quality standards. For example, it can detect color mismatches, misalignment, smudges, and other print defects. When an issue is identified, the system immediately alerts operators, enabling them to make adjustments or stop the press if necessary.
These advanced 100% print quality inspection systems are commonly used in high-speed, high-volume print environments such as packaging, label printing, and large-format printing. They ensure that each print job is monitored in real time, making them indispensable for industries where consistency and high standards are critical.
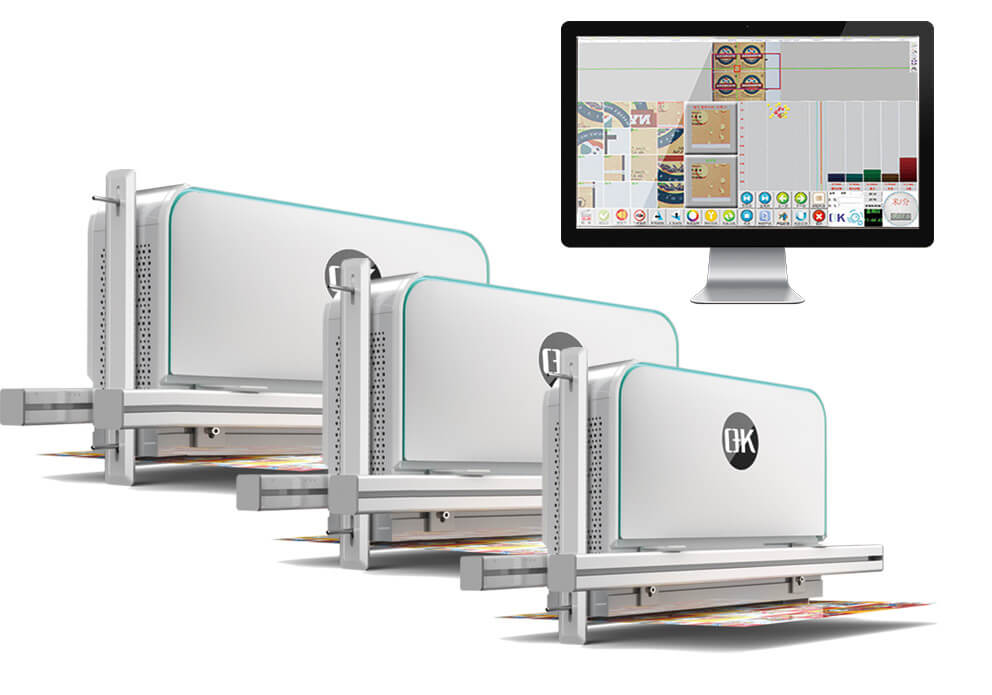
2. Offline Inspection Systems
Unlike inline systems, offline inspection systems are used after the printing process is complete. These systems are typically employed for final inspections, allowing operators to assess the entire batch of printed materials once it has been produced. The printed materials are manually fed into the inspection system for a thorough quality check.
Offline inspection technologies also rely on high-resolution cameras and image processing software, similar to inline systems. However, the key difference lies in the fact that these systems are not integrated into the production line and do not offer real-time monitoring during the print run. Instead, they are used for post-production checks where the quality of the final product is verified before packaging or shipping.
Offline systems are valuable for quality control purposes and for verifying prints that require more detailed inspection, such as security printing, product packaging, or high-end graphics. These systems provide a final assurance that all printed materials meet the required standards and are free from defects.
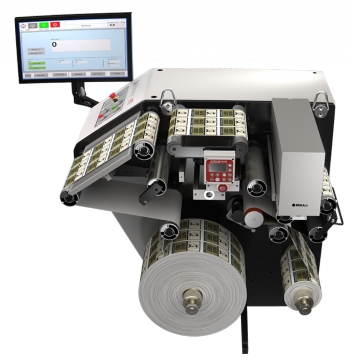
3. Automated Print Quality Control Systems
Automated web inspection systems for print quality control, combine both inline and offline inspection features, offering an integrated approach to ensuring consistent print quality. These systems are capable of monitoring print quality in real-time and can also store data for analysis after the production process is completed. By continuously monitoring the print process and storing data, they allow for adjustments during production and enable further analysis in offline mode.
These systems use a combination of vision sensors, color measurement devices, and software algorithms to ensure accurate print output. They can detect a wide range of defects, including color discrepancies, alignment issues, and other printing errors. The integration of automated feedback loops also means that operators can make adjustments to the printing process while the job is still in progress, improving efficiency and reducing errors.
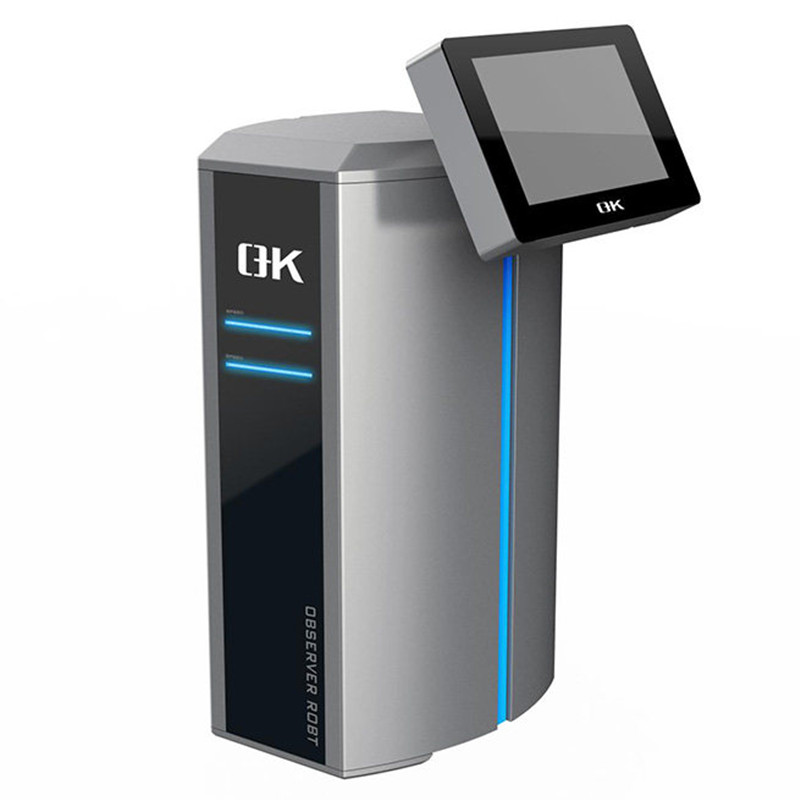
4. Smart Print Inspection Systems
Smart print inspection systems are an advanced iteration of traditional inspection technologies. These systems incorporate machine learning algorithms and artificial intelligence (AI) to not only detect defects but also predict potential problems before they occur. By analyzing vast amounts of data from previous print jobs, these systems can learn patterns and trends in print quality, enabling them to identify anomalies early in the printing process.
The benefit of smart inspection systems is that they improve over time, continuously refining their ability to detect defects and predict issues based on historical data. This technology is particularly useful in complex print jobs, where subtle defects may go unnoticed by traditional inspection methods. Smart print inspection systems are often employed in highly technical print environments, such as those used in printing electronics, security documents, and high-end commercial printing.
5. Hybrid Inspection Systems
Hybrid inspection systems integrate both inline and offline capabilities into a single unit. This hybrid approach provides flexibility in inspecting printed materials at different stages of the production process. For example, prints can be inspected inline as they are produced, but if any issues arise, the system can also perform a detailed offline inspection to ensure the problem is thoroughly understood and corrected.
Hybrid systems are particularly useful in high-volume production environments where both speed and accuracy are essential. They allow manufacturers to monitor print quality in real time while still performing comprehensive post-production checks on batches of printed material. The ability to switch between inline and offline inspection modes makes hybrid systems highly versatile and effective for maintaining high-quality standards.
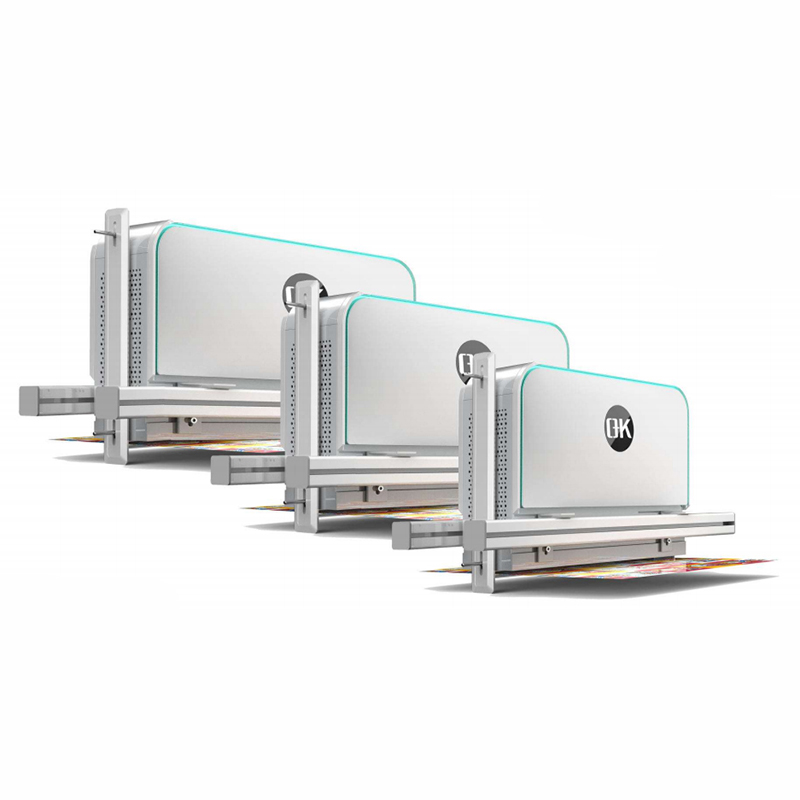
Benefits of Using Printing Inspection Technologies for Compliance with Regulatory Standards
1. Automated Detection of Defects
One of the primary functions of printing inspection technologies is the automatic detection of defects that could cause non-compliance with industry standards. These defects can range from color discrepancies, misalignment, ink smudging, to incorrect or missing labels. By using high-resolution cameras and advanced imaging software, inspection systems can scan the printed materials in real-time, identifying even the smallest flaws that might violate industry-specific standards.
For example, in the pharmaceutical industry, labels must accurately reflect ingredient information, dosage instructions, and expiration dates. Any deviation, even a slight misalignment or color shift, can lead to serious regulatory issues. Printing inspection systems ensure that these vital details are correctly printed, automatically flagging errors before the product reaches the consumer.
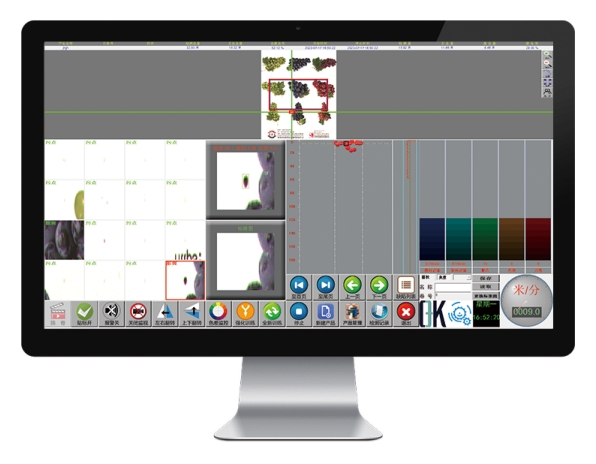
2. Real-Time Monitoring and Feedback
In compliance-driven industries, catching defects as soon as they occur is crucial to avoiding regulatory violations. Inline printing inspection systems monitor the print job continuously during production, providing real-time feedback to operators. This immediate detection allows for prompt corrective actions to be taken, ensuring that non-compliant prints do not progress through the production process.
For example, in packaging for food products, printing regulations may specify that nutritional information and allergens must be clearly visible. If a system detects that the print is too faint or misaligned, operators can immediately adjust the press to prevent non-compliant labels from being produced.
3. Color and Image Accuracy Verification
Certain industries, such as cosmetics, pharmaceuticals, and packaging, have strict requirements regarding color consistency and image accuracy in printed materials. Regulatory standards may specify exact color codes (e.g., Pantone) or image resolutions that must be adhered to for branding and safety reasons. Printing inspection technologies equipped with color measurement tools ensure that the printed materials match the required color standards.
By comparing the printed output against the predefined color profiles and images, the system ensures that every print is in line with regulatory requirements. This is particularly important in sectors where color discrepancies can lead to confusion or misrepresentation of products, such as in food labeling where incorrect colors may imply something is unsafe or misleading.
4. Barcode and QR Code Validation
For industries like pharmaceuticals and logistics, barcodes and QR codes play a critical role in product traceability and verification. Regulatory standards often require that these codes be scannable and accurate for proper tracking, safety checks, and consumer information. Printing inspection systems equipped with barcode verification technology ensure that every code is correctly printed, positioned, and readable by scanners.
These inspection systems verify that the codes comply with the required specifications, such as size, placement, and clarity. This is especially important in industries where counterfeit prevention and traceability are top priorities. A malfunctioning barcode or QR code could lead to regulatory violations and even endanger consumer safety.
5. Data Logging and Reporting for Compliance Audits
Regulatory bodies often require businesses to keep detailed records of print quality inspections for auditing purposes. Printing inspection technologies assist in maintaining these records by logging detailed data about each print job. This data can include defect rates, corrective actions taken, and even environmental factors like temperature and humidity that could affect print quality.
These logs provide the necessary documentation to demonstrate that compliance requirements were met during production. In case of an audit, businesses can present this data to prove that all printed materials met the regulatory standards. This transparency helps avoid penalties and supports the business’s reputation as a compliant, quality-focused manufacturer.
6. Traceability of Print Jobs
Traceability is a key element in ensuring compliance with printing industry standards, particularly for sectors like pharmaceuticals, food packaging, and consumer goods. Printing inspection technologies offer traceability features, allowing manufacturers to track and document every stage of the printing process. From raw material handling to finished product inspection, the entire print job can be traced, ensuring that it meets regulatory requirements.
For example, in the pharmaceutical industry, traceability ensures that all printed packaging materials, including labels with vital drug information, can be tracked back to the production lot. This is crucial in the event of a product recall, as it ensures that all affected materials are identified and removed quickly from circulation.
7. Detection of Missing or Incorrect Information
Many regulations require that specific information appear on printed materials, such as expiration dates, batch numbers, ingredient lists, and safety warnings. Missing or incorrect information can lead to serious legal and financial consequences. Printing inspection systems ensure that this critical information is not only present but also correctly formatted and legible.
These systems can also validate that regulatory-required symbols and certifications are included, such as recycling logos, quality assurance marks, or safety symbols. If any required information is missing or incorrectly printed, the system will flag it immediately, preventing non-compliant materials from reaching consumers or retailers.
8. Adherence to Specific Industry Standards
Each industry has its own set of printing standards that must be adhered to, and failure to comply can result in costly penalties or damage to brand reputation. Printing inspection technologies are specifically designed to cater to these varying needs. For example, in the food industry, label printing must adhere to strict guidelines regarding font size, layout, and font legibility. In electronics, printed circuit boards must meet precise tolerances and layout specifications.
By configuring inspection systems to the unique regulatory requirements of each industry, manufacturers can ensure that they are consistently meeting the required standards.
9. Minimizing the Risk of Human Error
Manual inspection methods can be prone to human error, especially when working with high-speed, high-volume print jobs. Printing inspection technologies eliminate this risk by automating the process, ensuring that regulatory standards are consistently met. Human operators can oversee the process and intervene only when necessary, while the inspection system handles the bulk of quality control.
This minimizes the chances of oversight, where human inspectors might miss defects that could lead to regulatory non-compliance. Automated inspection ensures a higher degree of accuracy and reliability, reducing the likelihood of costly mistakes.
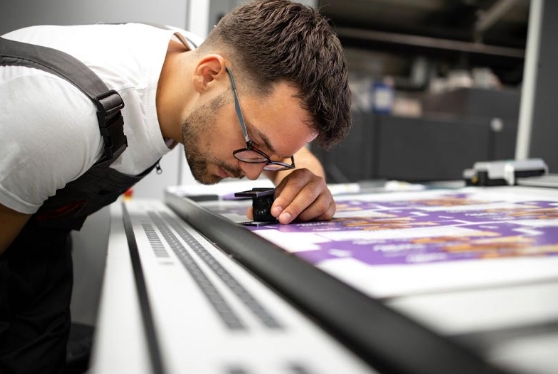
Summary
Printing inspection technologies provide essential tools for ensuring compliance with regulatory printing industry standards. Through automatically detecting defects, verifying accuracy, logging data for audits, ensuring the correct information is printed, etc, these technologies help businesses stay in line with industry regulations. With the increasing complexity of print jobs and the growing need for compliance across various industries, these technologies are indispensable for manufacturers who need to produce high-quality, compliant printed materials consistently.